In material extrusion, plastic filament is fed through a heated extruding nozzle and deposited onto the building platform layer by layer.
What is Material extrusion?
Material extrusion is an additive manufacturing technique using continuous thermoplastic or composite material filament to construct 3D parts. The plastic filament is fed through an extruding nozzle, which heats the material to a molten state and then deposits it layer by layer onto the building platform to create a 3D part.
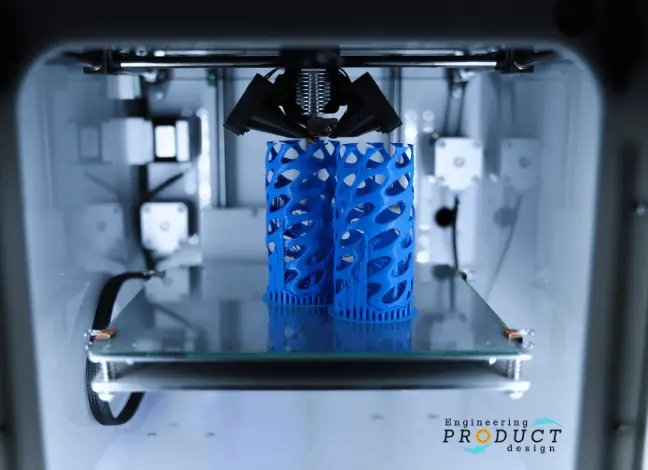
Material extrusion is now the most popular additive manufacturing process in terms of availability for general consumer demand and quality under the Fused Deposition Modeling (FDM) type of printer.
As per ISO/ASTM 52900:2021, it is one of the 7 Additive manufacturing processes. You can read the other types here.
How does Material Extrusion work?
Material extrusion printers typically have a build platform and a printing nozzle head gantry in a three-axis system. The schematic image shows that the printing head gantry moves in X & Y while the build platform moves in the Z-axis. Variants of this printer configuration include Cartesian, CoreXY, delta, SCARA, belt, H-bot, and polar.
Part Preparation – The 3D model is converted into layer-based information – Read our “How AM works?” article to understand how the model is converted by slicing software.
Machine set up – The printer is loaded with thermoplastic filament in spools or pellets. This will depend on the printer manufacturer and material extrusion types.
Printing – The extrusion nozzle head move along the X-Y plane which allows the nozzle tip to move and will start depositing the material layer by layer in predefined areas to cool and solidify.
The following video by Solid Concepts explicitly outlines the Material extrusion process.
FDM technology (Source:Solid concepts)
Material extrusion types
Material extrusion technology was first developed in the 1980s by S. Scott Crump under the registered name of Fused Deposition Modelling (FDM). The term fused deposition modelling (FDM) and its abbreviation FDM are trademarked by Stratasys Inc., a company co-founded by Scott Crump.
Since FDM’s inception, new material extrusion technologies have emerged with slight variations.
- Fused Deposition Modeling (FDM)
- Fused Filament Fabrication (FFF) – Plastic Jet Printing
- Pellet Extrusion
- Composite Filament Fabrication (CFF)
- Direct Ink Writing (DIW)
- Bound Metal Deposition(BMD) / ADAM
Fused Deposition Modeling (FDM)
Developed by Stratasys, FDM is one of the earliest and most well-known forms of material extrusion. It involves melting thermoplastic filaments and depositing them layer by layer to create a 3D object.
Read our ultimate guide to Fused Deposition Modeling, which details the FDM process, its pros and cons and the material choices.
Fused Filament Fabrication (FFF) – Plastic Jet Printing
Similar to FDM, Fused Filament Fabrication is a term often used interchangeably. It’s a more open term for similar processes that utilise melted filament for layer-by-layer printing. This method is not limited by proprietary technologies.
Fused filament fabrication (FFF) is developed by the members of the RepRap project which is not restricted to use by others. You can read all about RepRap here. This is also referred to as Plastic Jet Printing.
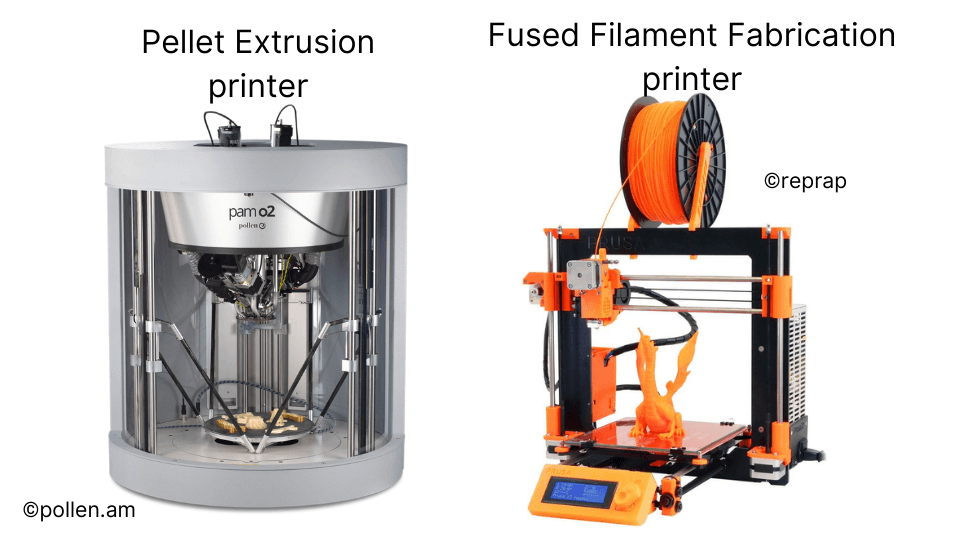
Pellet Extrusion
This technique involves using raw plastic pellets instead of filaments. In Pellet Extrusion, the pellets are melted and extruded through a nozzle to create the layers.
The most significant advantage of Pellet extrusion technology is its material availability. Pellets are the most widely available and used polymer format in the manufacturing industry. Hence, Pellet Extrusion benefits from an established supply chain with lower material costs.
How does Pellet Extrusion Work?
As the image shows, the extruder consists of an auger screw, extruder die, heating elements, and a material cartridge for the pellets. The process works very similar to an injection moulding machine in how it melts the pellets and pushes the molten plastic through the nozzle.
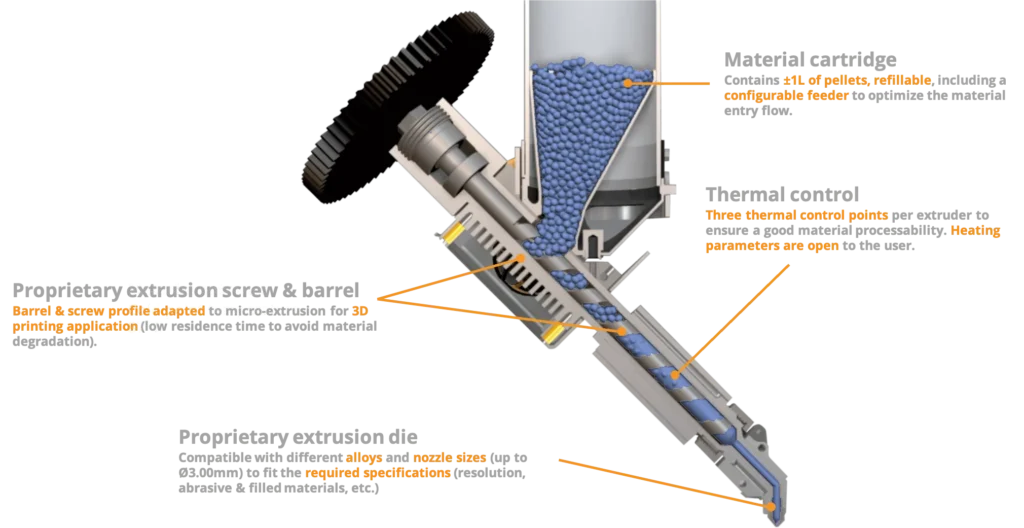
The printer head is then articulated by an XYX gantry system to print the parts as per the 3D model.
Composite Filament Fabrication (CFF)
What is Composite Filament Fabrication (CFF)?
Composite Filament Fabrication (CFF) adds continuous fibre strands such as carbon or fibreglass reinforcement to create composite, lightweight yet metal-like solid parts. CFF material extrusion technology, which uses two print nozzles, was introduced by Markfroged.
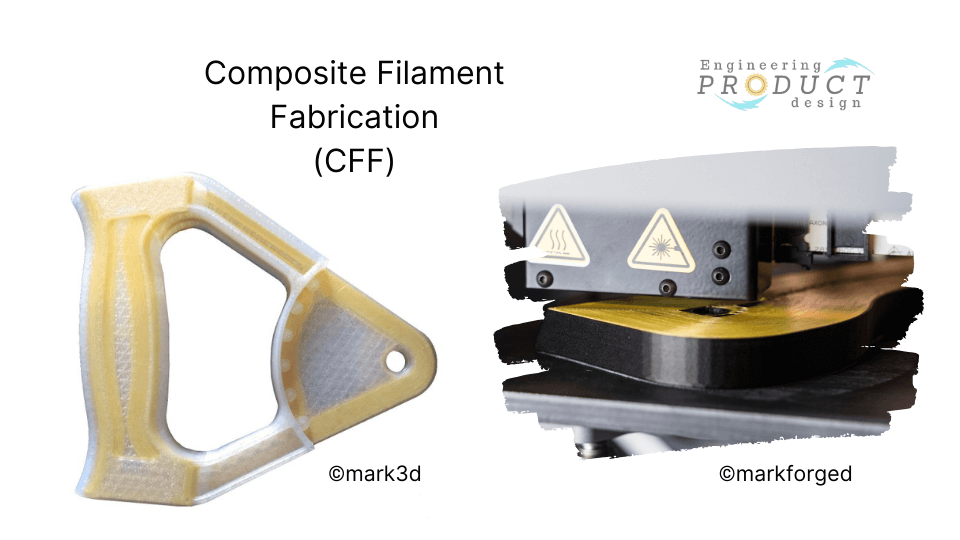
CFF is very similar to reinforced concrete with rebar. Like rebar reinforcement increases the strength of the brittle concrete, in CFF, the continuous fibre increases the strength of the part by increasing the strength.
Fibreglass | Fiberglass is sturdy and comparably cost-effective and increases the part strength. |
Carbon Fibre | Carbon Fibre is stiff and strong and behaves like aluminium alloy 6061. It is used for lightweight parts that carry medium to heavy loads. |
Kevlar | Kevlar would make high-toughness and shock resistance parts, making it ideal for parts that undergo shock loading and are high-impact. It bends instead of breaking. |
HSHT Fiberglass | High Strength High Temperature (HSHT) Fiberglass is a good candidate for high-temperature applications as it maintains strength and stiffness. This is because of its high heat-deflection property. |
How does Composite Filament Fabrication Work?
Composite Filament Fabrication printing steps
- The CFF process begins by extruding and depositing a thermoplastic layer, which forms the part’s infill and shells. This serves as the composites’ matrix material.
- Next, the continuous fibre is introduced into the matrix, which fuses with the thermoplastic using compatible resin coating.
- The above process is repeated layer by layer to create a composite structure with fibres as the backbone of the 3D-printed part.
Composite Filament Fabrication advantages
- High strength-to-weight ratio – Like conventional concrete and rebar, continuous fibres with thermoplastic materials create parts with exceptional strength-to-weight ratios, making them strong and lightweight.
- Design flexibility – Since fibres form the backbone, they can be laid out in specific orientations or patterns to optimise the part’s functionality.
- Part feature enhancement – Fibres can be placed in specific areas to increase localised strength per the part’s functionality.
Composite Filament Fabrication disadvantages
- Cost – As with any other 3D printing technology, initial equipment costs are high, which drives the manufacturing cost higher.
- Post-processing – Depending on the part design and final use, manufacturers might need post-processing techniques such as curing and heating.
Direct Ink Writing (DIW)
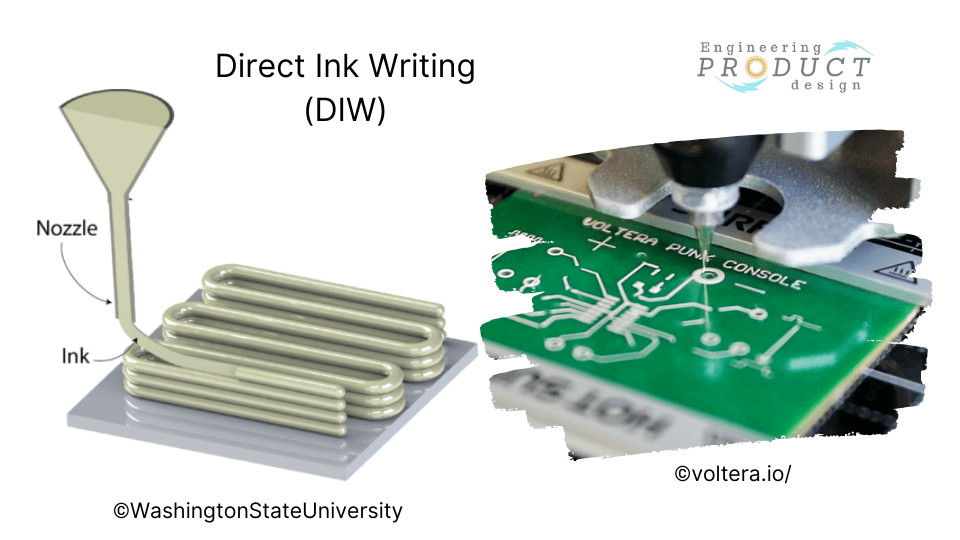
Direct Ink Writing (DIW)is another material extrusion technology variation predominantly employed at meso- and micro-scales. This method dispenses liquid-phase “ink” through tiny nozzles at controlled flow rates, depositing it along digitally defined paths to construct 3D structures layer-by-layer.
The DIW process can achieve very high material resolution, enabling the development of embedded circuitry and rapid manufacturing of sensors. Compared to traditional manufacturing, DIW eliminates masking and etching steps in electronic manufacturing.
Bound Metal Deposition (BMD)
BMD is a metal extrusion-based AM technology process where the metal powder-filled thermoplastic rods are extruded to create 3D parts. Instead of filament spools and pellets, bound metal rods, which are metal powders held together by either wax or polymer binders, are used. BMD is also known as Atomic Diffusion Additive Manufacturing (ADAM).
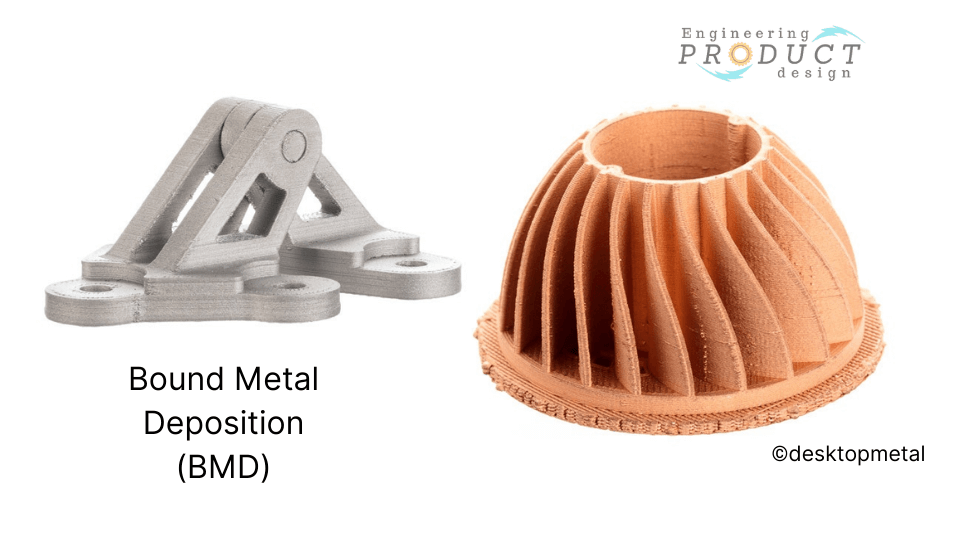
Desktop Metal’s patented process is called Bound Metal Deposition (BMD), while Markforged Inc. named their AM process Atomic Diffusion Additive Manufacturing (ADAM).
Advantages and Disadvantages of Material Extrusion
Advantages of Material Extrusion
- Wide selection of print material
- Easily understandable printing technique
- Easy and user-friendly method of material change
- Low initial and running costs compared to other AM techniques
- Comparably faster print time for small and thin parts
- Printing tolerance of +/- 0.1 mm (+/- 0.005″)
- No supervision required
- Small equipment size compared to other AM
- Comparably low-temperature process
Disadvantages of Material Extrusion
- Visible layer lines
- The extrusion head must continue moving, or else the material bumps up
- Supports may be required
- Poor part strength along the Z-axis (perpendicular to the build platform)
- Finer resolution and wider area increase print time.
- Susceptible to warping and other temperature fluctuation issues such as delamination
- Toxic print materials
Material extrusion materials
Although a variety of materials can be used in material extrusion, thermoplastics like acrylonitrile butadiene styrene (ABS), aliphatic polyamides (PA, also known as Nylon), high-impact polystyrene (HIPS), polylactic acid (PLA), and thermoplastic polyurethane are the most popular.
Lately, material extrusion 3D printing has successfully extruded paste-like materials like ceramics, concrete, and chocolate, as well as plastic materials like polyether ether ketone (PEEK) and polyetherimide (PEI).
As long as the base thermoplastic material is present sufficiently to ensure fusion between the layers, material extrusion can also be used with composite materials. This implies that components made of printed materials can contain components made of wood, metal, or even carbon fibre.
Material | Key properties |
---|---|
ABS (Acrylonitrile Butadiene Styrene) | Strength, Impact Resistance, Durability |
PLA (Polylactic Acid) | Biodegradability, Ease of Printing, Low Warping |
Nylon (Aliphatic Polyamides) | Toughness, Flexibility, Chemical Resistance |
HIPS (High-Impact Polystyrene) | Rigidity, Impact Resistance, Smooth Finish |
TPU (Thermoplastic Polyurethane) | Elasticity, Abrasion Resistance, Flexibility |
PEEK (Polyether Ether Ketone) | High-Temperature Resistance, Chemical Resistance |
PEI (Polyetherimide) | High Strength, Flame Resistance, Dimensional Stability |
Fiber Reinforced Filaments | Enhanced Strength, Stiffness, Lightweight |
Metal-Infused Filaments | Metallic Finish, Conductivity, Mechanical Strength |
Wood-Infused Filaments | Natural Appearance, Texture, Wood-like Characteristics |
Ceramic Filaments | Heat Resistance, Smooth Surface Finish, Non-conductive |
Material extrusion applications
Material extrusion can produce non-functional prototypes, production jigs, and small pre-production batches for testing and concept models.
During the embodiment design stages of product design, it can make rapid prototyping for multiple iterations cost-effective.
Material | Applications |
---|---|
ABS (Acrylonitrile Butadiene Styrene) | Prototyping, Automotive Parts, Electronics Casings |
PLA (Polylactic Acid) | Prototyping, Medical Devices, Food Packaging |
Nylon (Aliphatic Polyamides) | Gears, Bearings, Functional Prototypes |
HIPS (High-Impact Polystyrene) | Prototyping, Models, Display Items |
TPU (Thermoplastic Polyurethane) | Flexible Components, Phone Cases, Footwear |
PEEK (Polyether Ether Ketone) | Aerospace Components, Medical Implants, Automotive |
PEI (Polyetherimide) | Electrical Components, Aerospace Parts, Automotive |
Carbon Fiber Reinforced Filaments | Automotive Parts, Aerospace Components, Prosthetics |
Metal-Infused Filaments | Jewellery, Prototyping for Metal Parts, Decorative Items |
Wood-Infused Filaments | Furniture Prototyping, Decorative Objects, Artifacts |
Ceramic Filaments | Prototyping for Ceramics, Artwork, Custom Pottery |
What Is the Difference Between Material Jetting and Material Extrusion?
Material jetting and Material extrusion are two different 3D printing technologies that differ in their processes and mechanisms.
Material Jetting operates similarly to inkjet printing. It involves jetting tiny droplets of photopolymer materials onto a build platform. These droplets are often cured with UV light to solidify and form layers. This process is repeated layer by layer until the object is fully printed.
Material extrusion involves the deposition of molten thermoplastic filament through a heated nozzle onto a build platform. The nozzle moves according to the design specifications, laying down layers of material that fuse together upon cooling to form the final object.
Property | Material Jetting | Material Extrusion |
---|---|---|
Material | photopolymers or resins that solidify under UV light are used in material jetting. These materials can produce high-resolution prints with fine details and smooth surface finishes. | A wide range of thermoplastics, such as PLA, ABS, PETG, and more, can be used in material extrusion. The choice of material affects properties like the final print’s strength, flexibility, and temperature resistance. |
Accuracy & Resolution | Material jetting offers high resolution and accuracy, making it suitable for applications requiring intricate details and precise dimensions. | While material extrusion can produce detailed prints, its resolution might be lower than that of material jetting. Layer lines might be more visible, affecting the surface finish. |
Post-processing | Often, parts produced by material jetting may require additional post-curing to achieve optimal mechanical properties and surface finish. | Parts printed through material extrusion often require less post-processing. However, smoothing techniques or additional treatments might be applied to improve surface quality. |
Recommended reference
Diegel, Olaf, et al. A Practical Guide to Design for Additive Manufacturing. Springer Nature Singapore, 2019.
Celik, Emrah. Additive Manufacturing: Science and Technology. Walter de Gruyter GmbH, 2020.
Stratasys. Stratasys – Industrial 3D Printing Manufacturers, https://www.stratasys.com/en/Desktop Metal. Desktop Metal. Define the future. Make it real. | Desktop Metal, https://www.desktopmetal.com/.
No comments:
Post a Comment