One unsuspecting February morning in 1976, a 7.5 scale earthquake shook the Central American country of Guatemala. Originating from the Motagua Fault, the meeting point of the North American and Caribbean tectonic plates, the earthquake killed around 23,000 people and injured many more. The damage to buildings was also devastating, with tens of thousands of brightly painted adobe houses reduced to rubble in a matter of seconds.
Ironically, one of the few places in Guatemala that wasn’t leveled by the earthquake was the ancient Maya city of Tikal. Although the shock had uprooted plenty of trees, the city’s limestone buildings — including its iconic pyramids — didn’t show as much as a scratch. To locals, this was as relieving as it was puzzling.
How did the Maya, who lived hundreds of years ago and had limited access to technology, create architecture that was as strong and durable as anything modern engineering could produce? The answer, research has started to show, has to do with three ancient tricks, relating to the location, structure, and substance of their builds.
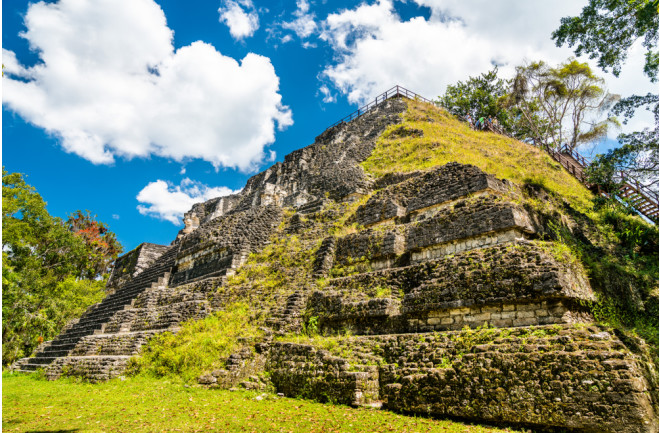
What Was Unique About Mayan Architecture?
Hidden in the jungles of northern Guatemala, about 30 miles away from the border with Belize, Tikal was originally occupied between around 300 and 900 B.C.E. That being said, the city's biggest buildings came centuries later, between about 600 and 900 C.E., when the Maya were at the height of their power. The city, whose name means “at the watering hole,” is thought to contain more than 4,000 buildings, the vast majority of which remain unexcavated.
The buildings, organized around squares and plazas, come in many different shapes and sizes, ranging from large to downright colossal. While the small, wooden homes of ordinary Maya citizens have long been lost to time, the palaces they raised for their kings — multi-storied and surrounded by towers and courtyards — are still standing.
What Were Mayan Pyramids Used For?
Also standing are the pyramids, similar to their Egyptian counterparts in basic design but different in finish. Constructed at a slightly steeper incline, their exterior is as richly decorated as the rooms inside. Mayan pyramids were mainly used for religious purposes, and tombs for dead leaders. Tikal even had several courts for playing tlachtli or pok-ta-pok, a traditional Maya ball game where players used only their elbows, knees, and hips.
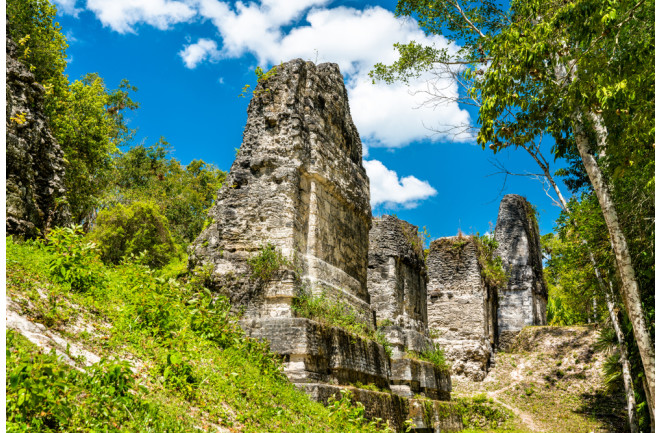
Why Was Maya Architecture So Long-Lasting?
With all that in mind, what allowed the Maya to make their structures so strong?
1. A Strong Location
The durability of Maya architecture could have several explanations, the first of which concerns location. Deeply familiar with the terrain, the Maya constructed their biggest settlements in places that were mostly safe from natural disaster, with the surrounding swampland insulating Tikal from 1976’s worst aftershocks.
But while swamps provide protection from earthquakes, they are also prone to flooding. The Maya addressed this problem with careful urban planning, placing their buildings on elevated ground so that they would remain dry during the rainy season.
2. A Sturdy Structure
A second explanation for the durability of Maya architecture has to do with the Maya’s knowledge of engineering. Pyramids are among the most stable and earthquake-resistant structures ever produced, rivaling Roman domes. This is because each layer is larger and heavier than the one above it, according to a 2020 analysis, preventing the structures from falling over or collapsing in on themselves.
3. A Recipe for Resilience
If location and engineering form the first two parts of the equation, material would be the third. Restricted to the natural resources that would have been available to them, the Maya made their buildings out of limestone, which they reinforced with a technique called lime pyrotechnology.
Mayan Architectural Techniques
By burning the limestone to temperatures of over 1650 degrees Fahrenheit, Maya builders created quicklime — a sturdy compound that hardens when exposed to CO2.
A paper published in 2018 states that the Maya discovered pyrotechnology as early as 1100 B.C.E. By the time Tikal entered its glory days, the city consisted of buildings so tough, they could withstand a millennia of exposure to the region’s tropical climate.
In addition to their pyrotechnology, the Maya peppered their lime plaster with ingredients from the environment. Studying the architecture of the Maya ruins of Copán, south of Tikal, and consulting indigenous people in the area, a team of mineralogists from the University of Granada in Spain found in that Maya builders infused their quicklime with the sap of two native tree species, chukum and jiote.
Recreating Mayan Plaster
Operating under the assumption that these biological additives served a practical purpose, as opposed to a ceremonial purpose, the mineralogists made their own, replica mix of Maya plaster, allowing them to put its structural integrity under a microscope.
According to the team's 2023 analysis, that assumption was confirmed. Once added, the tree sap was “absorbed on and occluded in the mesostructured calcite crystals making up the cement matrix of the plasters.” They concluded that “these organics profoundly affect" the structural traits of the substance, “rendering the plaster more resistant to physical and chemical weathering.”
Other Remarkable Uses of Ancient Architecture
It’s worth noting that the Maya weren’t the only civilization to enrich their plasters and mortars with things taken from their direct environment. Over the years, researchers have found ancient structures that contain traces of materials as diverse as milk, cheese, beer, and even urine. The mortar of China’s Great Wall and Forbidden City was made with starch and sticky rice, while the Roman architect Vitruvius, in his book De Architectura, recommends cooking oil as a means to make lime waterproof.
Trial and Error Engineering
Ancient architecture was a field of experimentation, and not all of these unusual ingredients were equally useful.
Sometimes materials were thrown in at random just to see what they would do. At other times, builders worked with intention, guided by experience and understanding. This seems to have been the case in India, where inlanders used herbs to help their mortar withstand moisture, and where the coastal dwellers routinely added unrefined sugar to protect buildings against the corrosive effects of sea salt. Maya use of chukum and jiote sap seems to have been similarly intentional.
Why Is Ancient Architecture Important?
Ultimately, studying the chemical composition of ancient architecture can help improve its modern counterpart. Although Maya, Indian, and Roman materials could never be applied to the construction of skyscrapers — a flat made from Roman concrete, University of Victoria archeologist John Oleson once said in an interview, “would collapse when you got to the third story” — their now-unorthodox techniques can inspire engineers to make important breakthroughs.
The stronger a building, the longer it will last. And in architecture, posterity is always an objective.