What are Alloys? (Definition, Examples, and Metallurgy)
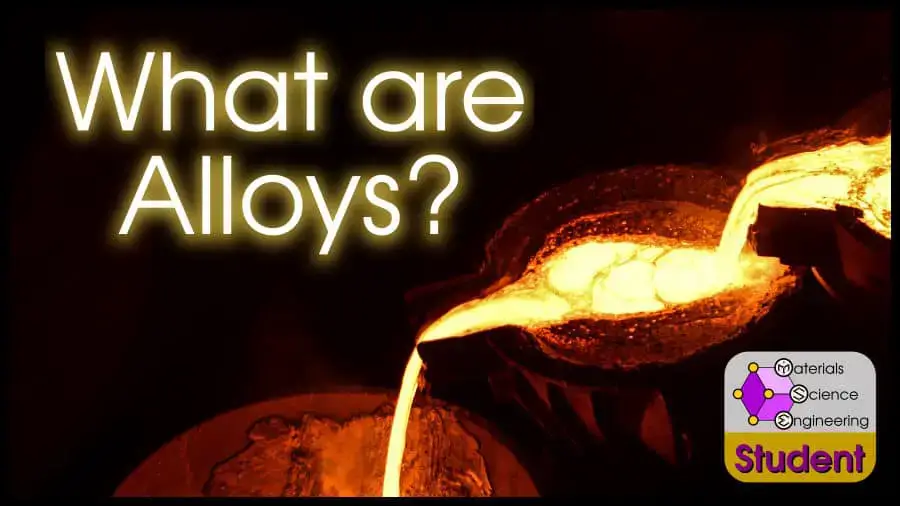
As someone who studies metallurgy for a living, I am often annoyed by the misinformation that is spread about alloys. I can (mostly) forgive movies like Pacific Rim when they suggest that pure metals are somehow stronger than alloys, but I’ve even seen misinformation spread about alloys on “informative” websites. It’s time to set the record straight.
Alloys are metals made of more than one element. That’s it. As long as the final product behaves like a metal, but it’s not elementally pure, it’s an alloy. There are no special rules about solid solution, number of phases, or the ratio of metallic and non-metallic elements. You can also think of alloys as intentionally designed metals.
Alloys, like all metals, are reflective, strong, good conductors, and (usually) ductile. These properties come from metallic bonding.
Outline
Why are Alloys Useful?
By alloying–adding new elements to a pure metal–you can achieve new properties. For example, suppose you mixed lead and tin. Doing this will result in a lower melting point than either pure metal!
Just as alloying decreases the melting point, it increases the material’s strength. Brass and bronze are much stronger than pure copper. Steel (iron alloyed with carbon) is much stronger than pure iron.
Notice that a copper and nickel alloy has higher strength than a simple composite of pure nickel and pure copper.
There are very few situations where a pure metal performs better than an alloy. Usually, lower melting point is good because it requires less energy to process the final product. Higher strength is usually good, because strength is one of a material’s most important properties.
How are Alloys Designed?
Alloys are made by mixing a metal with other elements (usually more metals). This “mixing” can be done by melting the elements together (casting, induction melting, or vacuum arc melting).
A more expensive way of making alloys is called powder metallurgy, which squishes metal particles together and fuses them in a process called “sintering.” Powder metallurgy has many advantages over regular melting because you can combine elements with dissimilar melting points and make sure the mixture is homogeneous. However, it’s not easy to make metal powder!
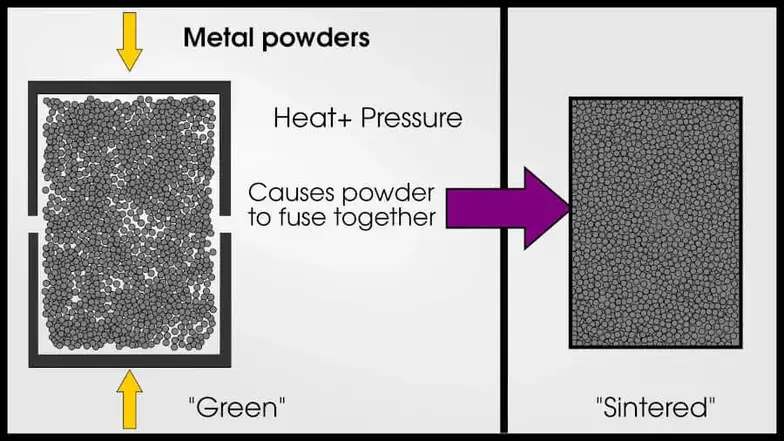
Alloys are typically designed to be in solid solution. It’s possible to have an alloy that is not in solid-solution, but these cases are rare. Generally, if two metals are not in solid solution,they will not have “metallic” properties (and won’t be called “alloys”). Alloys can also have precipitates which are not in solid-solution.
Solid solution means that one phase is dominant. Atoms of the other element are dissolved in the dominant phase, like sugar in water. (A popsicle is a good analogy for alloys). When you add sugar to water, you get sugary water. Add more sugar, and you still have water–it’s just sweeter.
But what happens if you add too much sugar? The amount of sugar that can fit into water at 90°C is a lot more than can fit at 10°C. In this case, the excess sugar will precipitate and form sugar crystals–alloy precipitation is exactly the same!
Effects of Solid Solution
Why is alloying two metals so different from combining them in a composite? After all, isn’t it the same amount of atoms?
The answer has to do with bonding. In an alloy the atoms are all mixed together. Every atom from one element interacts with several atoms of the other element. This is a very different situation from when atoms of an element primarily interact with themselves!
If you’re still confused about the difference between an alloy and a metal-metal composite, check out this article.
But why does solid solution mixing actually occur? And why do the atoms arrange randomly, rather than in a specific order?
Advanced explanation of why solid solution mixing occurs
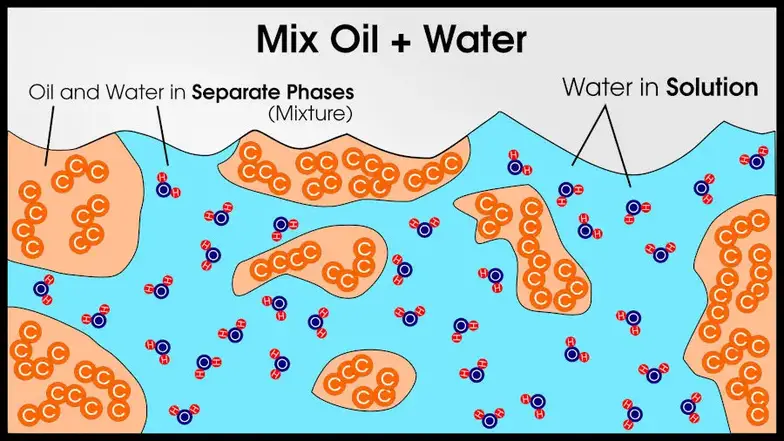
This is why A and B atoms can enter solid solution even if A-A and B-B bonds are stronger than A-B bonds. For most alloys, in fact, A-A bonds and B-B bonds will be stronger than A-B bonds.
That is why the melting point decreases when you alloy metals. Melting an alloy means adding kinetic energy until the atoms break their bonds. Weaker bonds mean a lower melting point.
But why are alloys stronger than the pure elements?
It’s very difficult to explain this unless you know other basic materials science concepts. For those of you who like a challenge, a brief explanation is included in the collapsable text.
Why alloys are stronger than pure metals
Types of alloys
There are several broad classes of alloys.
Regular alloys
Substitutional or interstitial alloys. Most of the composition is made of a single element, with small additions of other elements. If there are two elements, it’s a “binary alloy,” three elements is “ternary,” four elements is “quaternary,” and five elements is “quinary.” In practice, alloys with more than three different elements will be called “multi-component” alloys.
Steels
Steels are not fundamentally different from other alloys, except that they are perhaps the most advanced material metallurgy can offer. Highly engineered steels may have a dozen elements in small amounts (in addition to Fe and C).
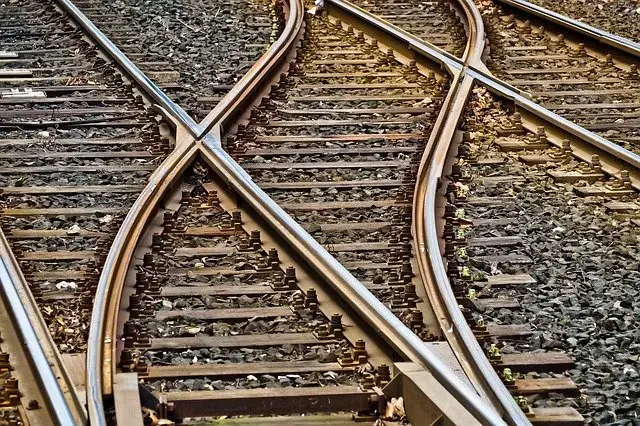
Superalloys
Superalloys are another pinnacle of metallurgy. Superalloys are like micro-scale composites. They have a matrix (solid solution) phase, and a precipitate (intermetallic) phase. Like steels, modern superalloys may have 10-20 alloying elements.
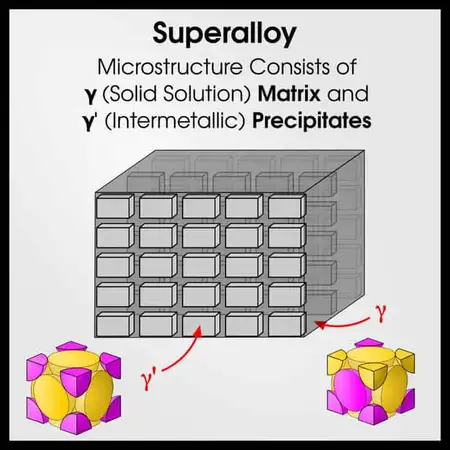
HEAs
High-Entropy Alloys (HEAs) take solid solution strengthening to the extreme. Remember how I said that most alloys are primarily composed of a single element? That’s because intermetallics may form if two elements occur in similar amounts. Instead, HEAs combine 5 or 6 metal elements in equal ratios. Because of the entropy of mixing, the alloy stays as a single phase. HEAs are a new type of alloy and are not commercially widespread.
BMGs
Bulk Metallic Glasses (BMGs) are metals arranged in an amorphous structure. That means there is no orderly crystal structure. These are slightly more developed than HEAs, but they are still rare.
Intermetallics
Intermetallics are not considered alloys by every materials scientist (see my argument here). I prefer to call them “intermetallic compounds” instead of “intermetallic alloys,” because the atoms are arranged in an ordered structure like ceramics, rather than in solid solution. In general, intermetallics have terrible properties and are completely useless. However, there are two notable exceptions. The strengthening phase of superalloys is an intermetallic, and NiTi is an intermetallic shape memory alloy.
Can a Pure Metal be an Alloy?
This is a purely semantic argument. Most materials scientists disagree with me, so reading this will likely confuse you. Still, I want to get it off of my chest so I decided to put it here in this collapsible text.
Click here to expand
To me, the word “alloy” suggests a compositionally engineered metal. Add carbon to iron, and get the stronger alloy, steel. Add chromium to steel, and get the corrosion-resistant stainless steel.
Alloying a metal means adjusting its composition to achieve certain properties. But can “dealloying” achieve the same thing? I believe it can.
Imagine that I wanted a material with the highest melting point possible. We’ve already discussed that having extra atoms in your metal decreases the melting point. So in this case, I would want to take pure tungsten and purify it further.
“Pure tungsten” may be 99.99% tungsten, and 0.01% other things that the manufacturer couldn’t remove. So what if I intentionally design a process to make my tungsten 99.99999% pure, to achieve the highest melting point possible?
I no longer have a default pure element, I have an intentionally dealloyed material. Does this mean it’s an “alloy” again?
I think so, but so far no one else agrees with me!
Alloy Examples
Alloys can be defined by their patent, historical use, or manufacturing specifications.
These specifications are often developed because certain impurities need to be removed. For example, many steel alloys have 0.03-0.05% phosphorus. This isn’t because adding phosphorus improves the steel–it’s because that’s the maximum acceptable level of phosphorus and it’s too expensive to remove more than that.
Here are a few examples of common or unique alloys.
Sterling silver
Ti-6Al-4V
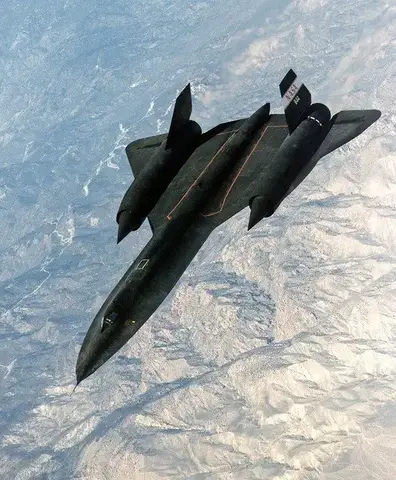
Ni-based superalloys
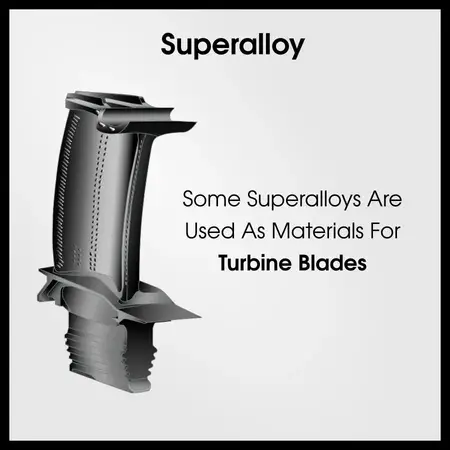
Stainless steel
Solder
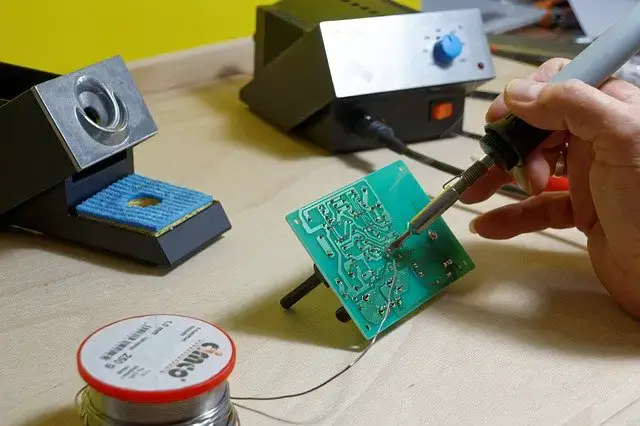
Bronze
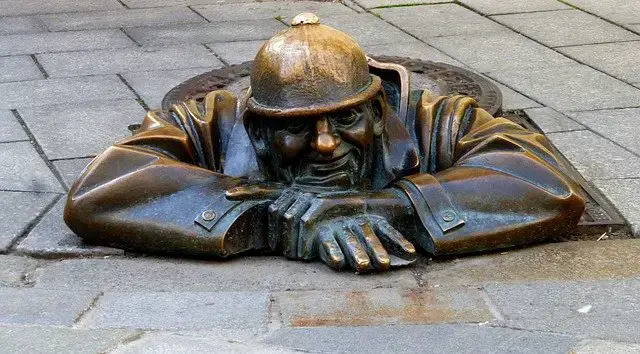
Brass
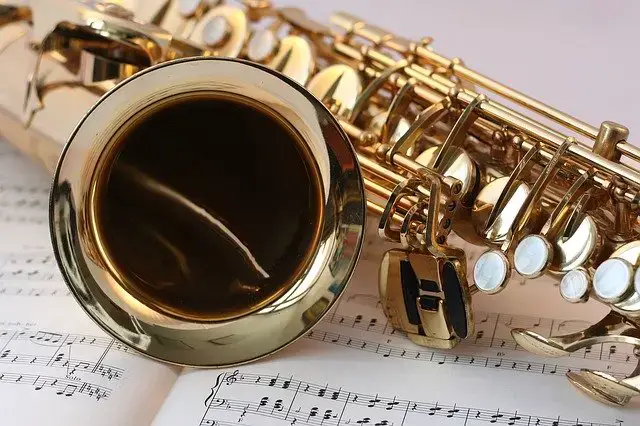
Bulk Metallic Glass
NiTi
Final Thoughts
Alloys are some of the most important engineering materials. Metals are useful for their conductivity, reflectivity, formability, and warning signs that they will break. They are relatively cheap to mine and manufacture.
Almost all real-world metals are alloys, instead of pure metals. Among other advantages, alloys are usually stronger and have a lower melting point than pure metals. The most important downside of alloys is that they have lower conductivity than pure metals–which is why the only pure metal you encounter in daily life is copper in electrical wires.
No comments:
Post a Comment