Selective laser sintering uses a laser to melt and fuse fine polymer particles of material to create 3D objects.
What is Selective Laser Sintering?
Selective Laser Sintering (SLS) is a powder-based additive manufacturing technology that uses a laser to melt and fuse fine polymer particles of materials to create 3D objects. Commonly known as SLS, this 3D printing technology falls under the power bed fusion AM category. Powder bed fusion is one of the 7 types of Additive manufacturing technologies.

Selective laser sintering (SLS) 3D printing has become renowned for its low cost, comparably high production rate, ability to print complex geometries and increased choice of materials. Due to these characteristics, SLS 3D printing is ideal for rapid prototyping, functional prototype assemblies, pre-production parts and test rigs.
SLS also has the advantage of printing parts with thin walls and complex internal structures, making it a popular choice for various applications, including aerospace, automotive, and medical devices.
What are the characteristics of SLS?
Tolerances & Accuracy | Typical tolerance – ± 0.3% of the dimension (Lower limit of ± 0.3 mm (± 0.012 in)) |
Layer thickness | 0.050 – 0.120 mm It depends on the SLS printer’s quality |
Minimum feature size | 0.5 mm or 0.8 mm The minimum feature size will depend on the type of features |
Build volume | The average build volume is around 300mm x 300mm x 300mm. Larger industrial machines offer a 700mm x 380mm x 580mm build volume. |
How does Selective Laser Sintering work?
SLS Printer Overview
The schematic shows a typical SLS printer containing a build chamber, powder delivery chambers, spreading roller or arm, articulated laser beam, and heating systems.
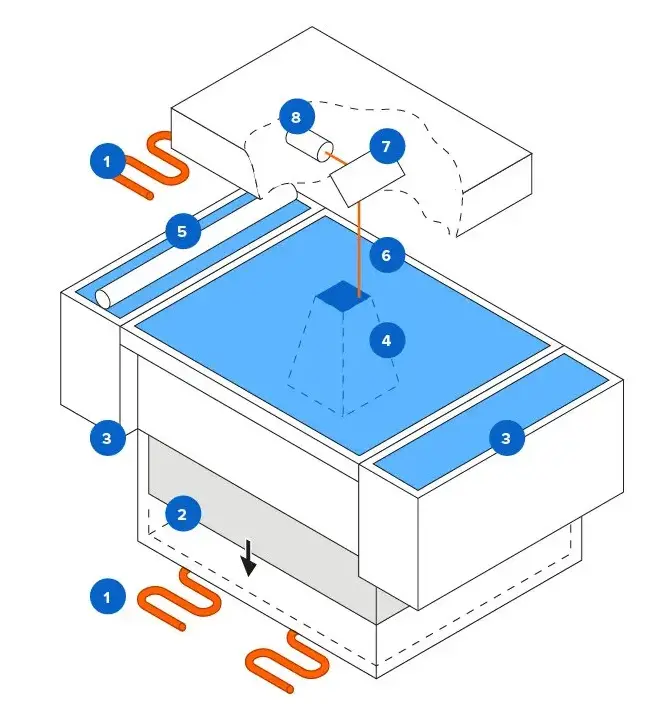
ID No. | Description | ID No. | Description |
---|---|---|---|
1 | Heaters | 5 | SLS powder recoater |
2 | SLS build chamber | 6 | Laser beam |
3 | Powder delivery chambers | 7 | X-Y scanning mirror |
4 | SLS printed part | 8 | Laser |
Selective laser sintering process steps
Selective laser sintering (SLS) is a 3D printing process that uses a laser to fuse fine material particles into solid structures selectively. The basic steps of the process are as follows:
- Powder bed preparation
- A fine, loose powder material, such as Nylon, is loaded into the powder delivery chambers and onto the build platform.
- The machine heats the powder inside the powder delivery chambers and builds a platform below the polymer melting temperature.
- The coating arm then spreads a thin layer of powder material evenly across the build platform.
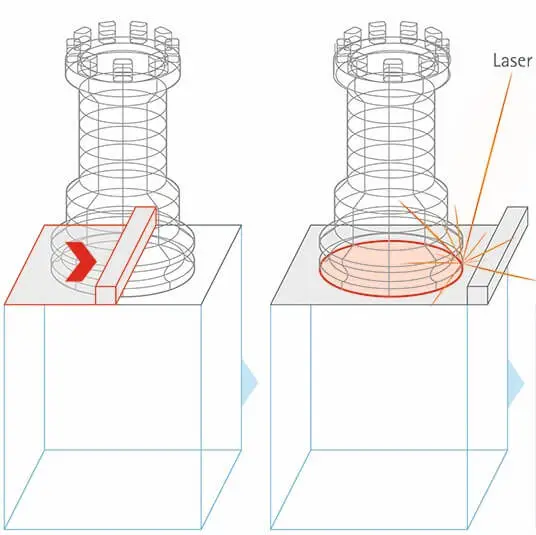
- Laser scanning and fusing
- A laser beam is directed onto the surface of the powder bed, following the contours of the 3D model to fuse the particles selectively.
- The laser selectively sinters the material, causing it to stick together and form a solid structure. The fusing contour path comes from the digital 2D cross-sectional data from the STL file.
- Layer buildup
- After the first layer is complete, the machine lowers the build platform and spreads another layer of powder.
- The laser then scans this new layer, fusing the particles to form another solid layer. The printing process is repeated layer by layer until the entire object is built.
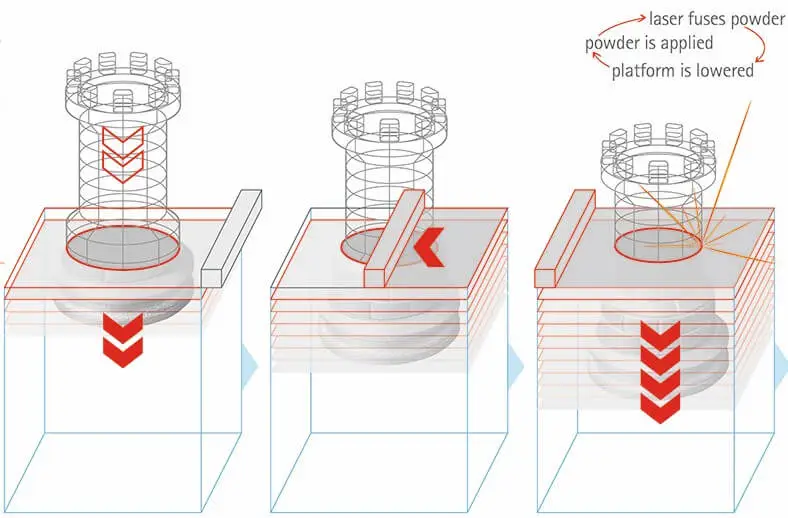
- Powder removal
- After the print, the platform is cooled, and the excess powder is removed, leaving behind the finished object.
- Post-processing
- Depending on the material used, the object may require additional post-processing steps, such as sanding or coating, to achieve the desired surface finish and durability.
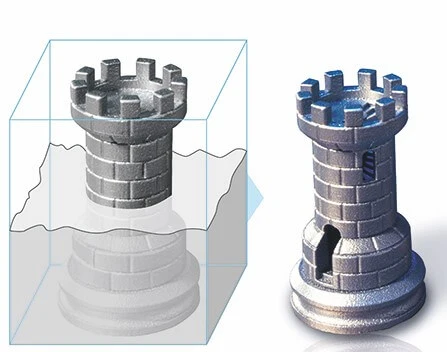
Advantages and disadvantages of selective laser sintering
What are the advantages and disadvantages of selective laser sintering? Like any other manufacturing process, SLS has both benefits and limitations
Advantages of Selective Laser Sintering
Selective Laser Sintering (SLS) is a 3D printing technology with several advantages.
- No need for support structures – Unlike material extrusion printing technologies, SLS does not require support structures. The powder surrounding the built section supports the printed section. Hence, SLS is more cost-effective and efficient, producing parts with a cleaner finish without support.
- Powder recycling – Remaining unsintered SLS powder is collected and reused, reducing waste.
- Complex geometries – SLS can print complex and intricate parts with fine details, making it ideal for producing functional prototypes and end-use parts with complex geometries.
- Wide range of materials – SLS can use various materials, including Nylon, metal, and ceramics, providing designers and manufacturers with multiple application options.
- Good mechanical properties – SLS can produce strong and durable parts, making them suitable for high-stress and high-load applications in aerospace, automotive, and medical devices. In addition, unlike FDM, SLS provide isotropic mechanical properties.
- Large build envelope – Compared to SLA and FDM, SLS machines have larger build volumes, allowing for the production of more significant parts in a single print run.
- Fast production times – Since powders require little exposure to powerful lasers to fuse, SLS can print parts quicker than its counterparts. As a result, SLS production times are typically faster than other 3D printing technologies, making it ideal for short production runs and rapid prototyping.
- Dying and colouring – SLS parts have a porous surface finish, making them suitable for dyeing and colouring.
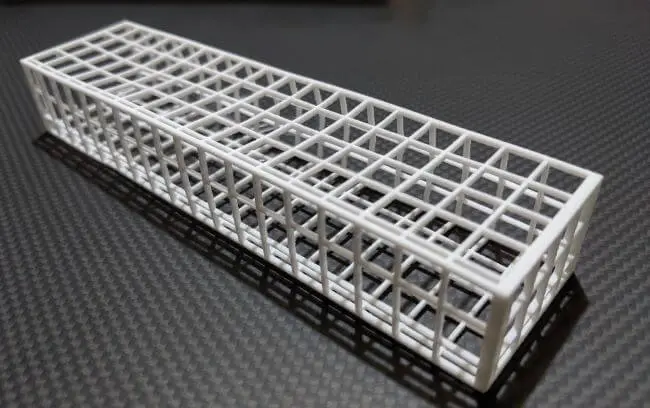
Overall, SLS is a versatile and highly efficient 3D printing technology that allows designers and manufacturers to produce complex, high-quality parts with various materials. Its advantages make it popular for applications from functional prototypes to end-use parts.
Disadvantages of SLS
Despite its many advantages, Selective Laser Sintering (SLS) also has some disadvantages, including:
- High equipment cost – SLS machines and materials can be expensive, making them a less accessible option for small businesses and individuals. This also drives the printing cost by service providers.
- Limited material options – SLS can only print Nylon based material.
- Low resolution – SLS resolution is lower than other manufacturing processes, making it unsuitable for producing highly detailed parts with fine features.
- Part warping – SLS parts can sometimes warp or deform due to the high heat generated during the printing process, which can affect the accuracy and dimensional stability of the finished part.
- Powder residue – SLS leaves a fine layer of unused powder on the part’s surface, which can be challenging to remove and affect the final product’s quality.
- Post-processing requirements – SLS parts may require additional post-processing steps, such as sanding or coating, to achieve the desired surface finish and durability.
While SLS offers many advantages, it is essential to consider these disadvantages and weigh them against your specific needs and requirements before choosing this technology for your 3D printing projects.
What materials are used for SLS
Selective Laser Sintering (SLS) is a 3D printing technology that can use a variety of materials, including:
Material | Characteristics |
---|---|
PA12 – Polyamide 12 (Nylon) | PA12 mechanical properties are comparable to injection moulded polyamide, with high dimensional stability, wear and chemical resistance. |
Polyether block amide (PEBA) | This thermoplastic polyamide elastomer (TPA) is a strong yet flexible rubber-like material. |
Alumide (Aluminium-filled polyamide) | This aluminium-filled polyamide is characterised by high stiffness and good post-processing abilities. Metallic appearance |
Carbon-fiber filled polyamide (PA-FR) | Excellent stiffness High weight-strength ratio Highly anisotropic |
Glass-filled polyamide (PA-GF) | High stiffness Anisotropic behaviour Increased wear and temperature resistance |
PA11 – Polyamide 11 (Nylon) | This environmentally friendly material is characterised by high-impact resistance and elongation at break. |
TPE Thermoplastic elastomers | Tear and abrasion resistance Flexibility Durability |
Polypropylene (PP) | Excellent plasticity High elongation Low moisture absorption High durability Excellent chemical resistance |
These materials offer a wide range of properties. As a result, they are suitable for various applications, but the choice of material will depend on the specific requirements and needs of the project. Therefore, it’s essential to consider the material’s strength, heat resistance, durability, cost, and availability when choosing a material for your SLS project.
No comments:
Post a Comment