Vat Photopolymerization is AM technology that produces 3D objects by curing photopolymer liquid resin using light waves.
What is Vat Photopolymerization?
Vat Photopolymerization is a type of additive manufacturing technology that produces 3D objects by selectively curing photopolymer liquid resin using light-activated polymerization.
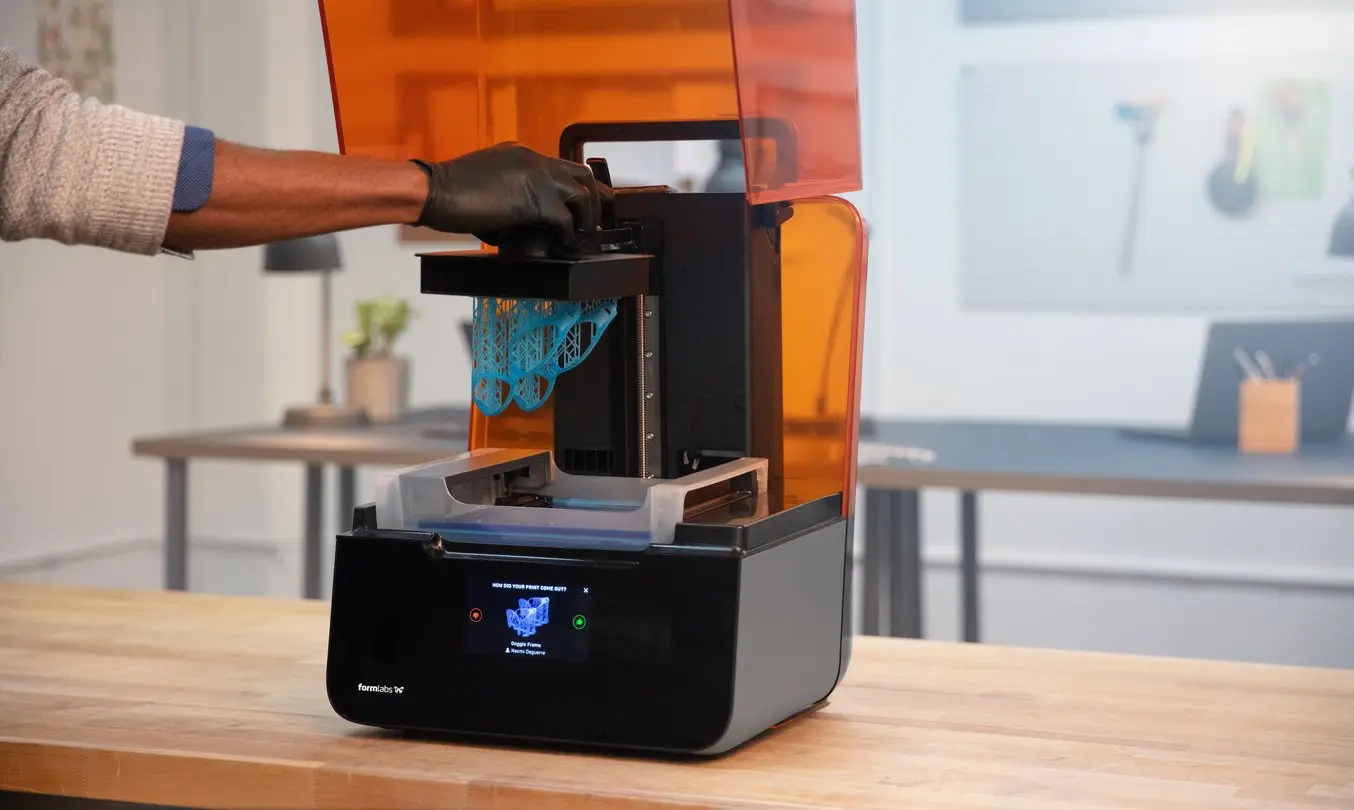
A photopolymer, also known as light-activated resin, is a polymer that changes its properties when exposed to light, often in the ultraviolet or visible region of the electromagnetic spectrum, causing its molecules chain to link. Stereolithography (SLA), the first patented and marketed AM process, is a vat photopolymerization technology.
Dr Hideo Kodama, a Japanese researcher, created the contemporary layered stereolithography technique in the early 1970s, employing ultraviolet radiation to cure photosensitive polymers. Chuck W. Hull invented the term stereolithography after patenting the technique in 1986 and establishing a company called 3D Systems to market it. Hull characterised the approach as printing small layers of an ultraviolet-curable substance in a series to create 3D things.
How does VAT photopolymerization work?
Special resins known as photopolymers are used as the printing medium in all forms of vat photopolymerization printers. When exposed to specific wavelengths of light, the molecules of liquid photopolymers quickly bond together and cure into a solid form, a process known as photopolymerization. Most 3D printers that use vat photopolymerization keep liquid photopolymer in a container or vat, with the build platform partially submerged at the liquid’s surface. The printer directs a light source to selectively cure the liquid photopolymer into a solid layer using information from a CAD file. The build platform is then re-submerged in the leftover resin, and the process is repeated for the subsequent layers until the design is entirely produced.
Vat photopolymerization types
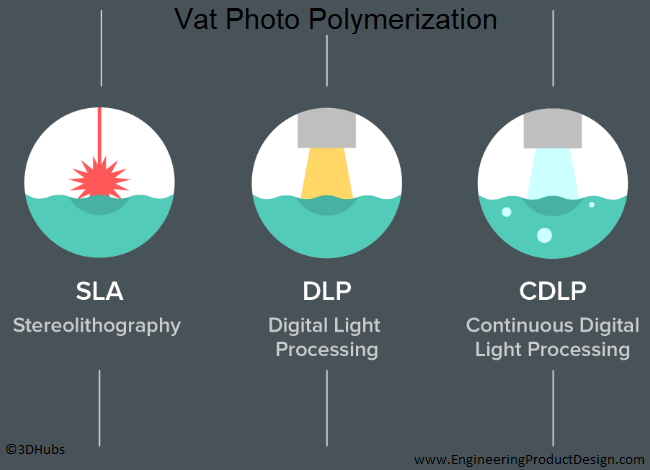
Stereolithography (SLA)
Stereolithography (SLA) uses a build platform immersed in a transparent tank of liquid photopolymer resin. After submerging the construction platform, a single point laser within the machine maps a cross-sectional area of a design through the tank’s bottom, hardening the material. The platform rises and allows a new layer of resin to flow beneath the object once the layer has been mapped and hardened by the laser. This technique is done layer by layer until a solid portion is formed. After that, the parts are routinely post-cured using UV radiation to enhance their mechanical qualities.
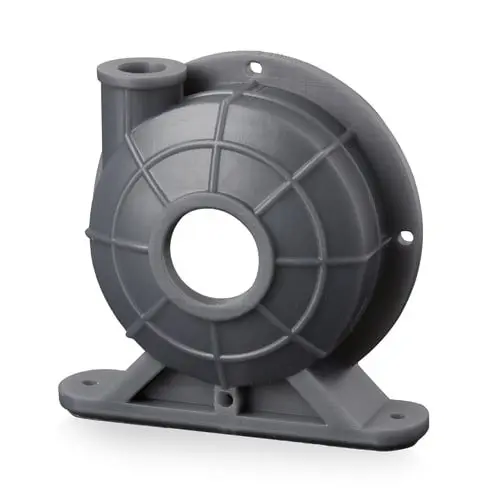
- Manufacturers – Formlabs, 3D Systems, DWS
- Material available – Standard, tough, flexible, transparent, & castable resins
Direct Light Processing
When compared to SLA, Direct Light Processing (DLP) uses a very similar process of creating components. The primary distinction is that DLP employs a digital light projector screen to display a single picture of each layer all at once. Since the projector is a digital screen, the picture on each layer is made up of square pixels, resulting in a layer made up of little rectangular bricks known as voxels. For some items, DLP can achieve quicker print speeds than SLA since each full layer is exposed all at once, rather than tracing the cross-sectional area with a laser.
- Manufacturer – B9 Creator, MoonRay
- Material – Standard & castable resins
Continuous Direct Light Processing (CDLP)
Continuous Direct Light Processing (CDLP) manufactures parts in the same way as DLP does. It does, however, rely on the build plate’s constant motion in the Z direction. This results in quicker build times since the printer does not have to stop and extract the component from the build plate after each layer is generated. This process is also known as Continuous Liquid Interface Production or CLIP.
- Manufacturer – Carbon3D, EnvisionTEC
- Material – Standard, tough, flexible, transparent, & castable resins
VAT photopolymerization applications
Vat polymerization methods are good for generating finely detailed pieces with a smooth surface finish. As a result, they are perfect for jewellery, low-run injection moulding prototypes, and a variety of dental and medical applications. The brittleness of the generated pieces is one of the key constraints of vat polymerization.
Advantages and disadvantages of VAT photopolymerization
Advantages of VAT photopolymerization
- A high degree of detail, precision, and overall quality
- The process is rather rapid
Disadvantages of VAT photopolymerization
- Costly in comparison
- Typically, they must be post-cured for an extended period to get significant strength from them
- Lack of photo-resin material choices
- Inadequate strength and durability
- After printing, resins can still be affected by UV Light
- Resins can warp and bend over time
No comments:
Post a Comment