Introduction
This article contains detailed information regarding zirconia ceramic and ZTA.
You will learn more about topics such as:
- What are Zirconia Ceramic and ZTA
- Types of Zirconia Ceramics and ZTA
- How Zirconia Ceramics and ZTA are Made
- Uses for Zirconia Ceramic and ZTA
- And Much More ...

Chapter One – What are Zirconia Ceramics and ZTA?
Zirconia Ceramics, or zirconium dioxide ceramics, are exceptionally strong technical ceramic materials with excellent hardness, toughness, and corrosion resistance without the brittleness common to other ceramic materials. There are several grades of zirconia ceramics, with yttria and magnesia partially stabilized zirconia ceramics being the most common.
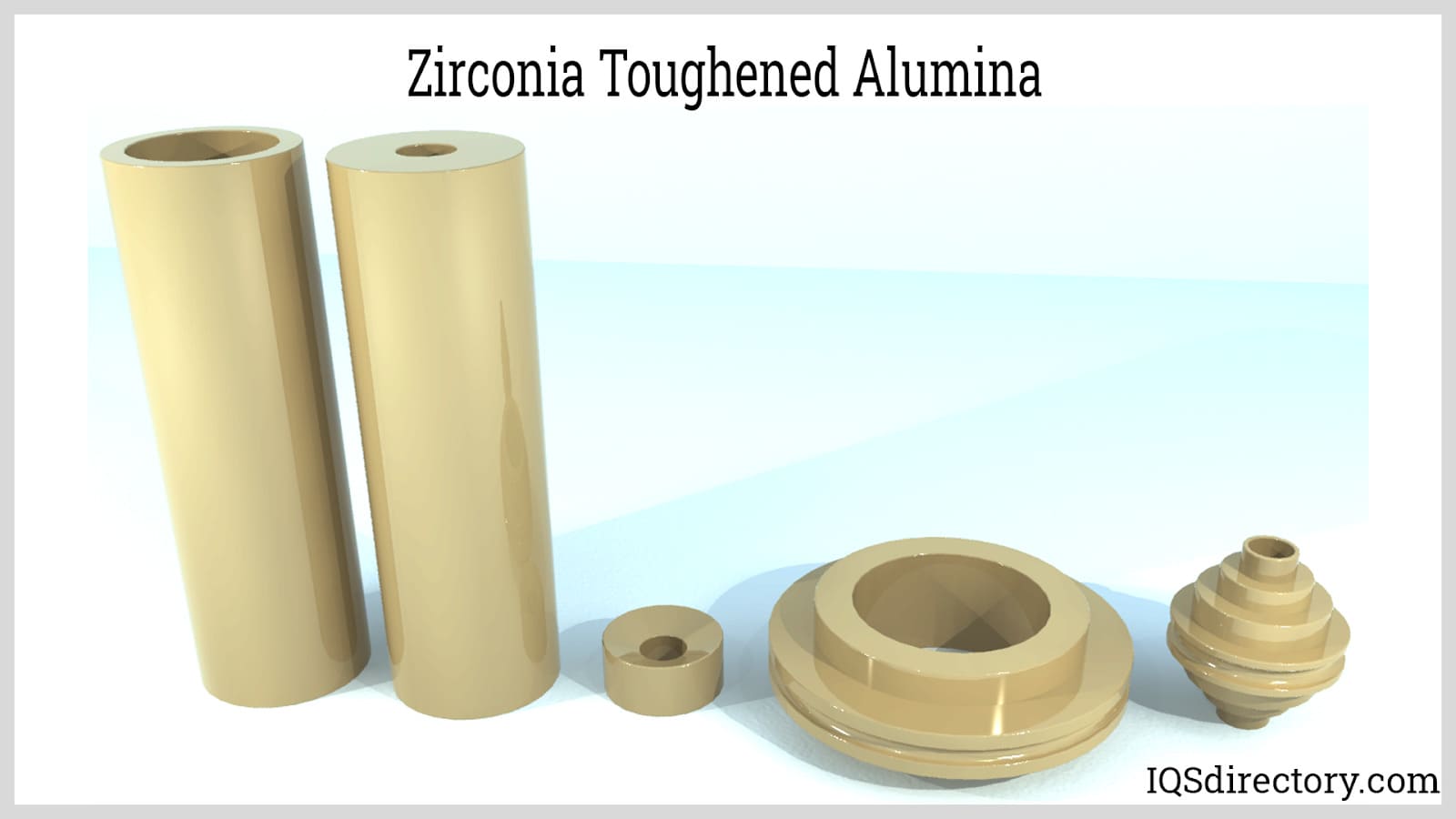
Zirconia toughened alumina (ZTA) ceramic is a composite material with alumina and zirconia as its major elements. The structure of ZTA includes zirconia grains placed in the alumina matrix. It has additional strength and toughness compared to alumina, with a lower cost than zirconia.
The combining of aluminum oxide and zirconium oxide significantly increases the strength, toughness, hardness, and wear resistance of the material. A process known as transformation toughening is at the center of the process that toughens the ceramic and increases its fracture toughness. When stress is applied, the particles of zirconia change their crystal structure, which causes a volume expansion to close any cracks.
Chapter Two – Types of Zirconia Ceramics and ZTA Ceramics
The many types of zirconia ceramics have developed from the desire of manufacturers to enhance the properties of the different phases of zirconia ceramics. The various phases require treatments to be appropriate for use in an assortment of environments. Zirconia toughened alumina is one of the many types of phases.
Oxides added to zirconia are designed to stabilize and toughen it. Typical stabilizing agents are yttria, ceria, magnesia, and alumina, each of which changes the properties and characteristics of the material.
Zirconia Ceramic Types
Ceria Stabilized Zirconia (CSZ)
CSZ has the toughness and strength to endure the challenges presented by moist and wet environments. It has high flexural and compressive strength, making it perfect material for producing sensors, instrumentation, probes, pumps, and fluid control systems.
When there are concerns about low temperature degradation, CSZ is used since it has less vulnerability to molecular water attack with the ability to withstand high temperature conditions.
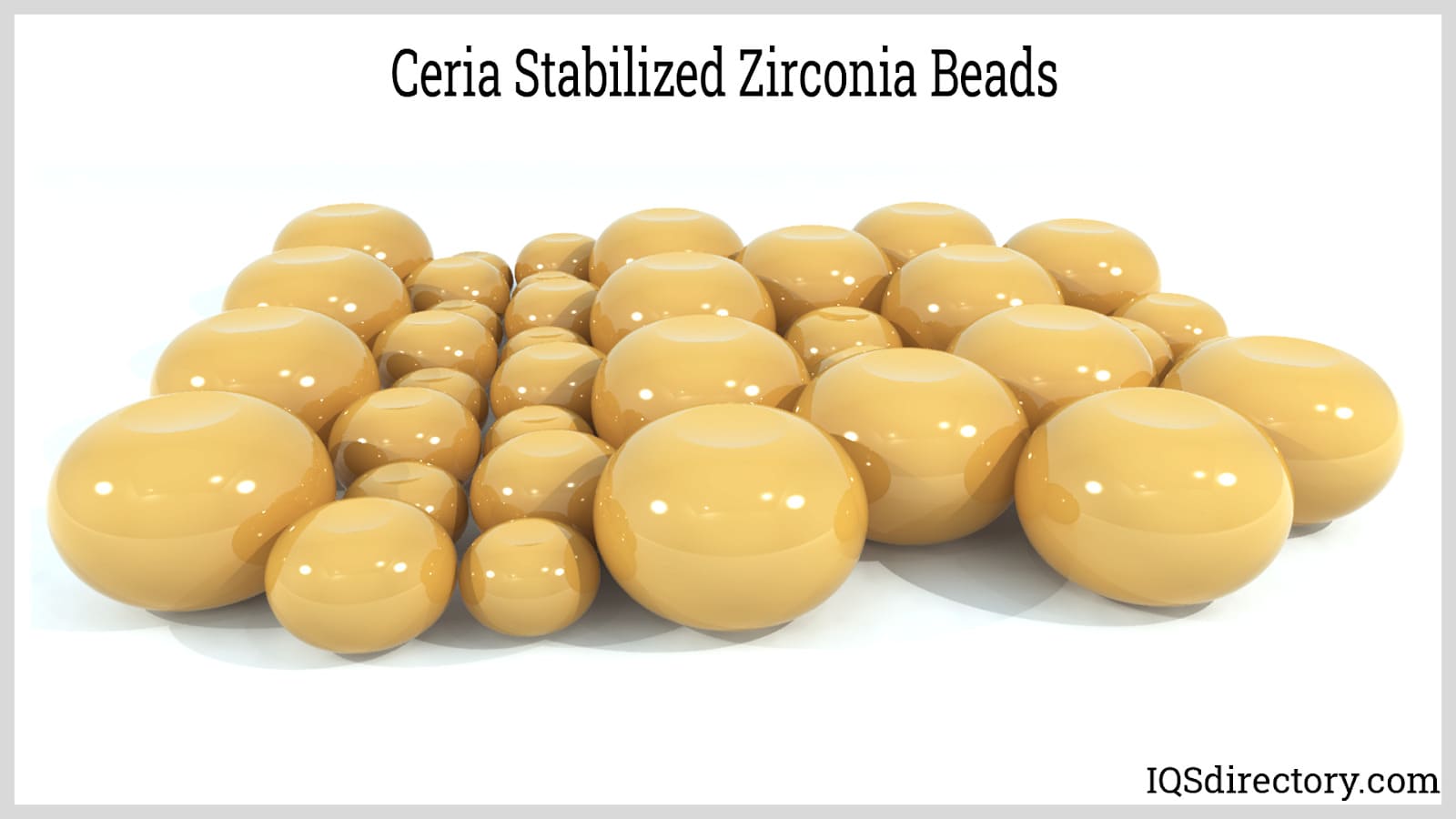
Various types of zirconia ceramics are continually being perfected as researchers combine various forms of stabilizing agents and metals to enhance the natural properties of zirconia.
Fully Stabilized Zirconia Ceramics (FSZ)
FSZ is stabilized with yttrium, a rare earth metal that is silvery white, soft, and ductile. It is used in high temperature applications that need thermal shock resistance, fracture toughness, and excellent corrosion resistance. A unique aspect of FSZ is its ability to allow only oxygen ions to pass through, which makes it viable for applications such as active membranes.
The transformation of zirconia from monoclinic to tetragonal to cubic increases its volume, which leads to cracks in the ceramic. By adding yttrium to the cubic polymorph, it is stabilized and capable of enduring a wide temperature range.
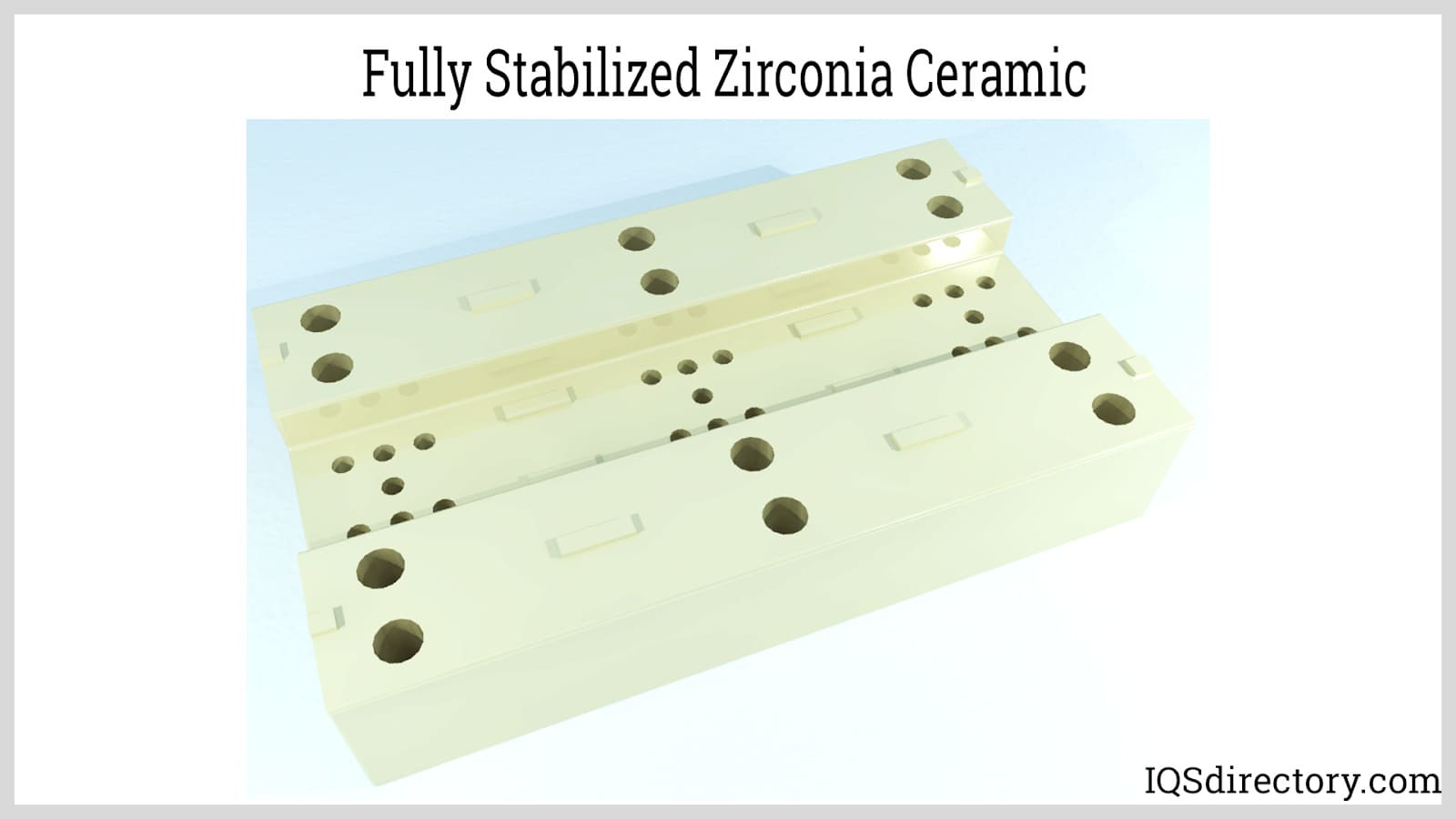
Partially Stabilized Zirconia (PSZ)
PSZ has a cream color with 10% magnesium oxide (MgO) as a stabilizer. They have high toughness, which it retains even at elevated temperatures. The microcrystalline grain structure of PSZ enhances its strength and makes it resistant to chemicals and heat.
Items made from PSZ will not corrode when exposed to high temperature fluid streams, even if the stream is a strong acid or alkali. In essence, PSZ is chemically inert with exceptional compressive and tensile strength.
A major benefit of PSZ is its ability to be machined into extremely intricate shapes, making it capable of performing functions where metals cannot operate. It is widely used for pump seals for caustic chemicals and friction stressed roller bearings.
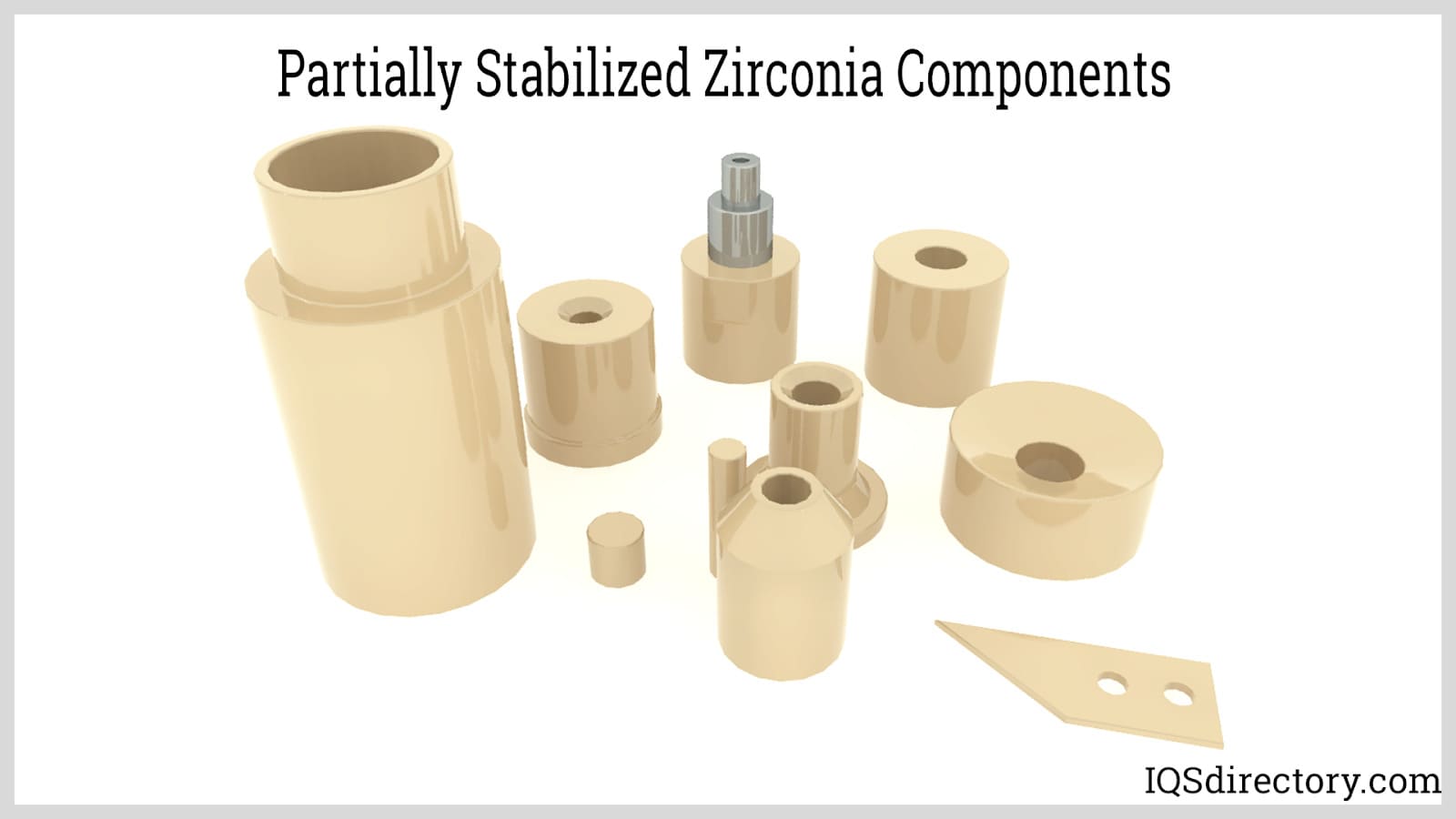
Tetragonal Zirconia Polycrystal (TZP)
TZP ceramics have outstanding fracture toughness and hardness at room temperature and corrosion resistance at extreme temperatures. They are the main material for medical procedures involving hip replacements and dental reconstructions. In the industrial area, TZP is used as a thermal barrier coating for fuel rod claddings.
Applications that demand the use of TZP require a strong, hard material with flawless microstructure. TZP has a thermal expansion coefficient that is close to iron and iron based alloys. It is referred to as ceramic steel because of its excellent fracture toughness.
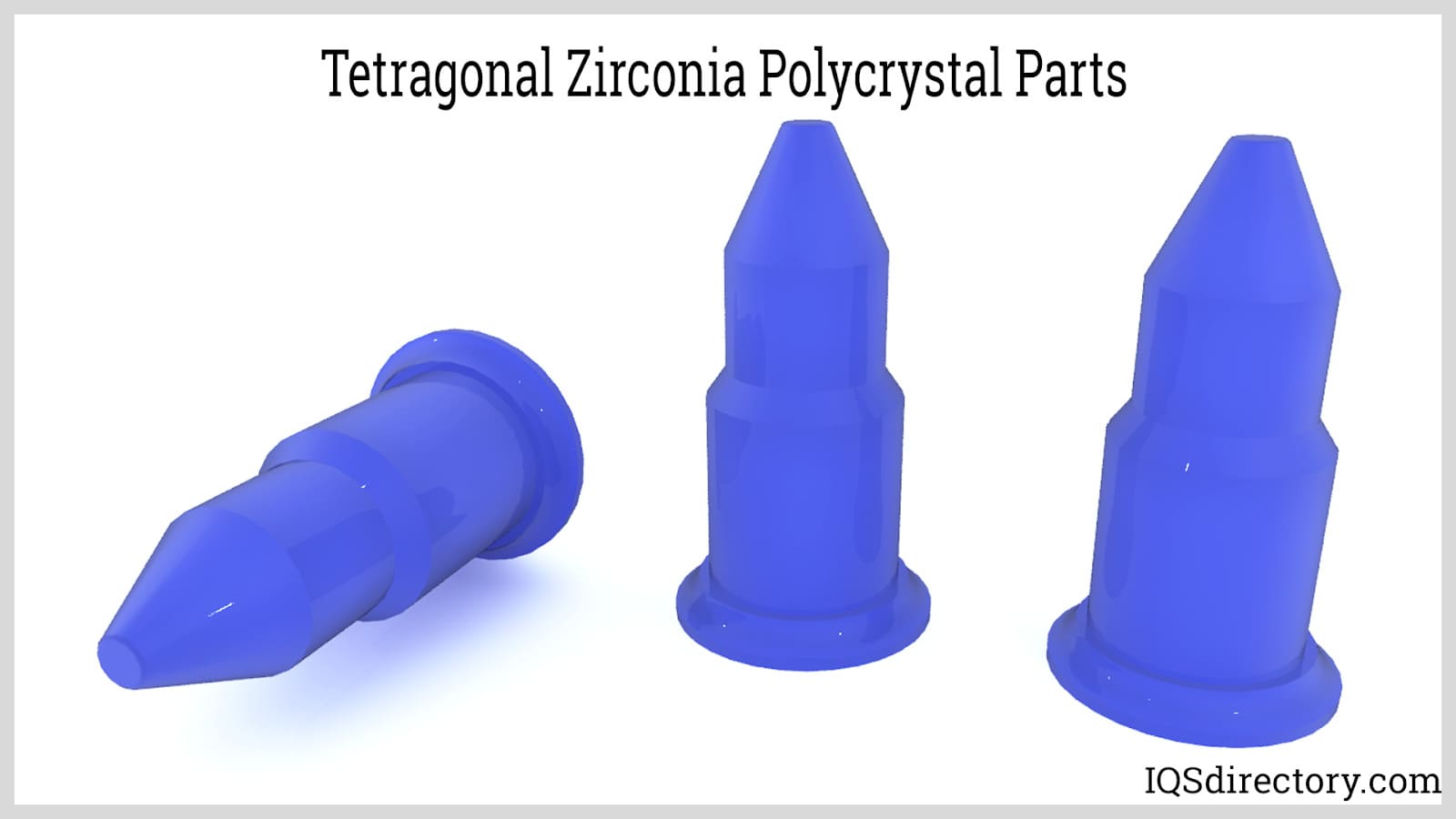
Transformed Toughened Zirconia Ceramics (TTZ)
TTZ is referred to as ceramic steel due to its strain response when stressed and is more like steel than brittle ceramic material. Transformation toughening of zirconia ceramic involves the use of martensitic phase transformation, which changes the stress state of a material by increasing tensile stress and acts against applied stress. When tension is applied, zirconia ceramics undergo a phase transformation that increases the ceramic’s volume and lowers the local stress to stop the growth of cracks. The process increases the toughness of ceramic materials.
A common use of TTZ is ceramic knives, which are twice as hard as regular steel knives and have ultrasharp blades for precision and delicate cutting.
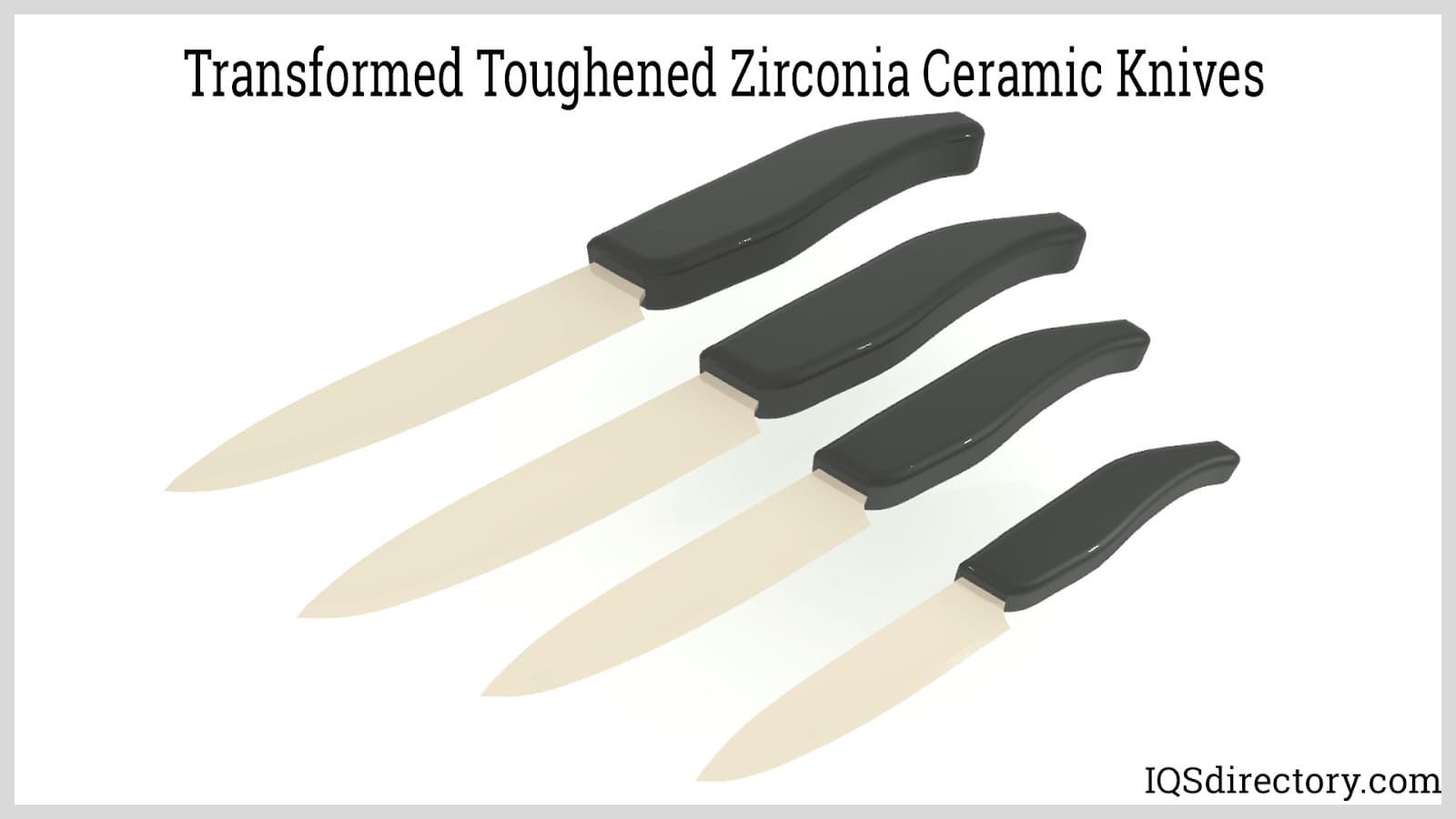
Zirconia Toughened Alumina (ZTA)
ZTA ceramics have chemical and thermal stability and exceptional strength. The production of ZTA includes stress induced transformation toughening where strain is applied to the zirconium that causes it to crack and move freely with the alumina particles. The result of the strain and cracking is a ceramic material with increased strength.
The use of ZTA is ever growing and includes valve seals, bushings, pump parts, medical implants, and cutting tools. The wide use of ZTA is due to its wide range of properties. Its strength and corrosion resistance makes it capable of enduring heavy loads without degrading.
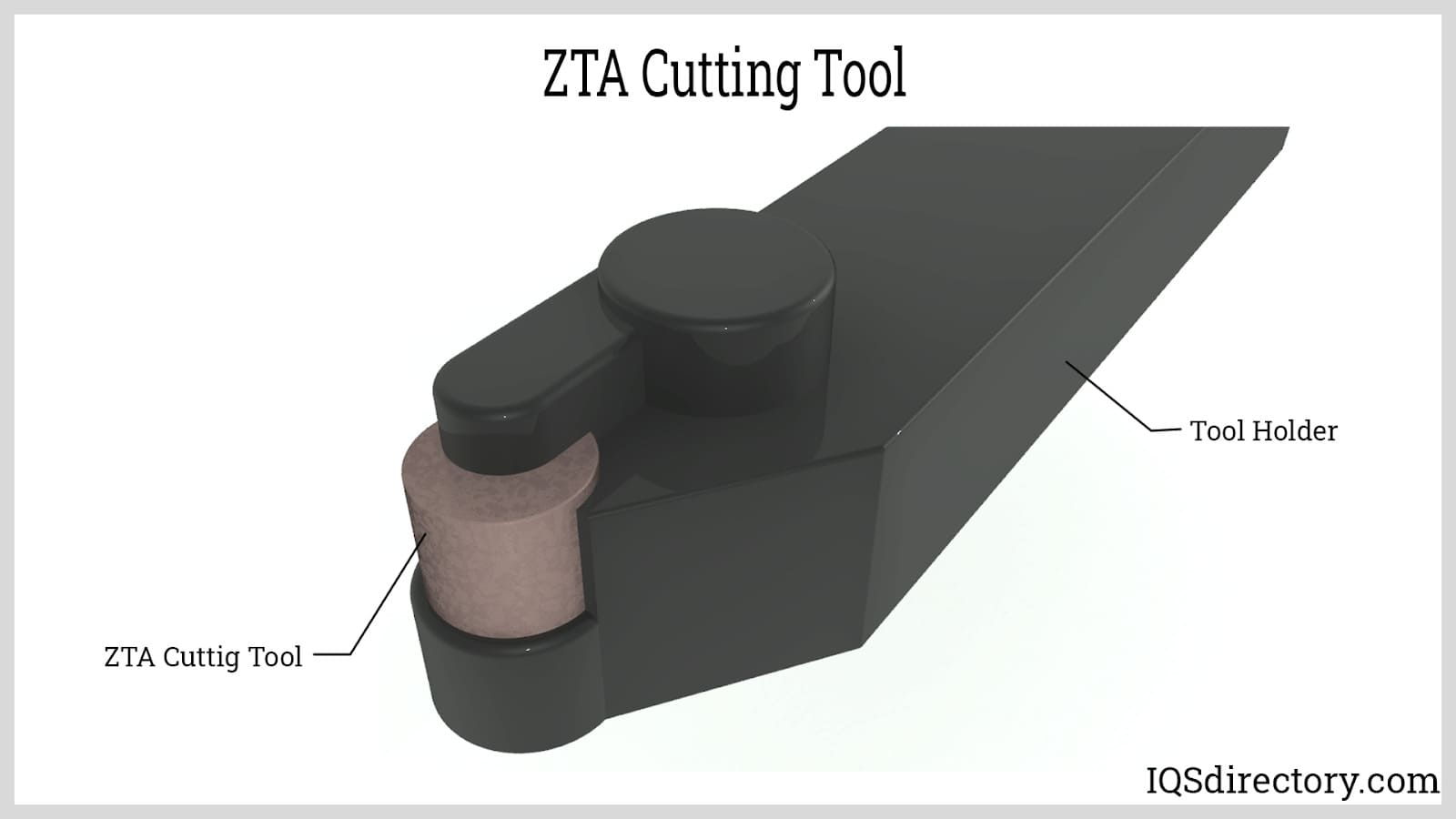
Chapter Three- Leading Manufacturers of Machinery Used to Produce Zirconia Ceramics and ZTA
Perfecting the process used to produce zirconia ceramics and ZTA is critical for best results. Luckily, there are many manufacturers of machines available in the United States and Canada that have essentially perfected this process. Below, we discuss leading manufacturers of this equipment.
Zirkonzahn – M1 Compact Milling Unit
The M1 Compact Milling Unit by Zirkonzahn is known for its versatility and precision in milling zirconia ceramics and other materials. It offers a compact design, making it suitable for small laboratory spaces. This machine provides high-speed milling capabilities and supports 5-axis simultaneous machining, allowing for complex designs and efficient production.
Amann Girrbach – Ceramill Motion 2
The Ceramill Motion 2 by Amann Girrbach is a versatile milling machine designed for producing zirconia ceramics and other dental restorations. The Ceramill Motion 2 features a fully automated 5-axis milling system, providing high precision and accuracy. This machine incorporates an intelligent tool management system and offers a wide range of compatible material blanks, making it suitable for various applications.
Ivoclar Vivadent – PrograMill One
The PrograMill One by Ivoclar Vivadent is a compact and user-friendly milling machine suitable for zirconia ceramics and other materials. It offers a self-contained design with an integrated PC and touch screen, simplifying the workflow. It uses high-performance components and provides efficient milling with high precision and surface quality.
Roland DG – DWX-52DCi Dental Milling Machine
The DWX-52DCi Dental Milling Machine by Roland DG is designed specifically for dental applications, including zirconia ceramics. It features a built-in automated disc changer, allowing for continuous milling without operator intervention. This machine offers simultaneous 5-axis machining, enabling complex dental restorations with excellent accuracy and detail.
VHF – R5 Dental Milling Machine
The R5 Dental Milling Machine by VHF is a versatile milling solution suitable for zirconia ceramics and other materials. It offers a large milling area, allowing for the production of multiple restorations simultaneously. The R5 Dental Milling Machine incorporates an intelligent tool management system and provides high-speed milling with precision and reliability.
Please note that the availability of specific models may vary, and it's always recommended to consult the manufacturers or authorized distributors for the most up-to-date information on available models and features.
Chapter Four – How Zirconia Ceramics are Made
The process for making zirconia ceramics involves the calcination of zirconium, which includes the heating of a material to an extreme temperature but limiting the amount of oxygen. The initial steps of the process are to remove any impurities and create thermal decomposition.
Zirconia, or zirconium oxide, is a crystalline oxide of zirconium, a lustrous, grayish white, soft, ductile, and malleable metal that is highly resistant to corrosion. The metal zirconium has been used for centuries with other metals since it easily forms stable compounds.
The Making of Zirconia Ceramics
Preparation of Composite Powder
The preparation of the composite powder includes mixing, which can take various forms, including mechanical, multiphase suspension, sol suspension, and sol gel. Each of the different methods has their benefits and are chosen to ensure a complete blending of the composite powder.
Mechanical Mixing – Mechanical mixing is the easiest to understand but has the least guarantee of success of uniform dispersion of the components. In the majority of cases, mechanical mixing creates a mixture with high porosity, which leads to inferior mechanical properties of the zirconia material.
Multiphase Suspension Mixing – The first step in multiphase suspension mixing is to prepare a single phase suspension with dispersed components. The next step is to determine the conditions necessary for the particles of each phase to disperse uniformly and completely. The uniformly mixed power is prepared using common flocculation conditions where the flocculant absorbs the submicron flocs formed from combining the suspended materials and bridges the gap between them.
Sol Suspension – The suspension of nano sol, a heterogeneous mixture, allows for the mixing of suspensions. If the solid content is high, the sol can be stirred or heated to create high mixed nano composite ceramics.
Sol Gel – Sol gel produces solid materials from very small molecules and involves converting monomers into a colloidal solution as a foundation for the gel. It produces uniformly mixed nano powder.
Grinding and Compacting
The mixed material is combined with a stabilizer to form a ball, which has a small amount of binder added and is compressed under pressure of 60 MPa up to 100 MPa. The compaction process is used to make the zirconia oxide powder and creates close contact with the stabilizer particles.
Sintering Process
The quality and proper preparation of zirconia ceramics for processing are highly dependent on sintering, which heats the stabilized zirconia powder to well over 1000o C. The sintering process can be performed in several ways with electric, high pressure, activation, and hot press being three of the most common processes.
Sintering is a method for consolidating the ceramic powder by heating the green compact to a temperature that is below its melting point, which causes the zirconia particles to diffuse. The pores in the material diminish or close up, as can be seen in the diagram below.
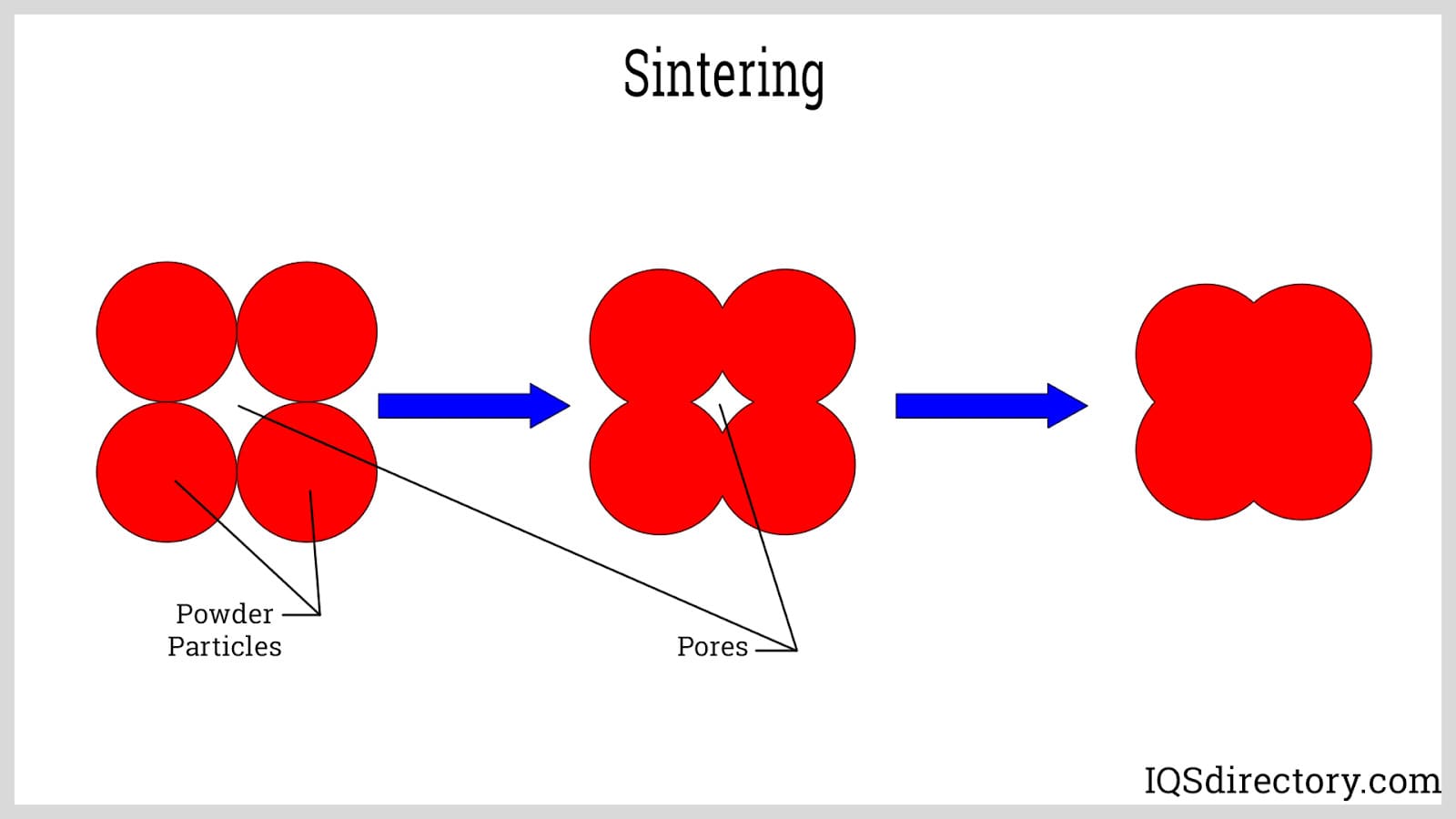
Electric Field Sintering – Electric field sintering uses a direct current (DC) electric field. The green material is placed in direct contact with electrodes in the furnace. An electric field is activated until the flash phenomenon occurs. Densification happens quickly and radically reduces the sintering temperature.
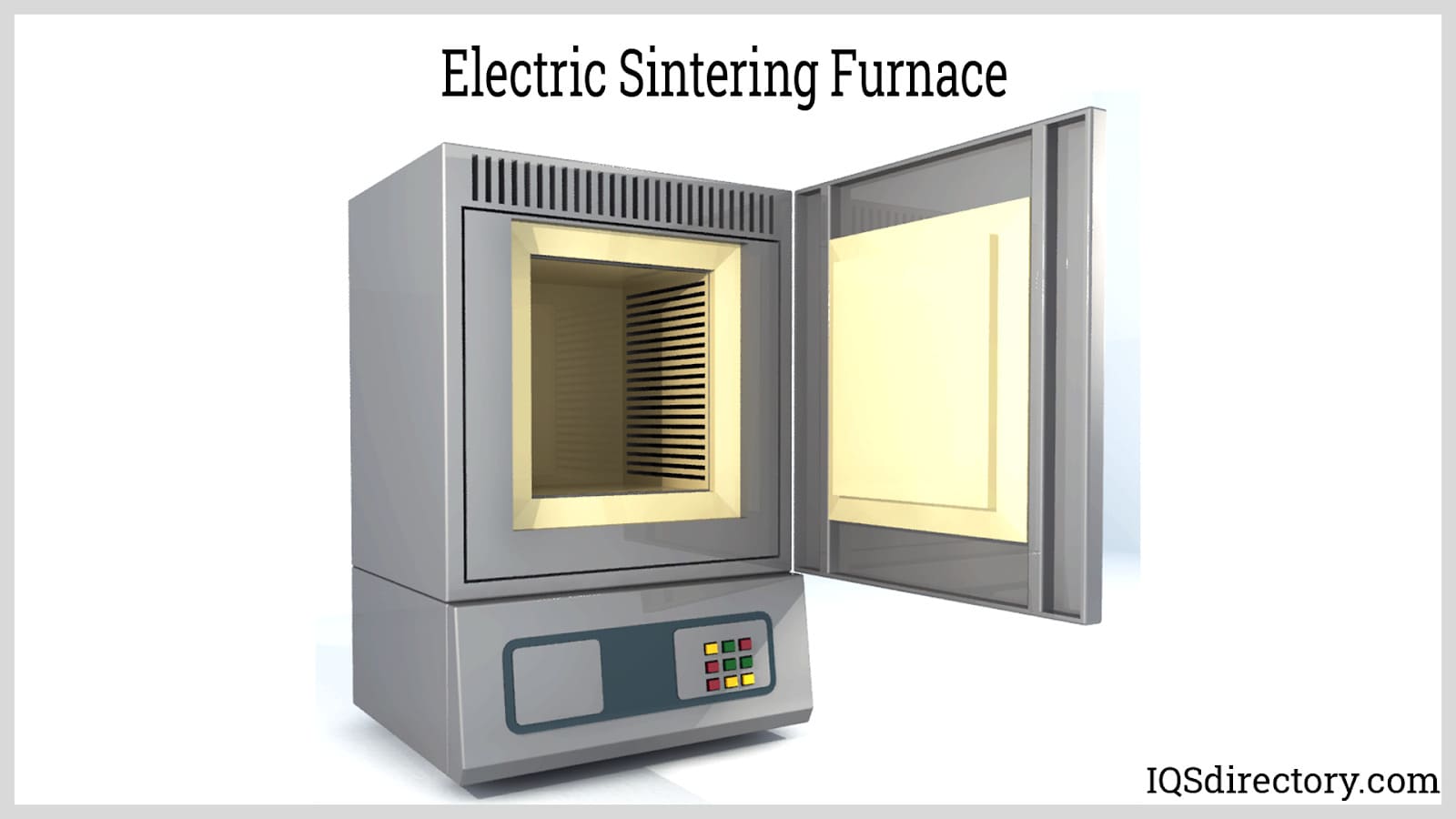
High Pressure Sintering – In high pressure sintering, zirconia ceramic powder is sintered at pressures of hundreds of thousands of atmospheres. It assists the material in reaching high density, has fine crystals, and changes the crystal structure and its atomic and electronic state. For high pressure sintering to be successful, it is necessary to mold materials, vacuum seal them, and use very pure zirconia material.
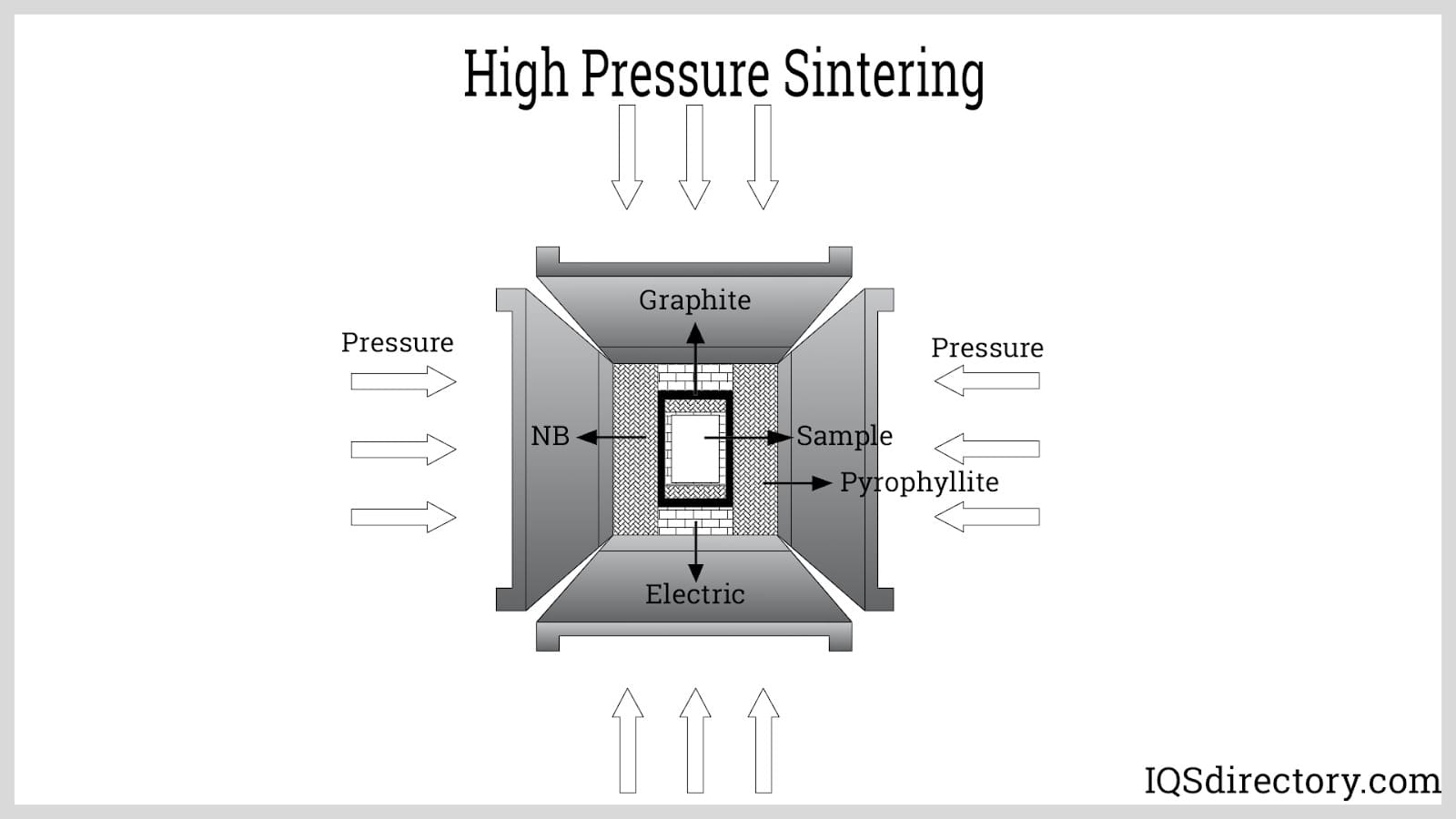
Activation Sintering– Activation sintering involves using physical or chemical methods to force the molecules of the reactants into a high energy state during and before sintering. The various physical methods that use activation sintering include electric field, magnetic field, and ultrasonic or radiation. Chemical methods use redox reactions, dissociation oxides, halides, and hydroxides. Activation sintering uses a reduced sintering temperature, has a shorter sintering time, and improves the sintering effect.
Hot Press – Hot press sintering has developed from the technology used for activation sintering. The hot press sintering process takes the activated state of the reactant from the activation process and uses higher energy during the decomposition phase change to create a higher density ceramic material but at a much lower temperature, lower pressure, and in less time.
The design is an exceptionally efficient hot pressing method.
Cold Sintering – Reducing sintering temperatures is a major thrust reducing carbon emissions from factories and industry. Several different methods have been introduced to meet the demand and be in line with the ever changing air quality standards.
Cold sintering uses a liquid to aid in the rearrangement and interdiffusion of the particles with some pressure and a small amount of heat. During the process, the powdered material is mixed with a liquid in which it is partially soluble. The wet material is placed in a die under pressure of 100 MPa up to 500 MPa and heated to less than 300o C. As the heat and pressure are applied, the solid material precipitates. For the moment, the process is unavailable for all zirconia ceramic materials.
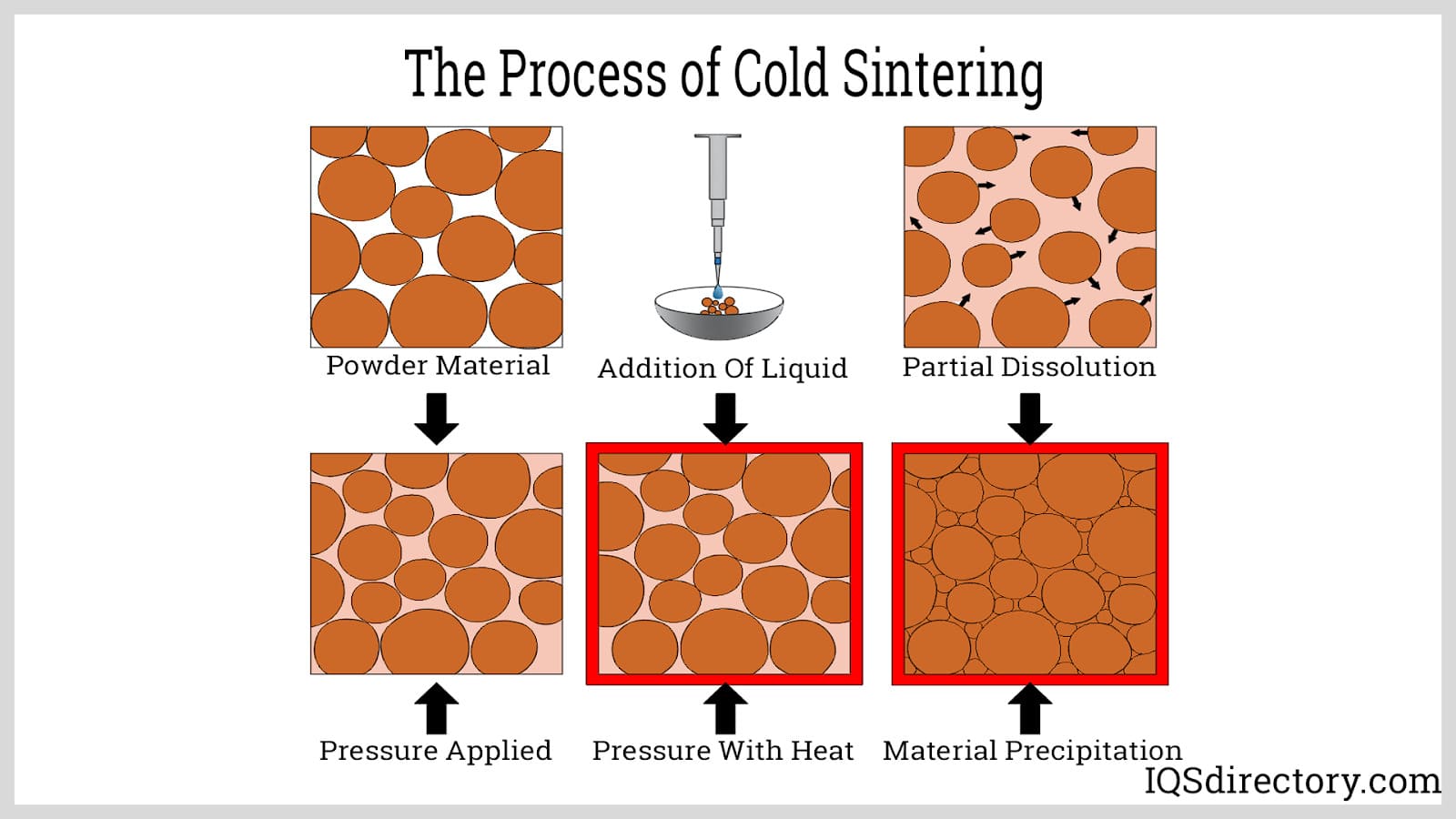
Machining of Sintered Zirconia Ceramics
Machining of sintered zirconia ceramics is a necessary part of preparing the solidified material for an assortment of applications. There are challenges to the machining of zirconia ceramics mainly due to its exceptional hardness, which is somewhat similar to that of steel. The bending strength and fracture toughness of zirconia ceramics is somewhat compromised with the addition of heat or an increase in temperature. This characteristic necessitates using high speed cutting tools with speeds of 500 meters per minute (m/min) up to 670 m/min. The increase in speed also decreases the amount of flank wear on the cutting tool.
Special cutting tools are required for machining zirconia ceramics and include natural, polycrystalline, chemical vapor deposition (CVD) diamonds, and cubic boron nitride cutting tools.
Natural Diamond (ND) – ND tools are used to prepare turning tools.
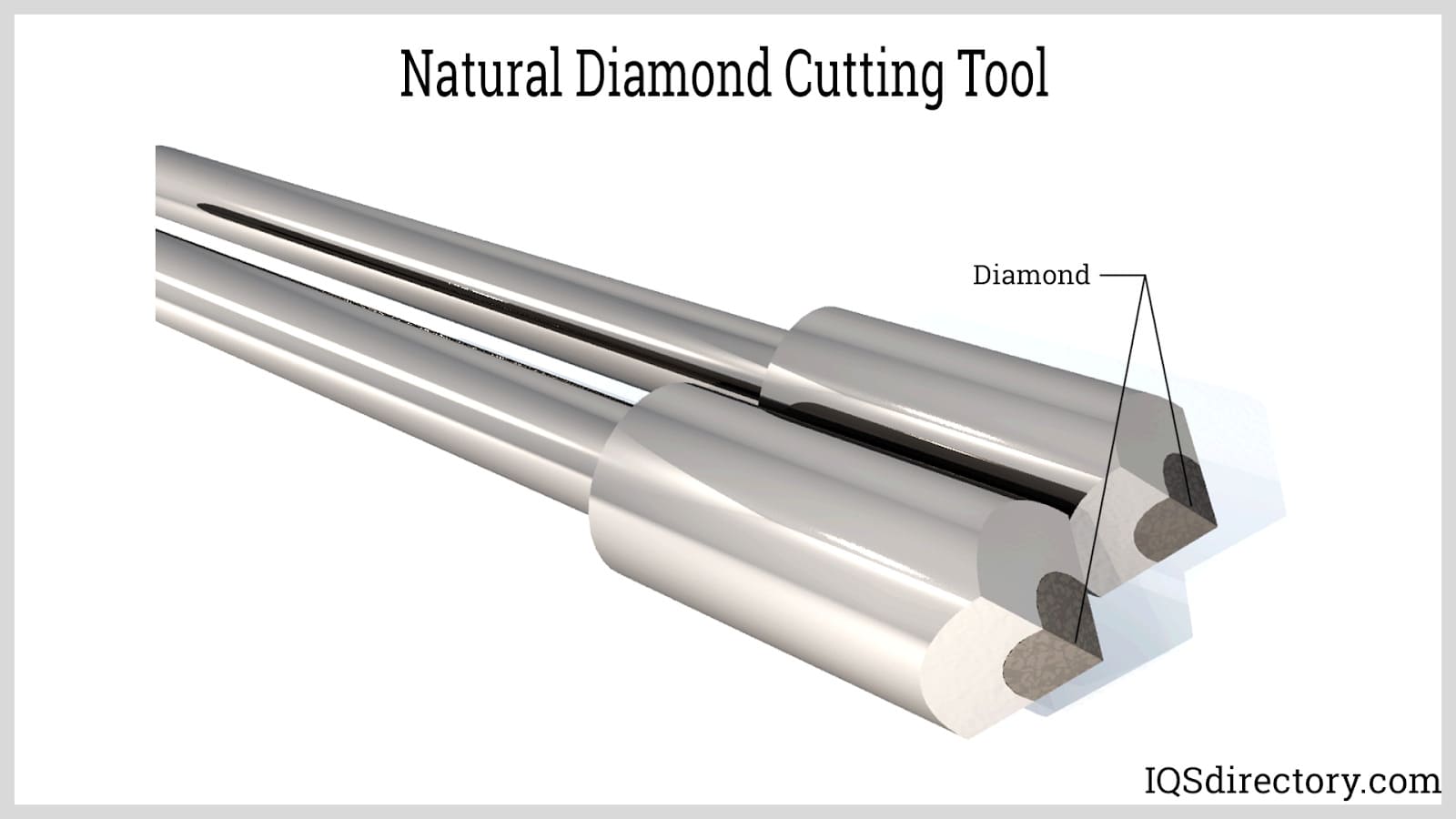
Polycrystalline Diamond (PCD) – PCD is a hard material that was developed in the 1970s. It has excellent mechanical, thermal, chemical, and electric properties and has become an essential tool for cutting processes. PCD cuts at high speeds with exceptional stability and precision. A major benefit is its ability to perform dry cutting.
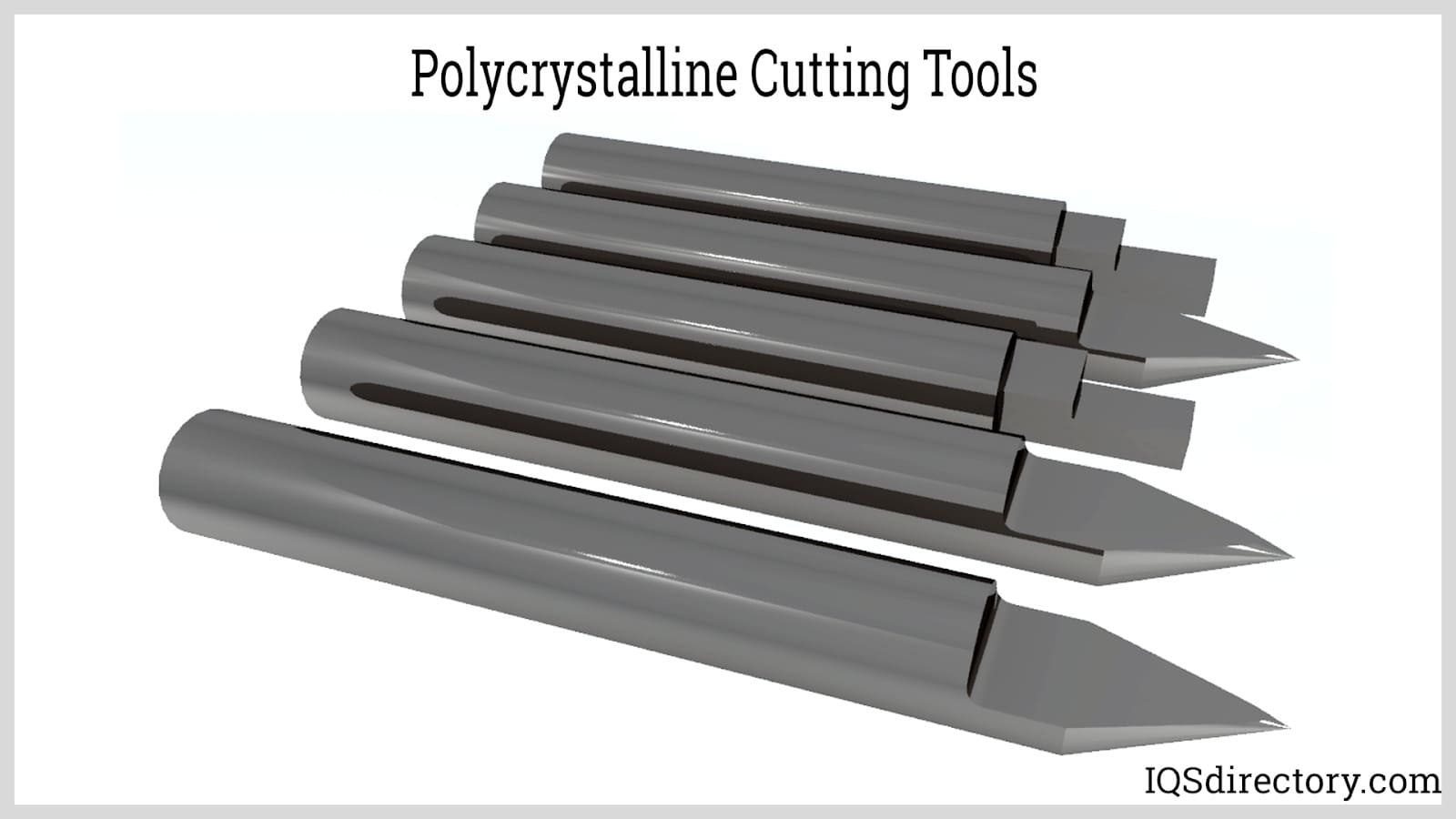
Chemical Vapor Deposition (CVD) – CVD cutting tools are ideal for machining zirconia ceramics since they perform the best when cutting materials that form a powder during the cutting process. They are primarily used in situations where cutting is abrasive without chipping.
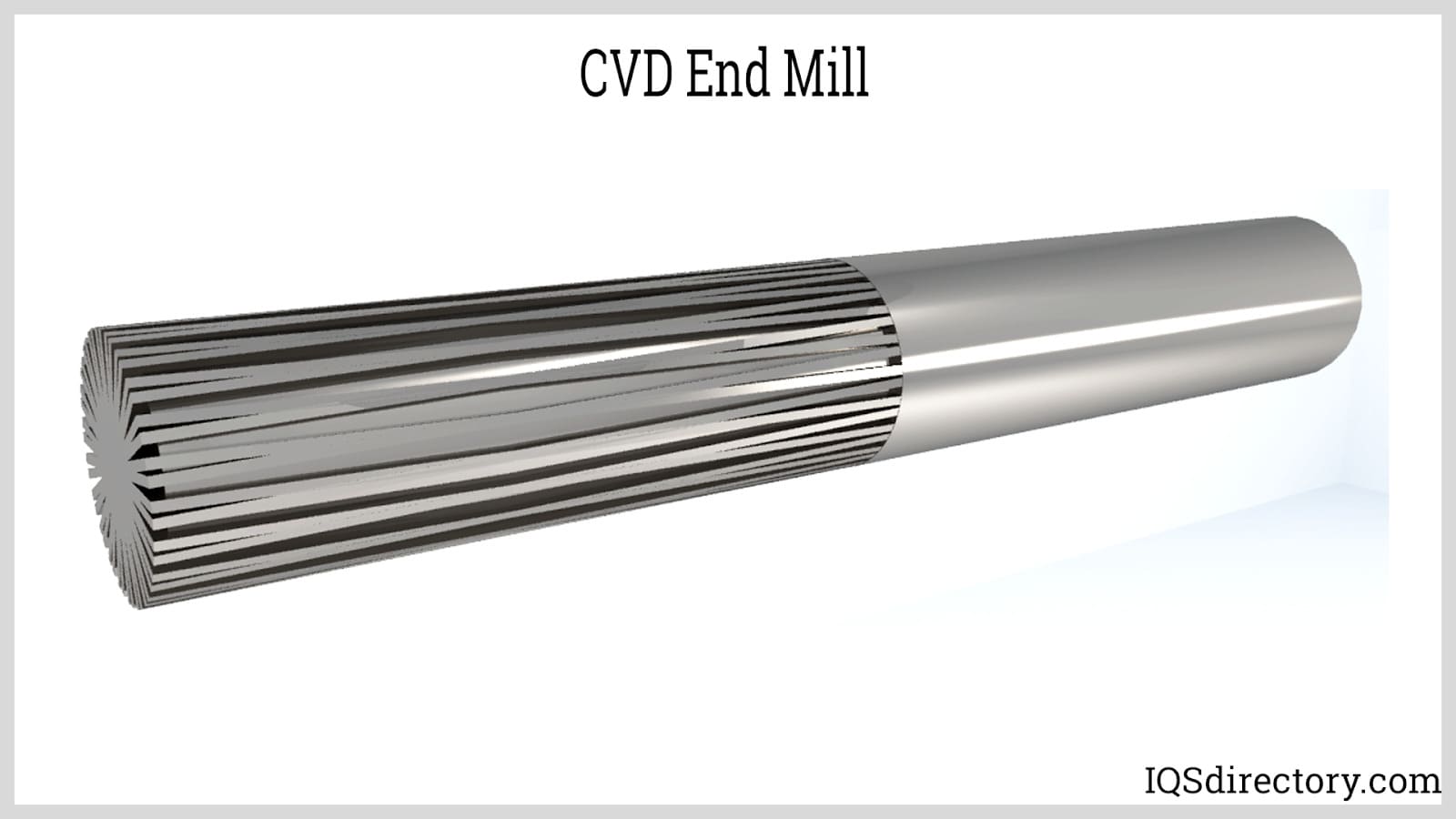
Cubic Boron Nitride (PCBN) – The BN structure of a PCBN tool resembles a diamond and performs like one. PCBN tools can be configured in several different forms and have the same material removal and wear resistance as diamonds but at a lower cost.
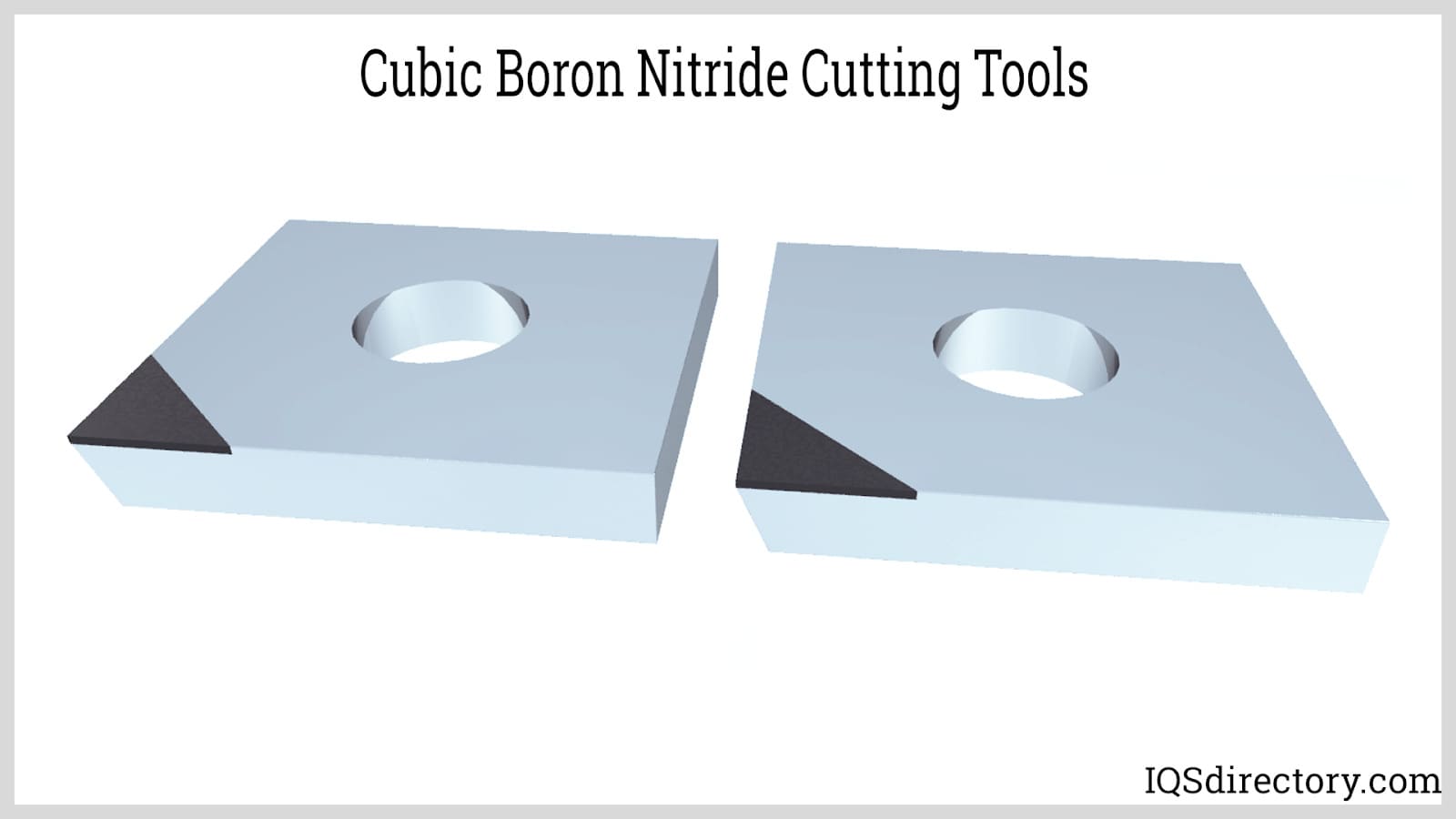
Chapter Five – Uses for Zirconia Ceramics and Zirconia Toughened Alumina
The hardness and strength of zirconia ceramics make them an ideal material for several applications. They can be found in prosthetic materials for dentistry and bone replacements and as ideal materials for automobiles and high altitude aircraft. The diverse uses of zirconia ceramics have made them a viable and useful material for engineers in creating new and unique designs and functions.
Aside from grinding and cutting zirconia ceramics, they are shaped and formed using injection molding, laser shaping, and cutting. Injection molding is used for high end and high volume production, while laser cutting is limited to a small number of products.
Zirconia toughened alumina is used in all of the applications where zirconia ceramics are used. Its diverse range of properties makes ZTA applicable to applications in the medical field and as material for pumps, valve seals, bushings, pump parts, cutting tools, and engine components. It is capable of withstanding heavy loads without degradation making it useful for load bearing applications.
Whenever zirconia ceramics are present, it is very likely that ZTA is also in use as an upgrade or essential component.
Zirconia Ceramic Uses
Uses in Dentistry
Three forms of zirconia ceramic are used in dentistry, which are tetragonal zirconia polycrystal, magnesium stabilized, and ZTA. Zirconia ceramics have the necessary properties to perform effectively for tooth restoration. It is aesthetically pleasing and has the required strength and is a substantial improvement over the metal dental materials of the mid-20th Century since it does not cause allergic reactions.
Uses for zirconia in dentistry includes posts, crowns and bridges, and implants.
Dental Posts – The aesthetic value of zirconia ceramic dental posts make them the first choice in restoring the anterior of teeth. Since the 1990s, they have served as a replacement for metal posts that caused a gray discoloration. The use of zirconia ceramic posts eliminates a corrosive reaction in the mouth and surrounding tissue, which includes burning, pain, and a metal taste.
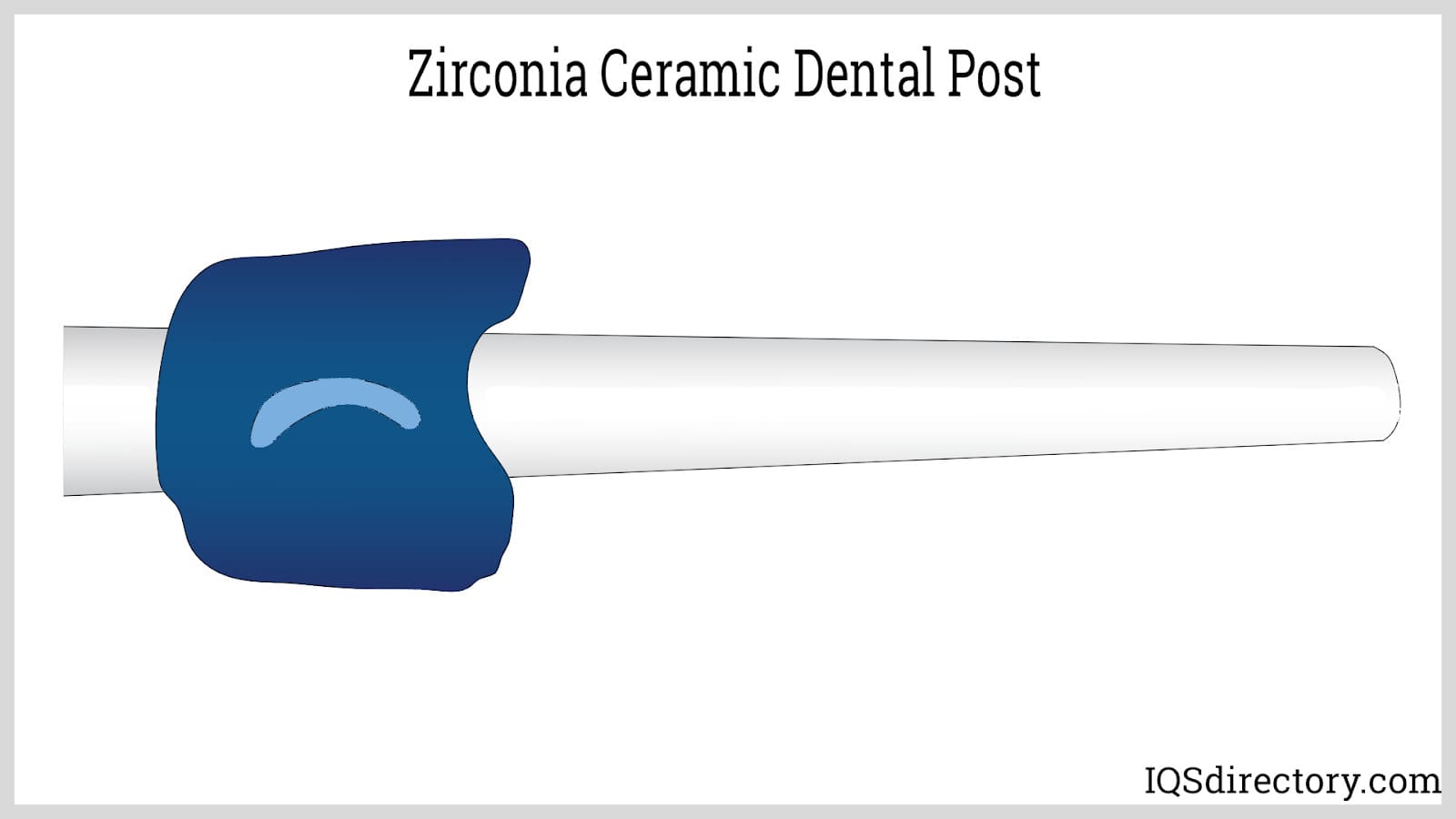
Crowns – Zirconia crowns are chosen over metal and gold ones due to their strength, durability, and aesthetic appearance and can be full, translucent, or layered zirconia. The adaptability of zirconia ceramics makes it possible to cement them in place or install them using screws. The strength of zirconia ceramic material makes it possible to use it with patients who grind their teeth or chew forcefully.
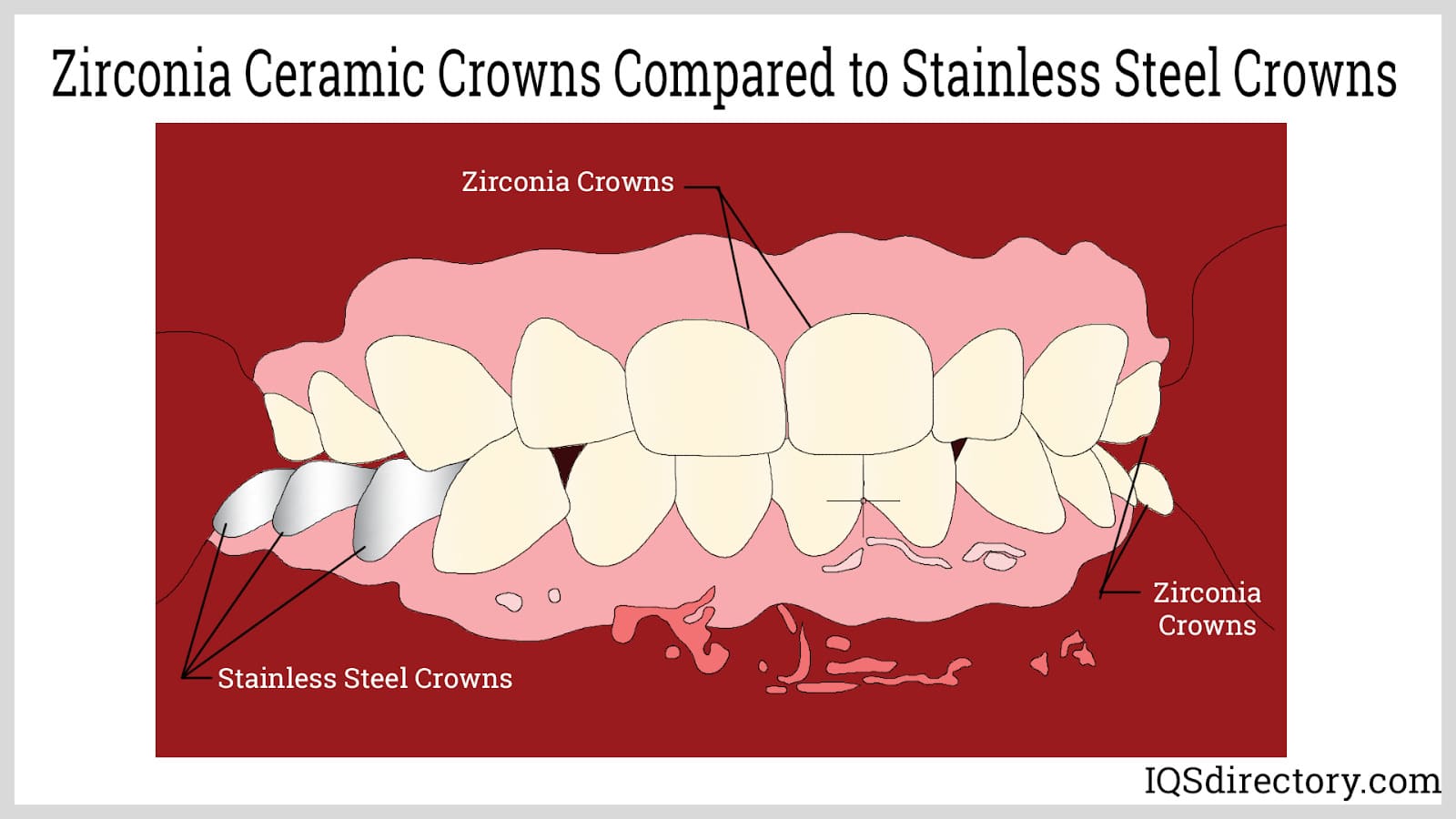
Abutments – The use of zirconia ceramic for abutments is due to its versatility which allows it to be designed using CAD or a wax impression. These methods allow the abutment to be custom designed for a perfect fit. When there is a thin gingival tissue, a zirconia ceramic abutment blocks light from exposing the abutment and assists in maintaining the aesthetic appearance. Their color can be adjusted to match the adjacent teeth.
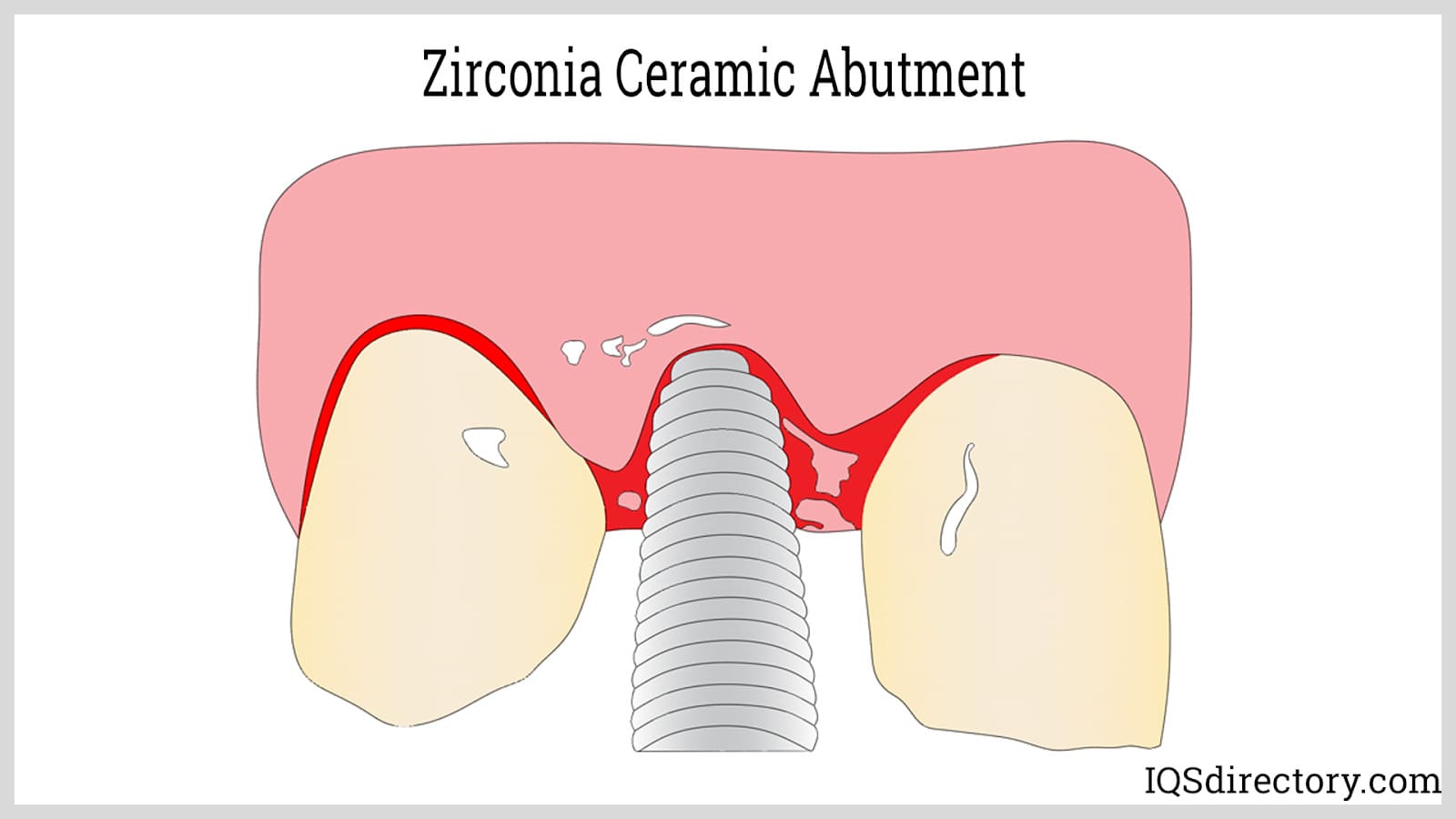
Zirconia Ceramic Brackets – Polycrystalline zirconia ceramic brackets have become an alternative to alumina ceramic brackets and a replacement for metal ones. Brackets are used in orthodontia as a restraining element for teeth and to keep the wires of braces off the teeth.

Dental Implants – Zirconia ceramic dental implants were approved for use in 2011. They are biocompatible and have excellent stability. For many years, the only method for inserting dental implants had been metal screws that did not have the correct aesthetic appearance and caused allergic reactions or sensitivities. Zirconia ceramic implants eliminate dark lines along the gum line and are available in different configurations.
Additionally, metal free zirconia ceramic implants are a better choice for the health of the gums since zirconia ceramic retains less plaque and calculus, which is especially true with one piece implants. The exceptional flexural strength and fracture toughness of zirconia ceramic ensures a tight and long lasting fit.
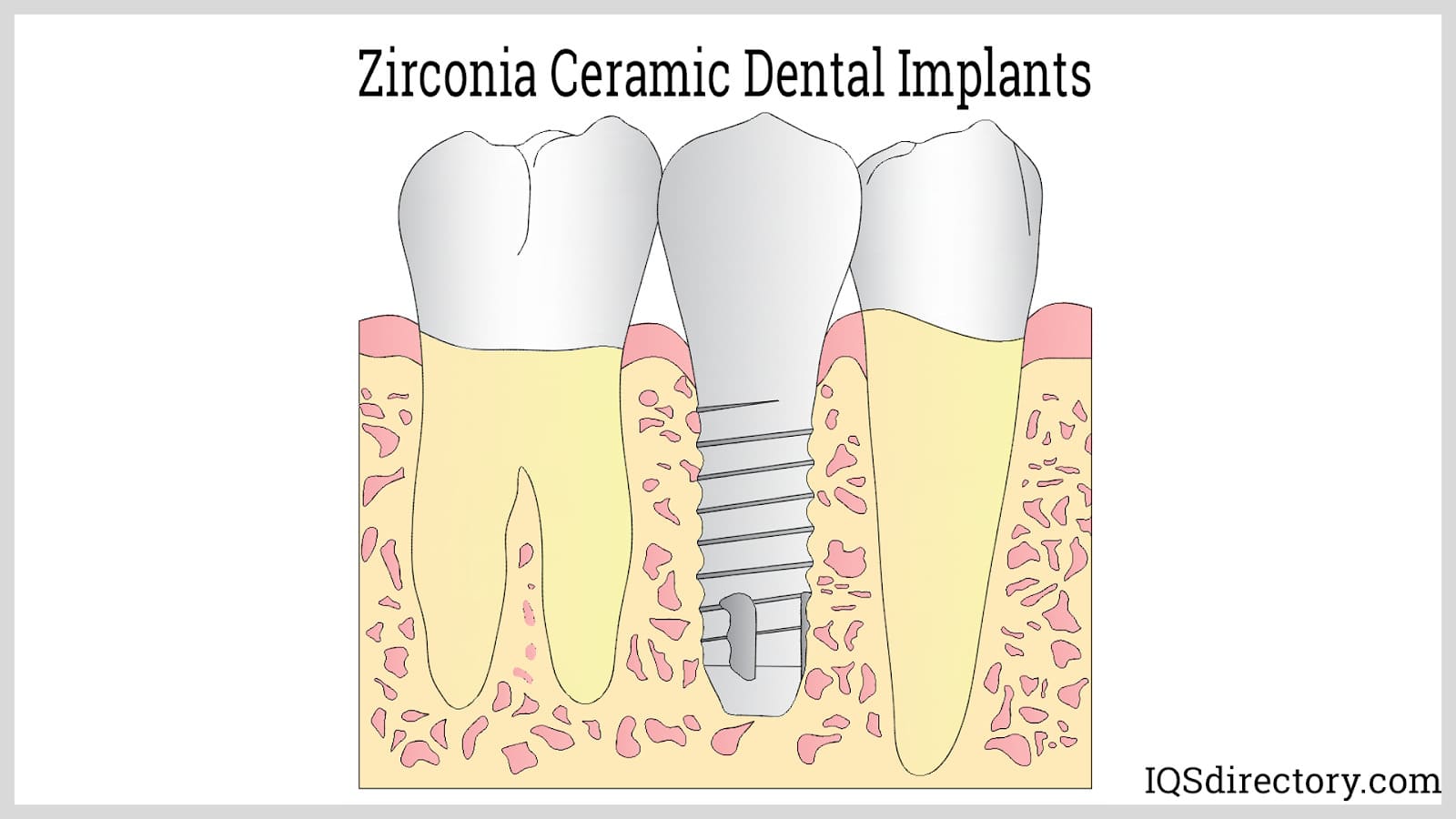
Uses in Orthopedics
Dense zirconia ceramics are used for joint replacements, especially for wear resistant bearing surfaces. Zirconia ceramics have mechanical advantages over metal alloys and can be polished to an exceptionally smooth finish. The ability of the material to be scratch resistant as a bearing surface is highly beneficial.
The most common material used to produce ceramic bearing materials is ZTA, which has a wear resistance comparable to metal and has become the first choice for hip joint replacement.
Hip Joints – Hip joints are a ball and socket type of joint. The socket is formed by a cup surrounding the ball and is protected by cartilage and lined with a membrane. When there is damage to the blood supply, the bone weakens and begins to collapse. As the condition advances, it is necessary to replace the hip joint. The stem and support sockets for hip replacements are made of steel or titanium. The heads and sockets are made of zirconia ceramics due to their strength and long wear. This is especially true in cases where hips have to be replaced early in life.
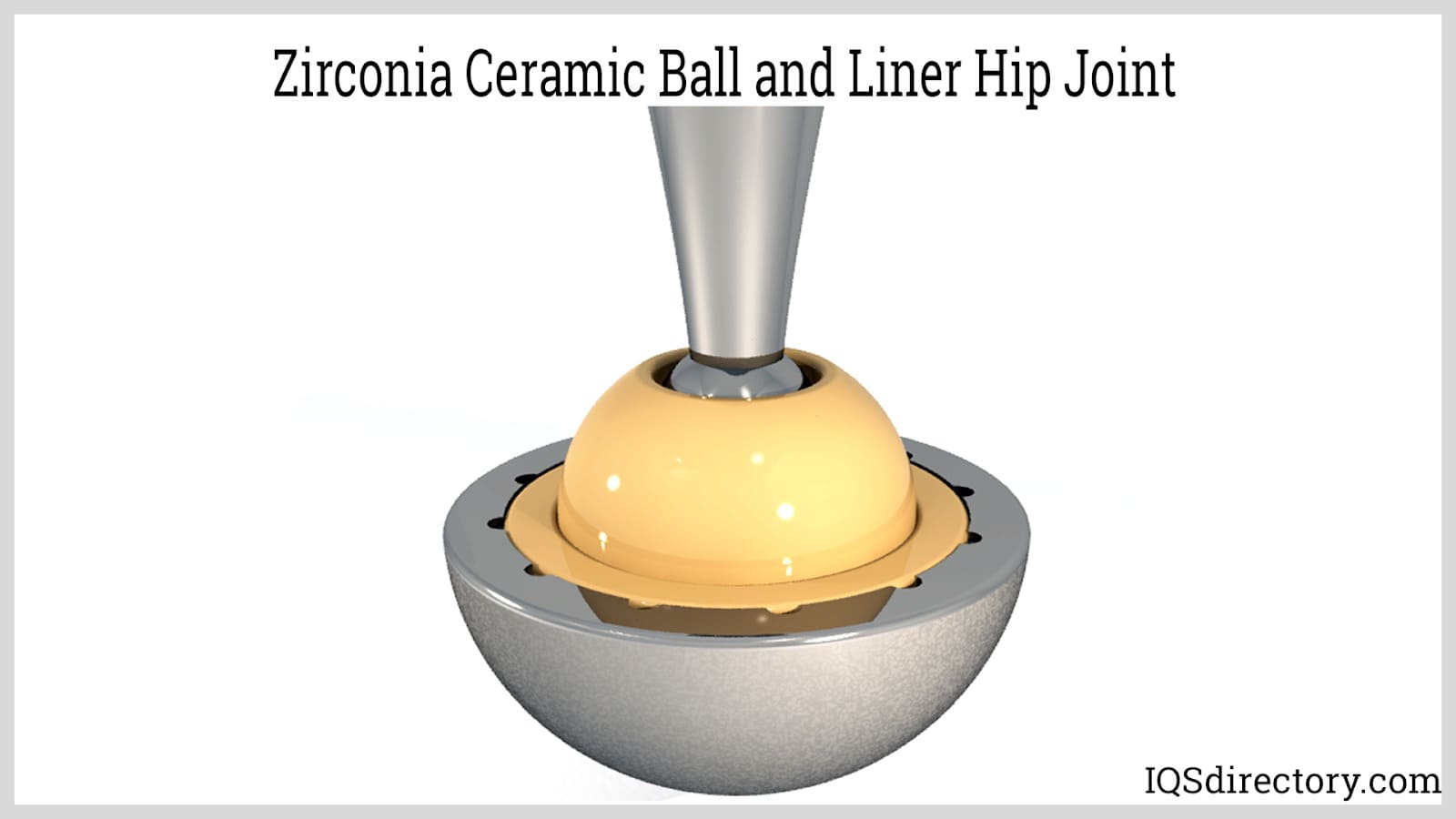
Knee Replacement – The replacement of knees with zirconia ceramics is necessary when arthritis develops in the joint and causes pain. In tests of total knee arthroplasty with zirconia ceramic, it was found that there was substantial improvement of the movement of the knee. Completed research has proven that zirconia ceramics have an excellent survival rate and assist in joint functionality.
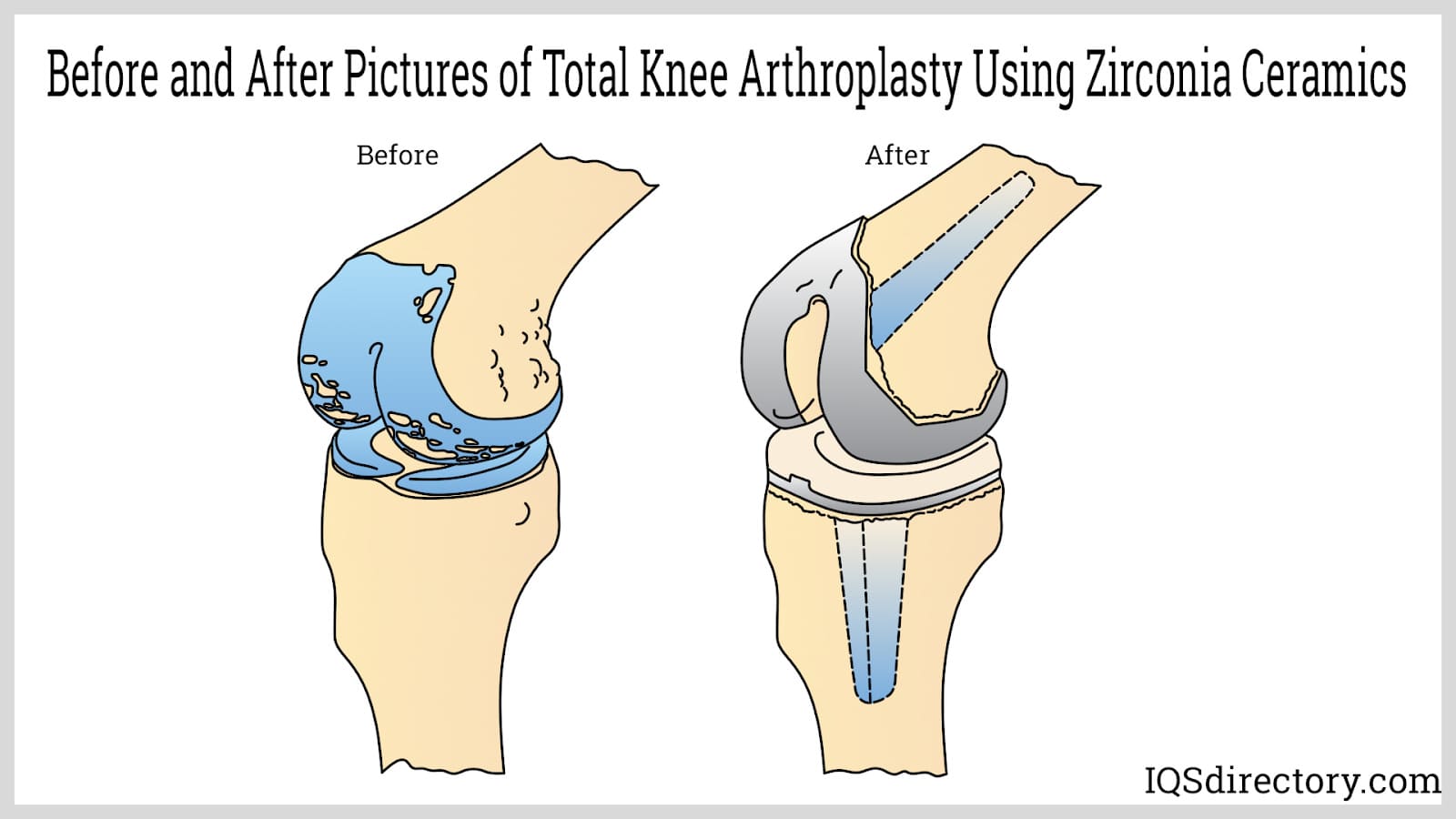
Cutting Blades
Cutting blades made of zirconia ceramics are suitable for cutting membrane materials such as paper, aluminum, and steel. They have less leftovers, a low reject rate, and less frequent need for blade replacement. Their high hardness, fine grain, and steel like strength make them far more durable than other materials. Additionally, the blades are resistant to corrosion, erosion, and wear, making them capable of surviving any type of environment.
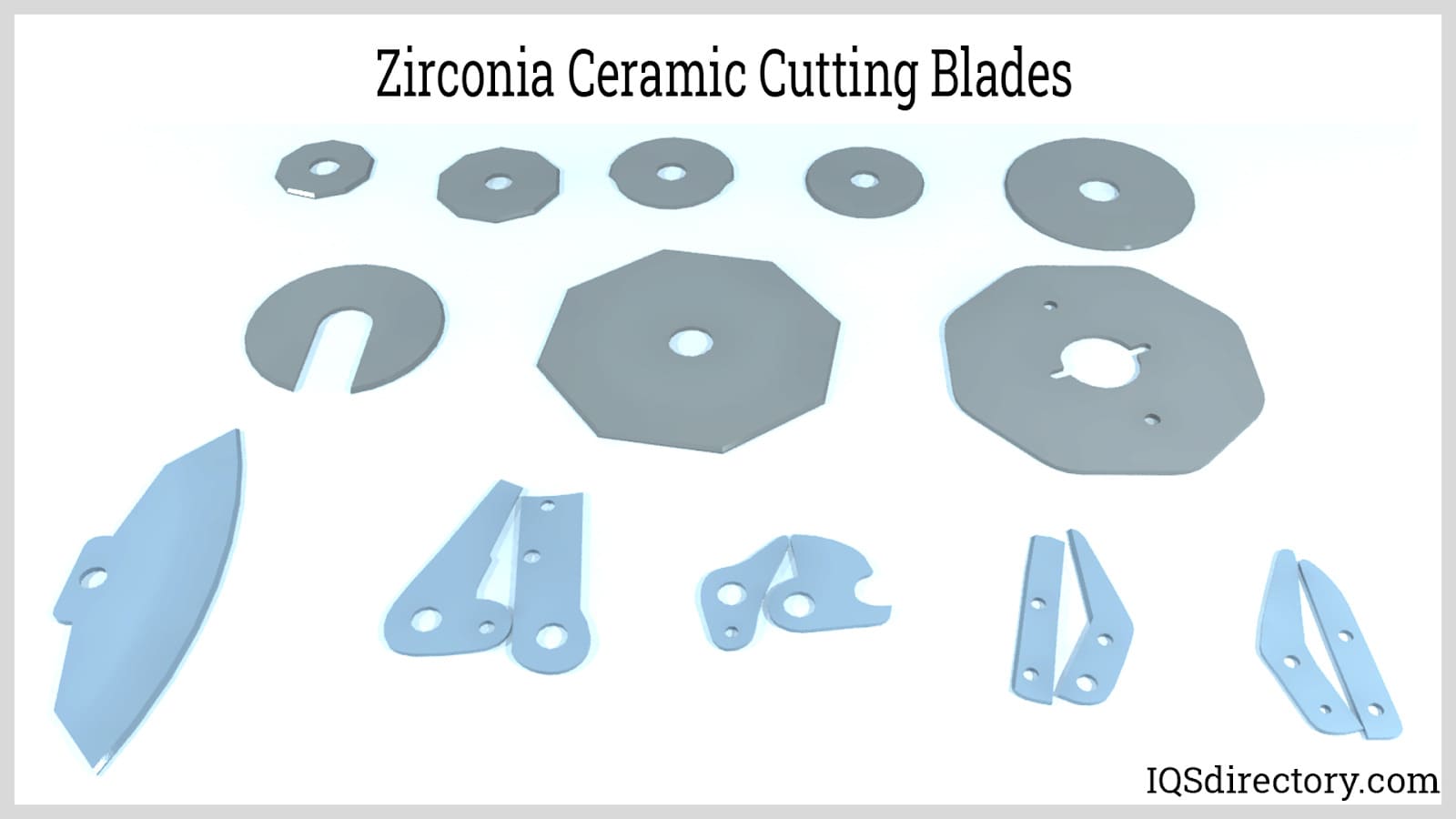
Ceramic Bearings
Zirconia ceramic bearings are wear, corrosion, high temperature, extreme cold, and magnetoelectric field resistant. They do not require oil lubrication and can be used in extreme conditions as well as harsh stressful environments. They have traditionally been used in cooling fans where they have demonstrated long life and noise stability, which has made them ideal for use in computers.
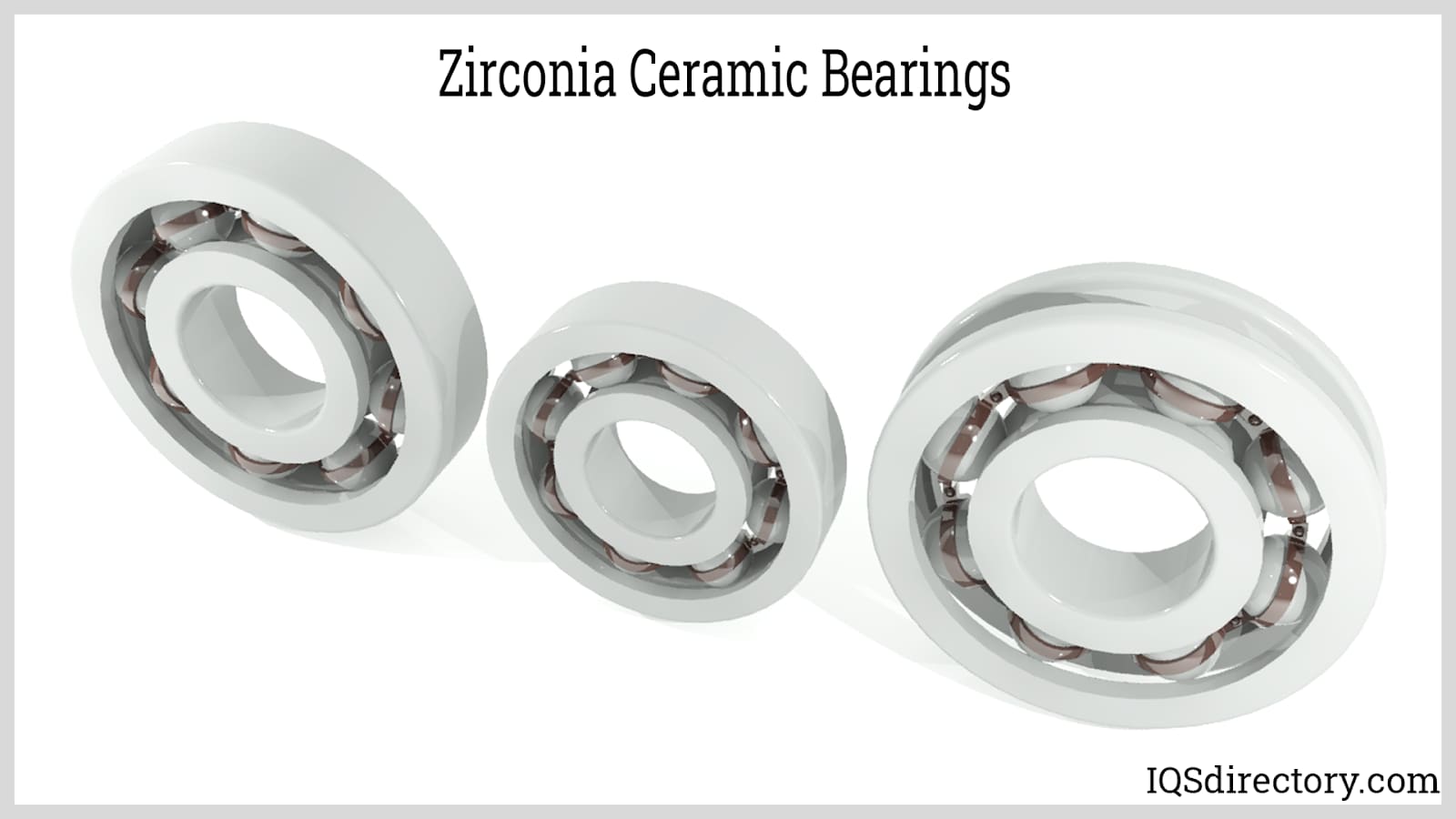
Zirconia Ceramic Valves
The majority of valves have been made of metal for many years. The susceptibility of metal to corrosion has produced significant damage to the working life and reliability of metal valves, which has severely impacted system and process functions.
Pipelines handle a wide assortment of chemicals and materials such as hydrogen sulfide, carbon dioxide, and organic acids present in oil, gas, and reservoir water. These materials are destructive and damaging to the surfaces of metals and cause rapid deterioration. The exceptional wear, corrosion, temperature, and thermal shock resistance of zirconia ceramics has made them the perfect replacement for metal valves.
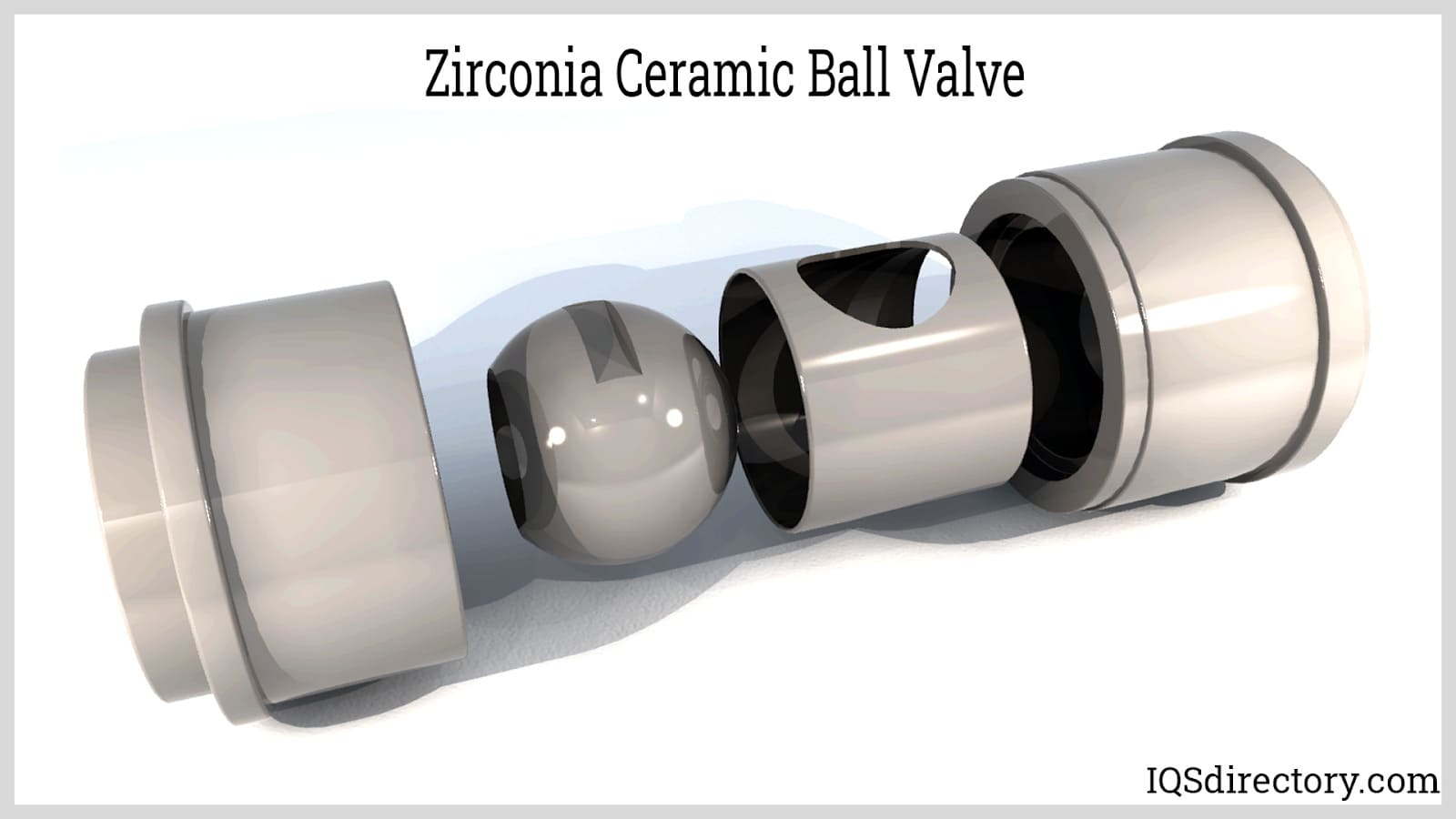
Grinding Beads
Zirconia ceramic grinding beads are made of yttrium stabilized zirconia due to its excellent crystallization and high performance. They are commonly used in grinding applications that require ultra-fine grinding and dispersion of paints, coatings, electronic materials, and magnetic materials.
The characteristics that make zirconia ceramic beads ideal for grinding include shortened grinding times, high hardness, exceptional toughness, nonporous smooth surfaces, roundness, suitable for high viscosity materials, and fineness.
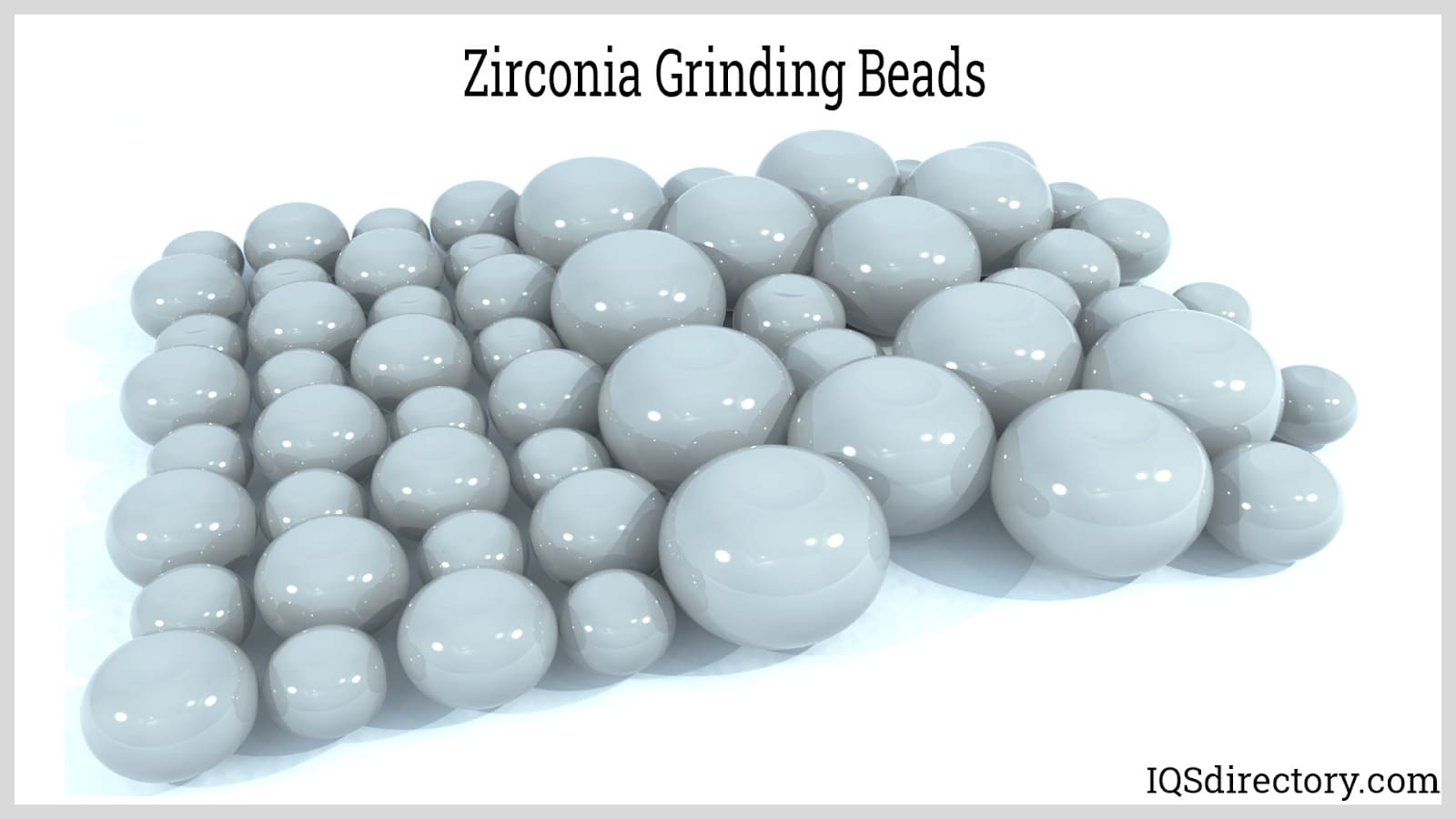
Zirconia Ceramic Crucibles
Zirconia ceramic crucibles are used as refractory and insulating containers that provide a clean melt at temperatures reaching 1900o C and above. They are specially designed for melting superalloys and precious metals due to their chemical inertness, excellent thermal shock resistance, and the capability of reaching temperatures of 2200o C.
Zirconia ceramic crucibles are fully stabilized with yttrium or partially stabilized for corrosion and wear resistance. The many sizes and varieties of zirconia ceramic crucibles range in size capacities from 2 mL up to 300 mL at heights of 15 mm to 80 mm and wall thicknesses of 1.5 mm to 3.5 mm.
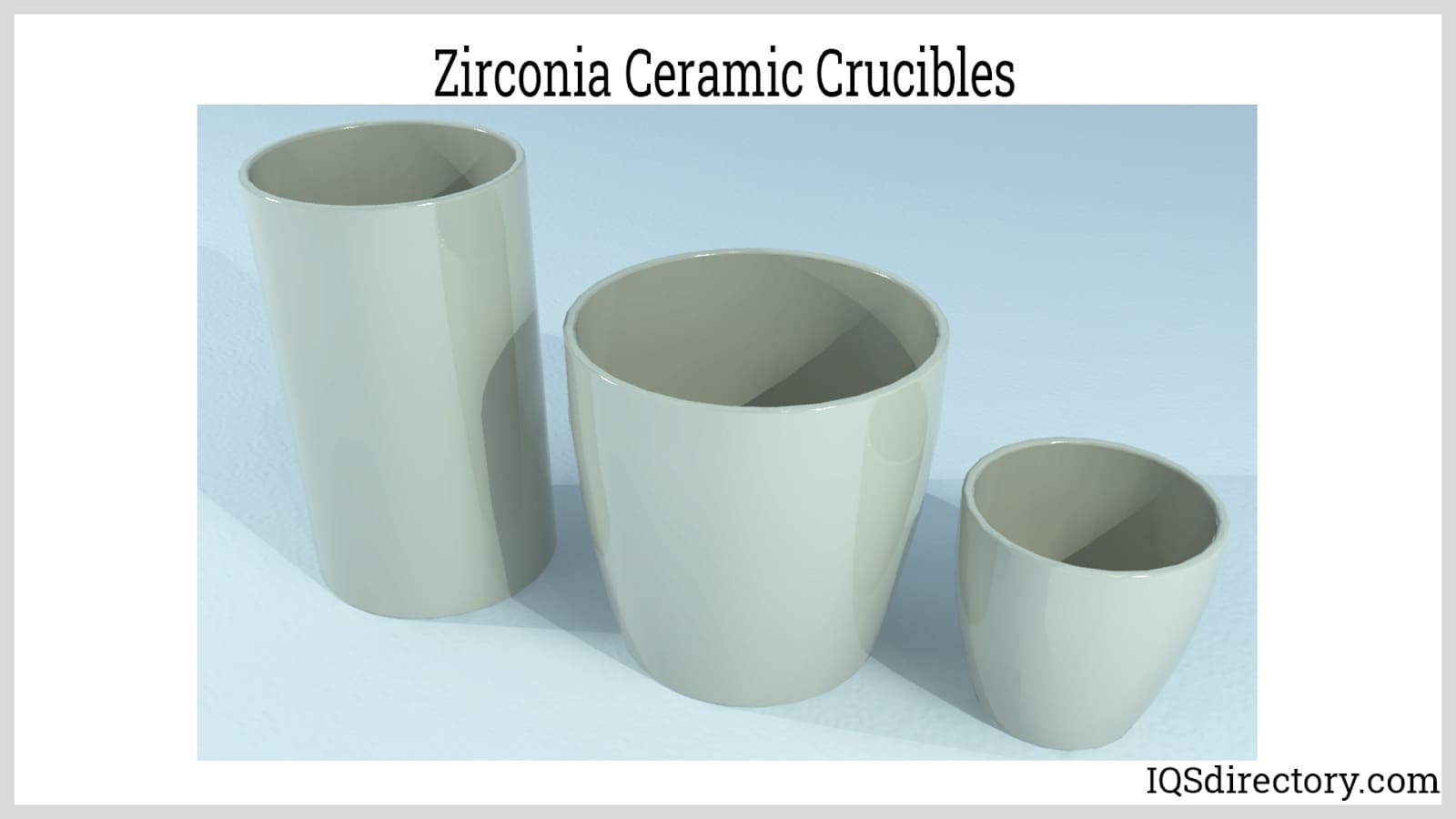
Filter Plates
The shock resistance, high temperature strength, porosity, and surface area of zirconia ceramics make them capable of absorbing impurities from molten metal while preventing bubbles in the metal. This factor reduces turbulence making it possible for the metal to be homogenized. Zirconia ceramic filter plates can be coated with catalysts. While the impurities are being removed, chemical reactions are conducted to improve the quality of the metal casting.
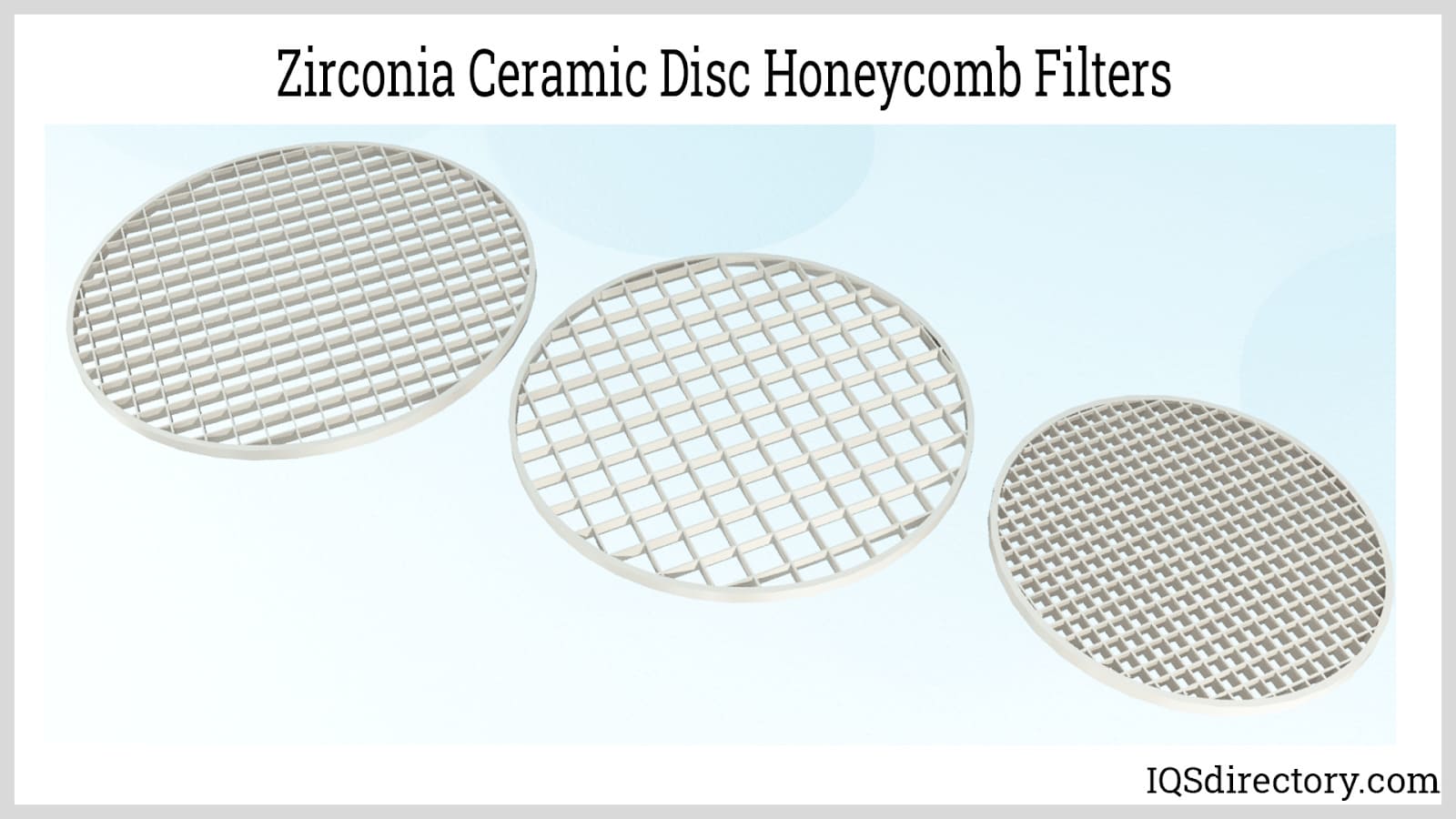
The thirteen uses for zirconia and ZTA ceramics listed above are only a small fraction of the many ways this highly durable, tough, and strong material is used. Zirconia and ZTA ceramics can be found in the aerospace and automobile industries due to its light weight and strength. It is also used as a pump component, insulation, and heating elements. Researchers and engineers are constantly finding more innovative and practical uses for zirconia ceramics and ZTA ceramics.
Chapter Six – Grades of Zirconia Ceramics and ZTA
The determination of the grades of zirconia ceramics is based on the type of stabilizer used, which can be yttria, alumina, magnesium, and cerium. The addition of stabilizers is to reduce the tendency of the zirconia ceramics to crack when their volume increases by more than 9%. The condition is controlled by substituting Zr+4 ions in the crystal lattice with slightly larger ions.
Zirconia Ceramic Grades
Yttria (YSZ or YTZ) Grade
YSZ is one of the strongest of the zirconia ceramics. It has the highest flexural strength of all zirconia ceramics. Its chemical inertness allows it to be used in the food and cosmetic industries. On the Mohs hardness scale, YSZ has a rating of >9, with diamond being the ultimate hardness at 10.
The high wear resistance of YSZ prevents any contamination of it during milling, grinding, or dispersion. It has a density of >6gm per cm3, making it the most dense ceramic material.
Alumina (ZTA) Grade
ZTA ceramics have additional strength and toughness at a lower cost than other zirconia ceramics. The combination of aluminum oxide with 10 to 20% of zirconium oxide offers increased strength, toughness, hardness, and wear resistance than is found using alumina alone. The biggest change in the material is caused by transformation toughening, which significantly increases the fracture toughness of ZTA.
When placed under stress, zirconia particles change their crystalline structure from tetragonal to monoclinic. This causes a volume expansion that compresses the cracks in the alumina matrix. This transformation makes ZTA applicable for applications requiring structural strength.
Magnesium (MSZ) Grade
MSZ has small precipitates of tetragonal phase that form inside of its cubic phase grains. The precipitates change from meta-stable to tetragonal phase to stable monoclinic phase when a crack appears in the material, which causes the precipitate to expand and close the crack to create toughness in the material.
How MSZ is prepared determines its color, which can be ivory or yellowish orange. Ivory colored MSZ is very pure with excellent mechanical properties. It is stable at temperatures of 220o C and capable of enduring moisture rich environments.
Cerium (CSZ) Grade
CSZ is designed for use in moist environments due to its high strength and toughness. It is suited for use as sensors, instrumentation, probes, pumps, and fluid control systems. CSZ is a robust material with low temperature degradation properties and has reduced vulnerability to the effects of water. It is the best performing zirconia ceramic for wet operating conditions.
Conclusion
- Zirconia Ceramics, or zirconium dioxide ceramics, are exceptionally strong technical ceramic materials with excellent hardness, toughness, and corrosion resistance without the brittleness common to other ceramic materials. There are several grades of zirconia ceramics, with yttria and magnesia partially stabilized zirconia ceramics being the most common.
- Zirconia toughened alumina (ZTA) ceramic is a composite material with alumina and zirconia as its major elements. The structure of ZTA includes zirconia grains placed in the alumina matrix. It has additional strength and toughness compared to alumina, with a lower cost than zirconia.
- The many types of zirconia ceramics have developed from the desire of manufacturers to enhance the properties of the different phases of zirconia ceramics. The various phases require treatments to be appropriate for use in an assortment of environments. Zirconia toughened alumina is one of the many types of phases.
- The process for making zirconia ceramics involves the calcination of zirconium, which includes the heating of a material to an extreme temperature but limiting the amount of oxygen. The initial steps of the process are to remove any impurities and create thermal decomposition.
No comments:
Post a Comment