The first additive manufacturing system appeared in the 1980s — from there, additive manufacturing has taken off, branching out into several different types of technologies for turning CAD files into 3D physical objects.
Heading towards the end of the Cold War in the United States in the 1980s, military funding exploring science and industrial technologies increased. This led to the exploration of a diverse range of ideas and concepts with innovative potential — one of these was additive manufacturing. In the early 1980s, Dr. Hideo Kodama, an inventor, took the knowledge from 3D scanning and the layering pattern from 3D topographical maps, to create the prototyping machine. In 1984, Charles Hull developed the material Stereolithography Apparatus known as SLA. He went on to establish the first 3D printing company in 1986, that then produced the first 3D printing machine in the year 1987 — printing layer by layer using Stereolithography Apparatus (SLA). Thus, commercialized availability of additive manufacturing and 3D printing for manufacturers was born.
Following the release of this first 3D printer, inventors and creators began researching new methods and techniques for additive manufacturing. In 1991, three new, different additive manufacturing technologies were commercialized. Scott Crump invented a technology called fused deposition modeling (FDM), and founded his own company called Stratasys. A company called Cubital released a technology known as solid ground curing (SGC). An additive manufacturing technology called laminated object manufacturing (LOM) was introduced by a company called Helisys.
In the 2000s, more companies and enthusiasts took a keen interest in the capabilities and fundamental process benefits offered by 3D printing. Thus, the race to build the best machine and become a leader in the industry had begun. A new company called RepRap emerged in 2005 by professor Adam Bowyer from the University of Bath. The company specialized in making self-replicating machines. This open-source project led to the eventual proliferation of desktop fused deposition modeling (FDM) 3D printers. This turn in the industry influenced a company called MakerBot to produce DIY kits in 2009, for hobbyists interested in the idea of trying 3D printing to create models and build functional working parts for DIY projects. After hobbyist interest generated significant hype, another 3D company formed: Prusa Research was founded in 2011 and developed the Prusa i3 design, based upon the company’s early work on the RepRap machine. With the Prusa i3 3D Printer now on the market, MakerBot sought to be a contender, making the Replicator 2, which was released in late 2012. This machine became the world’s most popular 3D printer at the time.
As MakerBot continued its success, the creators of FDM, Stratasys, merged with another company (Objet) in 2012, and then subsequently acquired MakerBot in 2013. During this time period, available additive manufacturing solutions were characterized by several issues: cheap printers were unreliable and lacked the mechanical properties for high-value applications, while industrial 3D printers were not affordable to the majority of relevant manufacturers.
Markforged entered the industry in 2013 with a revolutionary 3D printer design and the ability to use methods such as Fused Filament Fabrication (FFF) and Continuous Fiber Reinforcement (CFR), which allowed parts to be printed quickly and accurately with a variety of innovative material options. Markforged’s proprietary CFR technology added strength to parts and introduced composite parts strong enough to replace metal parts: quicker, and for much cheaper. Markforged introduced the Mark One at Solidworks World 2014 with an anodized aluminum enclosure and native cloud-based slicing and control.
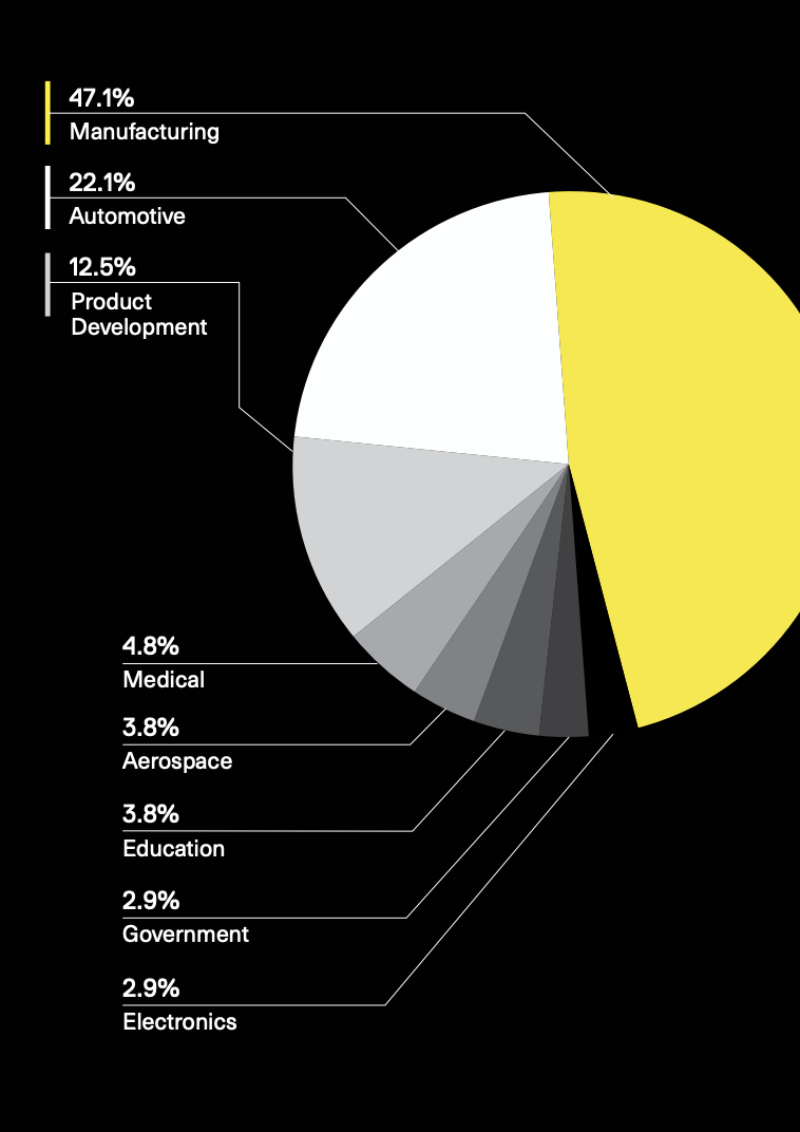
Adoption rates of additive manufacturing technologies across industries
Today's Additive Manufacturing Technologies
Today, additive manufacturing is a prominent growth driver in some of the largest global industries. According to recent data on industry adoption of 3D printing, 47% of manufacturers use additive technology: 22.1% of automotive manufacturers, 12.5% of product development manufacturers, and 4.8% of medical manufacturers. Aerospace, education, and the defense industries are also adopting additive manufacturing at ever increasing rates.
Even in the last decade, additive manufacturing solutions have come a long way. Compared to earlier additive manufacturing technologies, today’s 3D printing platforms are characterized by:
Improved power and reliability, with higher print speeds, maximum part sizes, and surface finishes.
Ease of use, as earlier additive manufacturing platforms required specialized knowledge and carried higher learning curves. Modern 3D printing software is intuitive to use and does not require additive manufacturing expertise.
Broader material capabilities, with the ability to print in traceable, aerospace-grade composite materials.
Introduction of metal fused filament fabrication (FFF) technology, which has made 3D printing metal parts faster, safer, and more cost effective than ever.
Cloud connectivity between each user and set of printers allows for distributed manufacturing operations. Users can initiate prints across 3D printers in different geographic locations, to ensure that the right part is available both where and when it is needed.
Industry 4.0 connectivity with 3D printing software integrations — part production can be initiated by requests in each factory’s core systems.
Scalability, from cloud-enabled interconnectivity combined with the expansion of different 3D printers that satisfy distinct manufacturing needs (such as metal, industrial 3D printers, and desktop 3D printers).
What Has Fueled the Growth of Additive Manufacturing?
Additive manufacturing is still relatively new. So, why have its technologies experienced this rate of growth since its inception? Simply put, innovation has occurred at a fast rate due to AM’s potential to be the most effective solution for many common manufacturing pain points.
One key benefit is that additive manufacturing produces drastically shorter lead times compared to conventional manufacturing processes. These shorter lead times mean that additive manufacturing can:
Support a just-in-time (JIT) manufacturing production model for companies to avoid risk and maintain leaner inventories.
Increase speed to market for products, as access to in-house additive manufacturing accelerates design cycles through enabling rapid prototyping, and produces the part in a fraction of the amount of time it would take to request and receive through traditional manufacturing processes.
Furthermore, in-house additive manufacturing grants companies full control of their supply chains. For manufacturers looking to reduce dependence on external suppliers and minimize risk in supply chain operations, use of an additive manufacturing platform allows them to control their full supply chain from end to end without worrying about common material shortages and logistical delays
Additive manufacturing also improves design freedom for engineers building parts. Oftentimes, the processes used to manufacture parts are dictated by the limitations of what the traditional manufacturing process supports. For example, when manufacturing a bracket through subtractive techniques, unnecessary constraints are imposed by having to start with sheet metal, while bending or stamping into shape. With additive manufacturing, designs can be made without these unnecessary steps and limitations.
Beyond the improvements it provides to manufacturing operations, adoption of additive manufacturing is representative of a cultural shift that puts innovation first. For job-seeking engineers, companies invested in an additive manufacturing strategy present opportunities to focus on innovation and solve interesting design problems, while automating the arduous tasks and eliminating unnecessary constraints that come with producing parts through subtractive manufacturing processes.
No comments:
Post a Comment