Introduction
Here is the most concise information on alumina ceramics on the internet.
You will learn:
- What are Alumina Ceramics?
- The Properties of Alumina Ceramics
- How Alumina Ceramics are Produced
- Alumina Ceramics Products
- And much more …
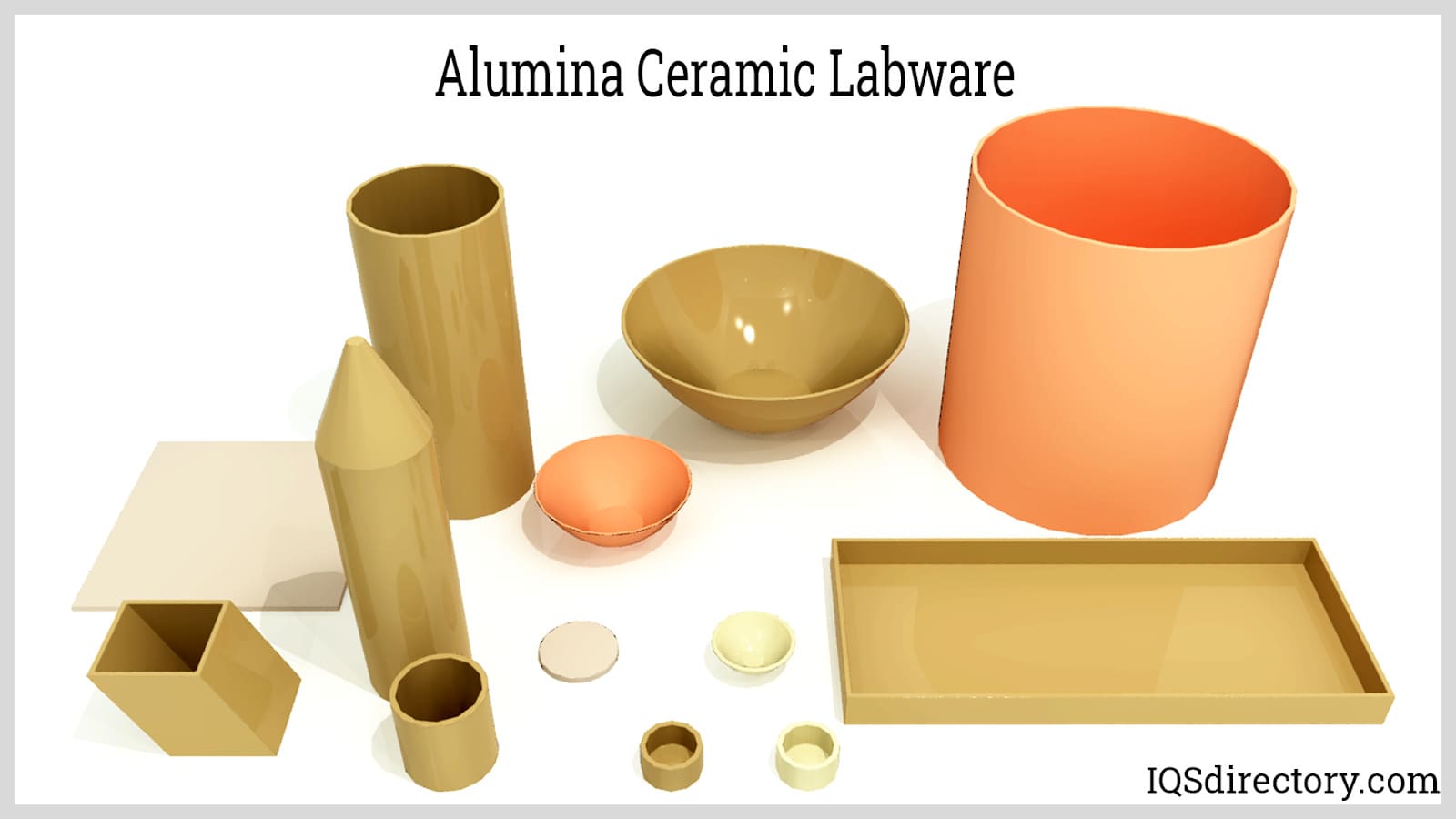
Chapter One – What are Alumina Ceramics?
Alumina ceramic is a well-known, long-wearing industrial oxide ceramic with high hardness. It is manufactured from bauxite and can be shaped using injection molding, die pressing, isostatic pressing, slip casting, diamond machining, or extrusion. Alumina ceramics have the same sintered crystalline body as sapphire and ruby.
One of the main uses of alumina ceramic is as an insulation material for electrical components. In other applications, it is used for its exceptional strength and corrosion and wear resistance.
Products made from alumina, some of which are shown in the image below, are wear, chemical, erosion, corrosion, and high temperature resistant and bioinert, making them perfect for medical implants.
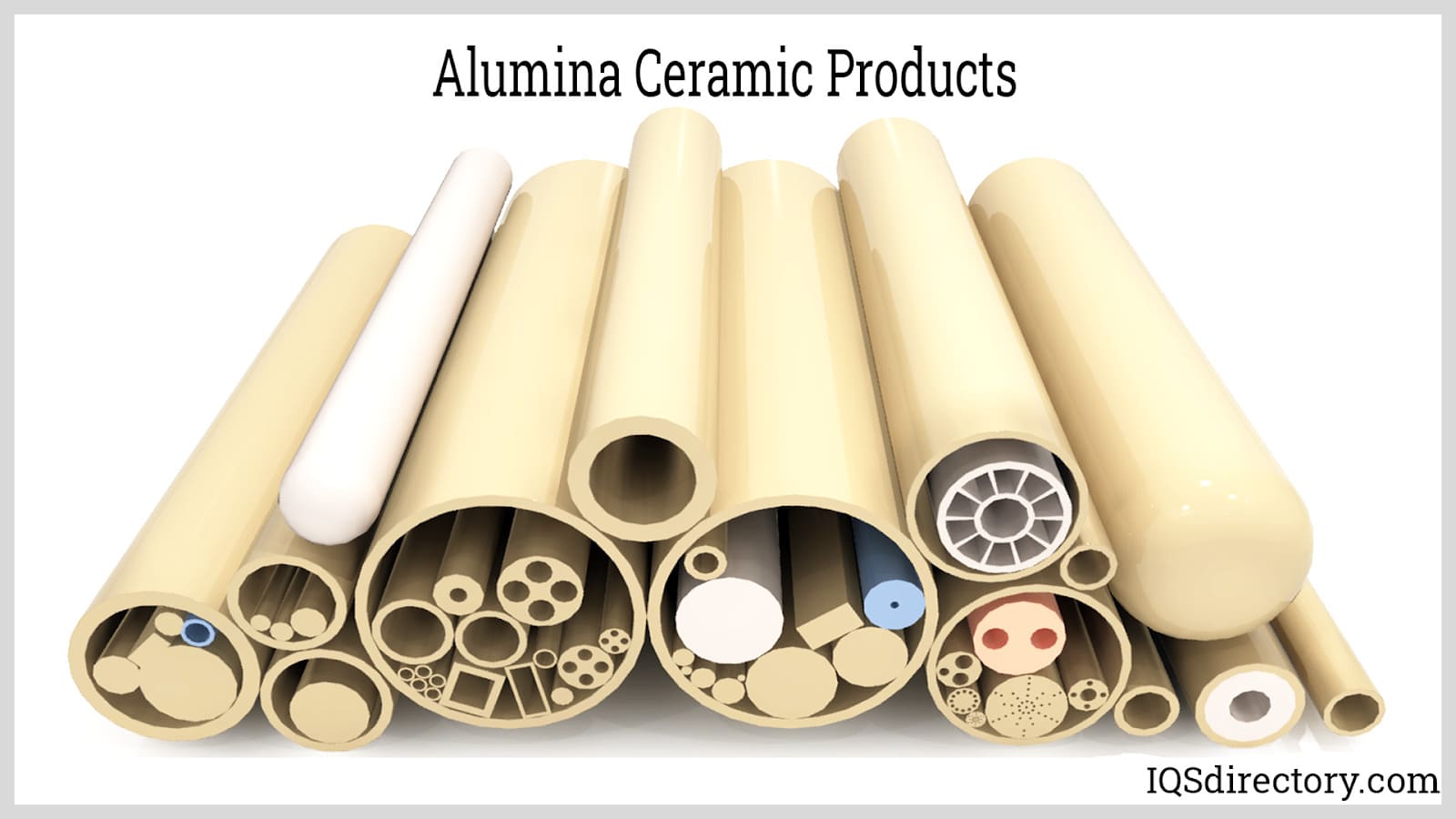
Alumina ceramics are technical ceramics due to their properties and price to performance ratio. The classification of alumina ceramics is based on their alumina content, which can vary from 70% to 99.9%. The higher the purity of alumina, the stronger is its wear and corrosion resistance.
Chapter Two – Properties of Alumina Ceramics
Alumina ceramics are made from a white granular material that is similar to table salt or a very fine, silky, dense white powder. The three types of alumina are hydrated, calcined, and tabular. Each type comes in a variety of grades.
The types of alumina vary according to the amount of soda (Na2O), iron (Fe2O3) and silica (SiO2) they contain as well as their chemical purity and the properties of the powder used in the production process.
Calcined:
To produce calcined alumina, aluminum oxide is heated to 1050o C or 1900o F. The super heating removes all chemicals and water creating a very pure, 99.99% pure, with a 9 on the Mohs hardness scale, which is just below a diamond’s Mohs rating of 10.
Hydrated:
Alumina hydrate, or alumina hydroxide, is used as a glaze because of its ability to stay in suspension in glaze slurries and adhesive qualities.
Tabular:
Tabular alumina is produced by heating aluminum oxide to 1650o C or 3000o F. It has a high heat capacity, excellent thermal temperature, strength, and volume stability. It is formed from sintering balls of calcined alumina,
which are crushed to form a powder. Tabular alumina has high refractory properties, mechanical strength, wear resistance, chemical purity, dielectric properties, and corrosion resistance in acids and alkaline.
Properties of Alumina
High Temperature Ability
Alumina is used in oxidizing and reducing atmospheres up to 1650°C or 2900°F as well as vacuum environments of 2000°C or 3600°F. At 1000o C, it keeps 50% of the tensile strength it has at room temperature. While metals are weakened by high temperatures, alumina ceramics retain their strength when they return to normal temperatures and are unchanged.
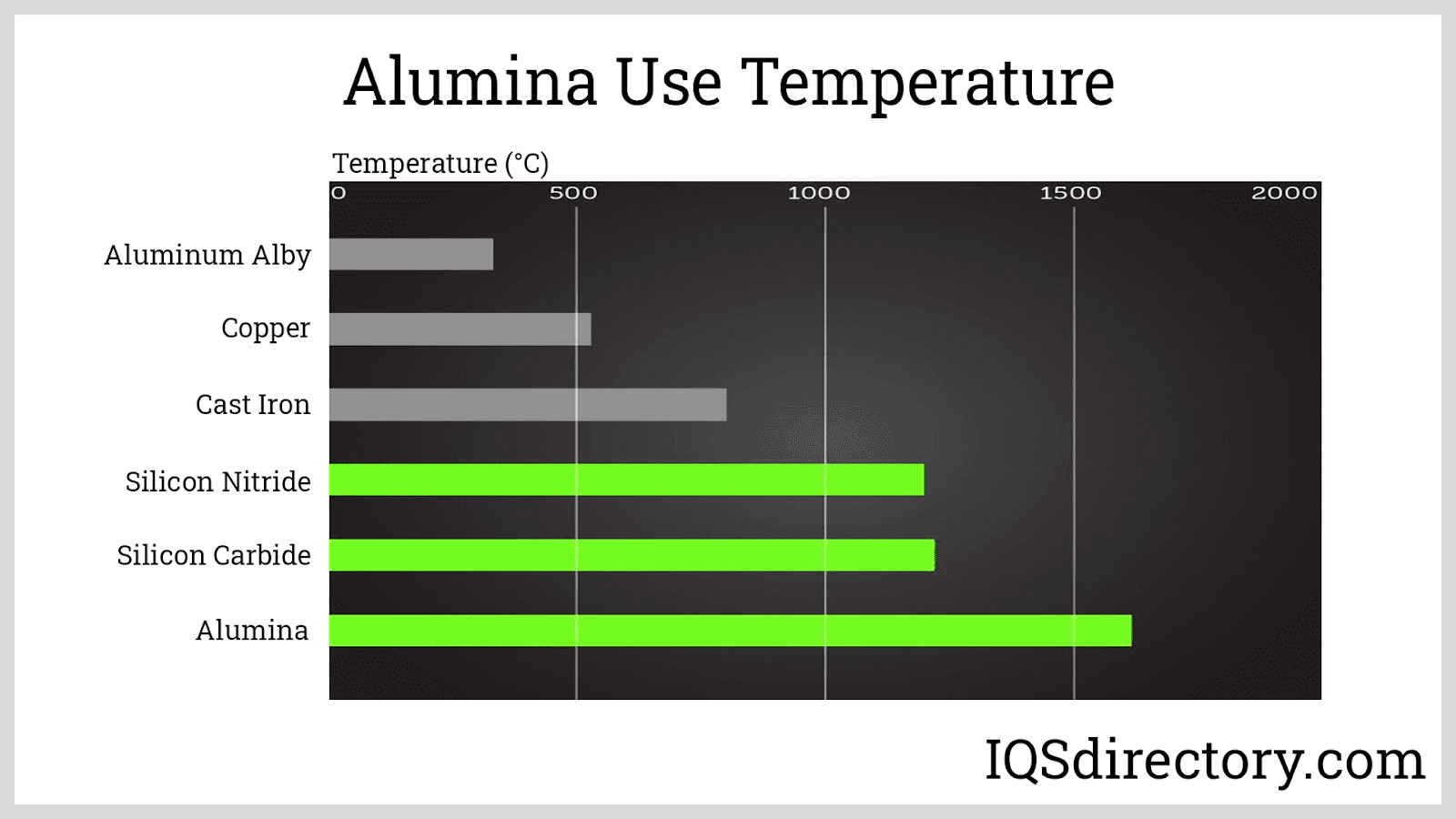
Abrasion Resistant
Abrasion wears down a material by rubbing it away by friction. The resistance to abrasion means a material will maintain its original structure even after mechanical wear. Alumina ceramics are high in abrasion resistance due its hardness.
Chemical Resistance
Alumina is resistant to acids and alkalis at high temperatures because it is inert, not chemically reactive, which makes it resistant to the effects of chemicals such as solvents and salt solutions.
Density
The density of a material is its mass divided by its volume. This is read as grams per cubic centimeter (g/cm3), where grams is mass and cubic centimeters is volume. The volume and density of the material are inversely proportional.
Alumina ceramics are made from fine particles that do not allow for voids in the material. Fewer voids means the material has high volume and density. The density of alumina ceramics varies according to the temperature. For example, at 77 °F (25 °C), its density is 3.965 g/m3 at standard atmospheric pressure.
Manufacturers must grind the powder to a sub-micron (nanometer) level to achieve an after-firing grain size of less than five microns, which produces the fewest voids and creates the best wear surface. Ceramic with a 95% alumina content, after firing, will have a grain size of 30 to 40 microns, large voids, and a high wear rate. In contrast, ceramic with an 87% alumina content, after firing, will have a grain size of three to five microns.
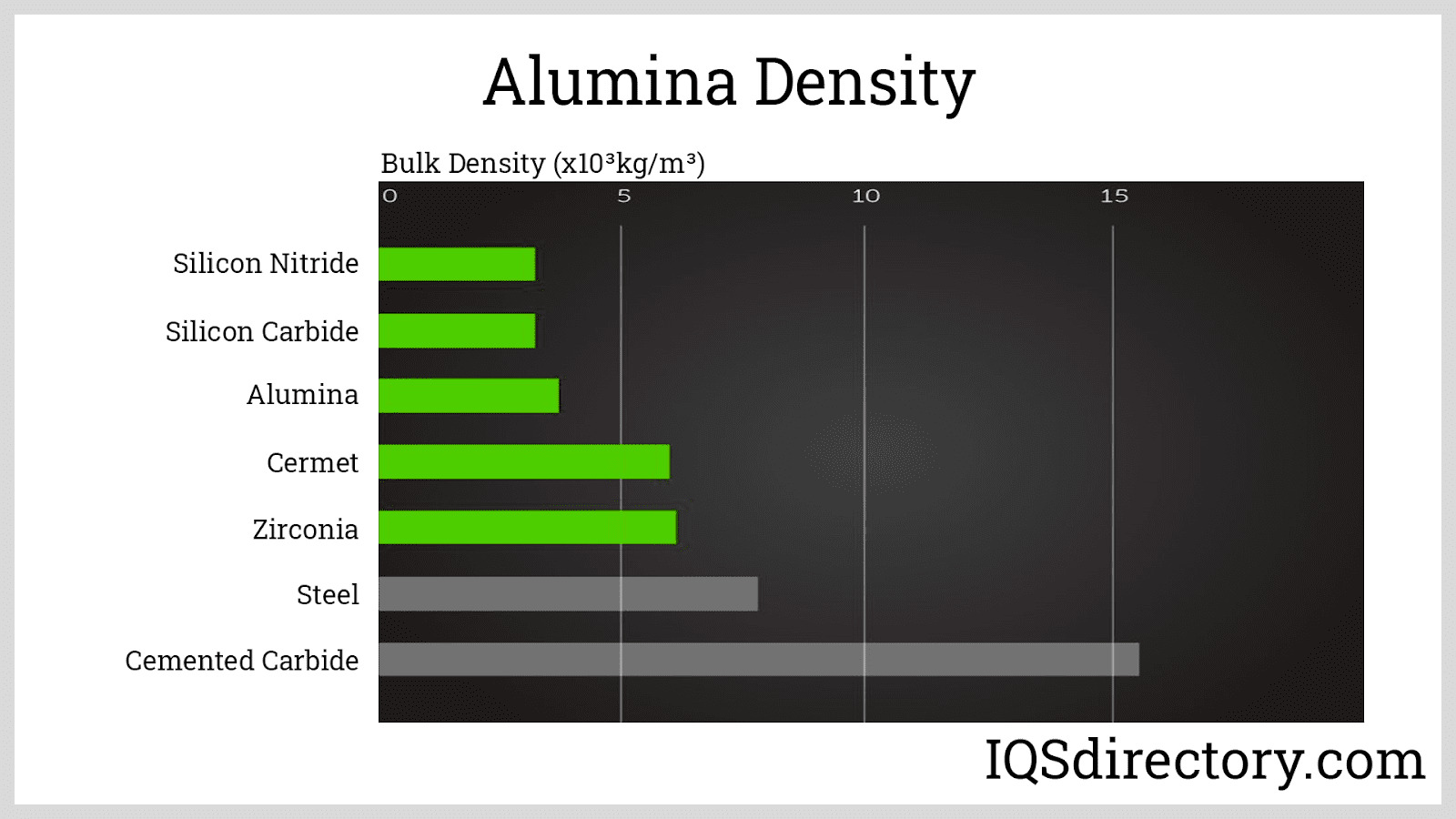
Mechanical
The mechanical properties of a material is determined by its strength, which is the amount of stress and strain it can endure. Alumina has superior strength and hardness that improves with the purity of the different grades.
Thermal
Thermal conductivity is a measure of how well a material spreads heat. As an example, cooking pans must have high thermal conductivity in order to prepare meals. When heat is applied to a material, its atoms begin to rapidly agitate and stretch their bonds. This is referred to as the coefficient of thermal expansion. Alumina ceramics have a low coefficient due to their strong atomic bonds, which makes them more stable in the face of increased temperatures.
The high resistivity of alumina ceramics reduces thermal shock. In addition, its purer forms have even greater resistivity.
Dielectric
Alumina ceramics have exceptional dielectric properties compared to metals or plastic. Dielectric loss is a measurement of the amount of lost energy when a ceramic is subjected to electromagnetic voltage. With high conductivity, electrons move freely when exposed to electromagnetic voltage. The purpose of an insulator is to inhibit the flow of electrons. Alumina ceramics are able to withstand extreme exposure to electrical charges without any dielectric loss. This makes it a perfect insulation material because of its dielectric equality. Electric current is unable to pass through it.
Hardness
Hardness measures the ability of a material to endure mechanical wear and abrasion. Alumina ceramics are harder than steel and tungsten carbide tools. According to Rockwell hardness, alumina ceramics are at HRA80-90, second only to diamonds and above stainless steel.
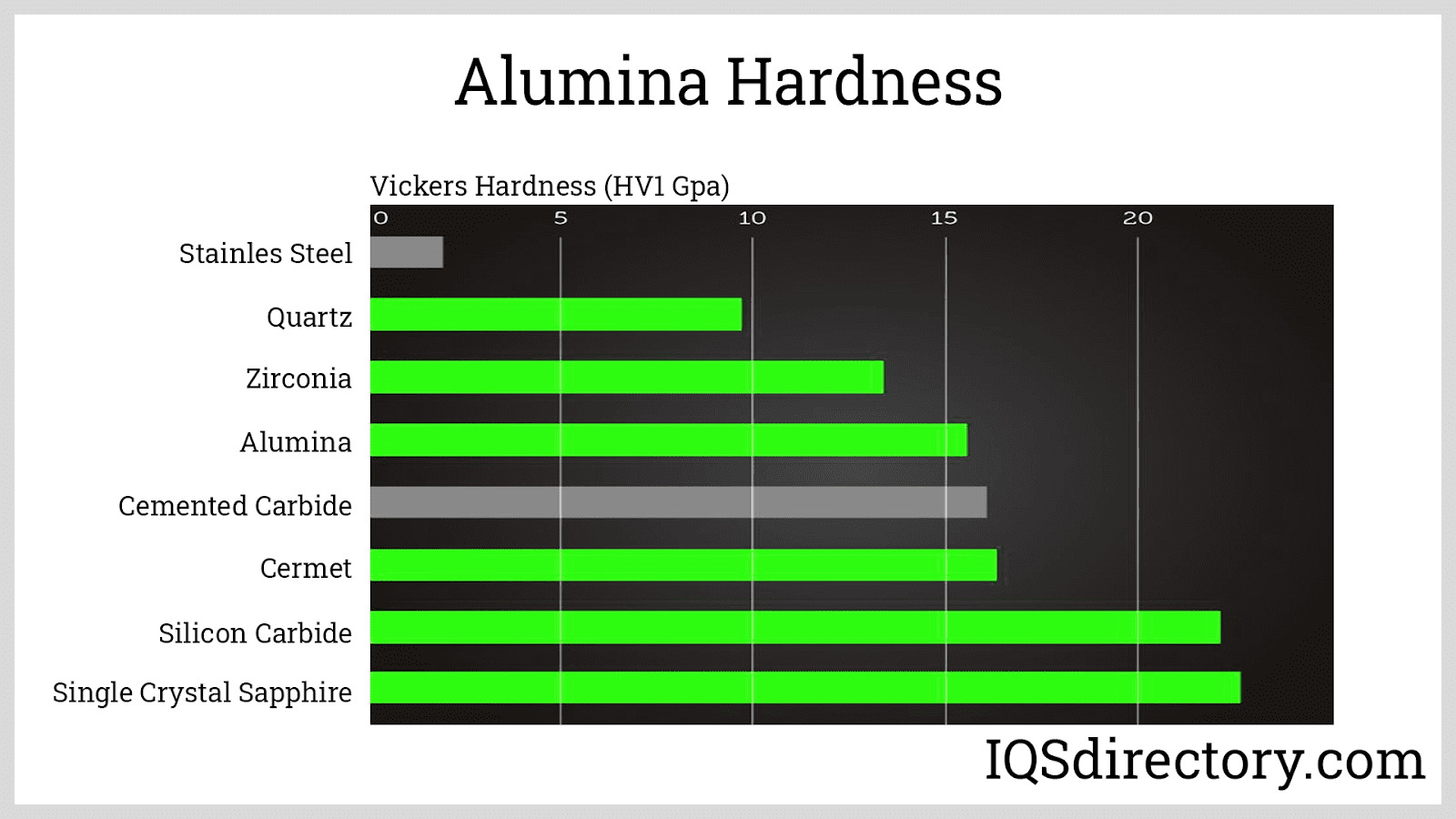
Chapter Three – How are Alumina Ceramics Produced?
The powder material for alumina ceramics comes from the processing of bauxite, which is an aluminum rich clay like material located a few meters below the earth’s crust. The method for manufacturing alumina was discovered in 1887 and is called the Bayer process.
Alumina Ceramic Production
Grinding:
The mined bauxite is taken to a processing plant, where it is ground to extract the aluminum oxide. The composition of the removed aluminum oxide looks like a white powder.
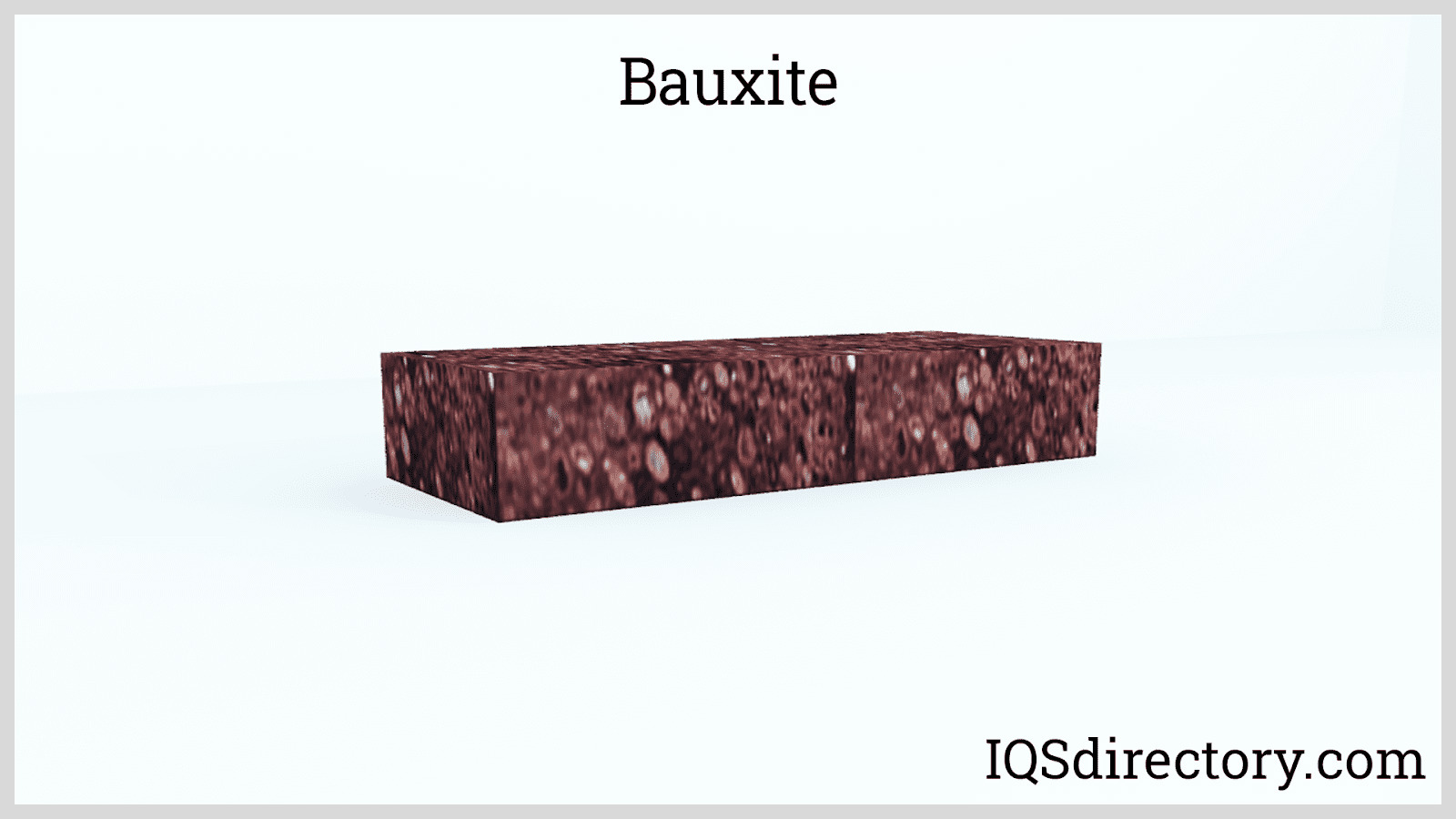
Washing and Drying:
The ground bauxite is washed, dried, and dissolved in a mixture of caustic soda and lime to form a slurry that is heated in a digester to 300o F or 145o C and placed under 50 lbs. of pressure for several hours to dissolve the aluminum compounds.
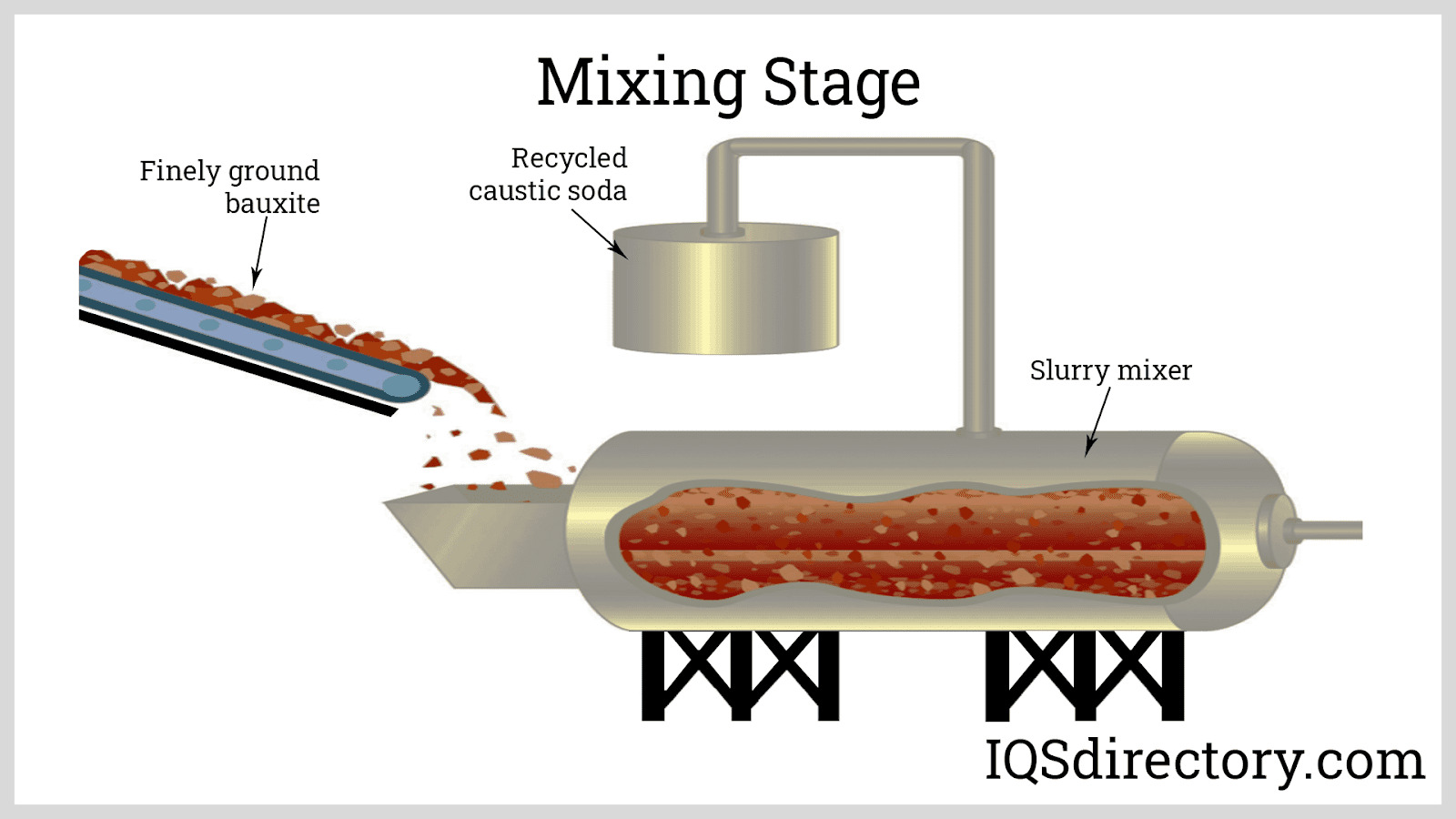
Flash Tanks:
The slurry is pumped through a series of flash tanks to reduce the pressure and heat on the material. The flash tanks cool the material at atmospheric pressure and flash off steam.
Settling Tank:
The impurities in the slurry, like sand, iron, and other elements that do not dissolve, settle to the bottom of the tank. The liquor at the top of the tank moves through a set of filters and is washed to recover the alumina. It is filtered several times before moving on.
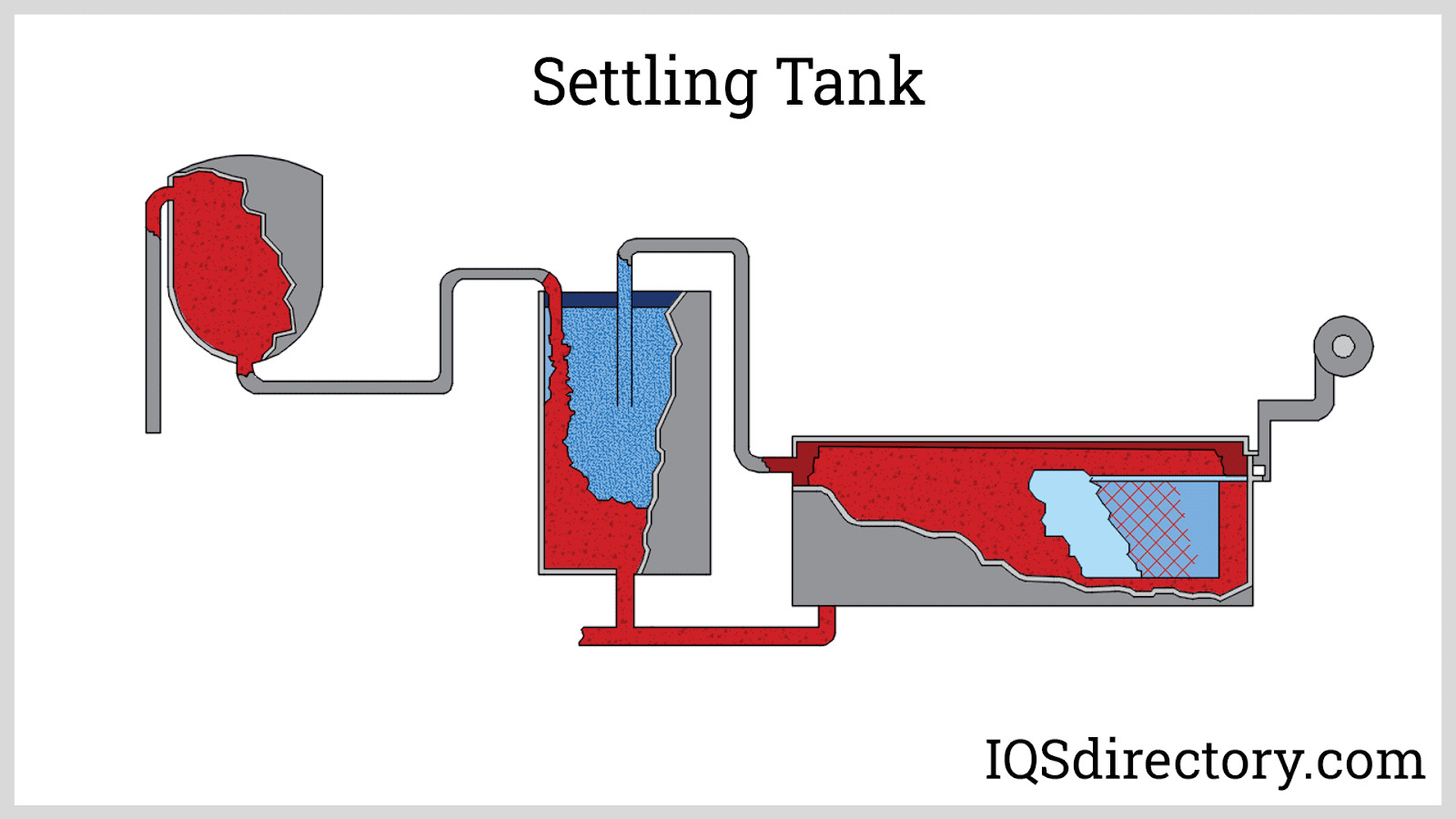
Precipitators:
The filtered clear sodium aluminate is pumped into a series of precipitators. Particles of alumina are added to begin the process. The alumina grows around the seeds causing them to fall to the bottom of the tank to be removed and sent to thickening tanks. The material is filtered again.
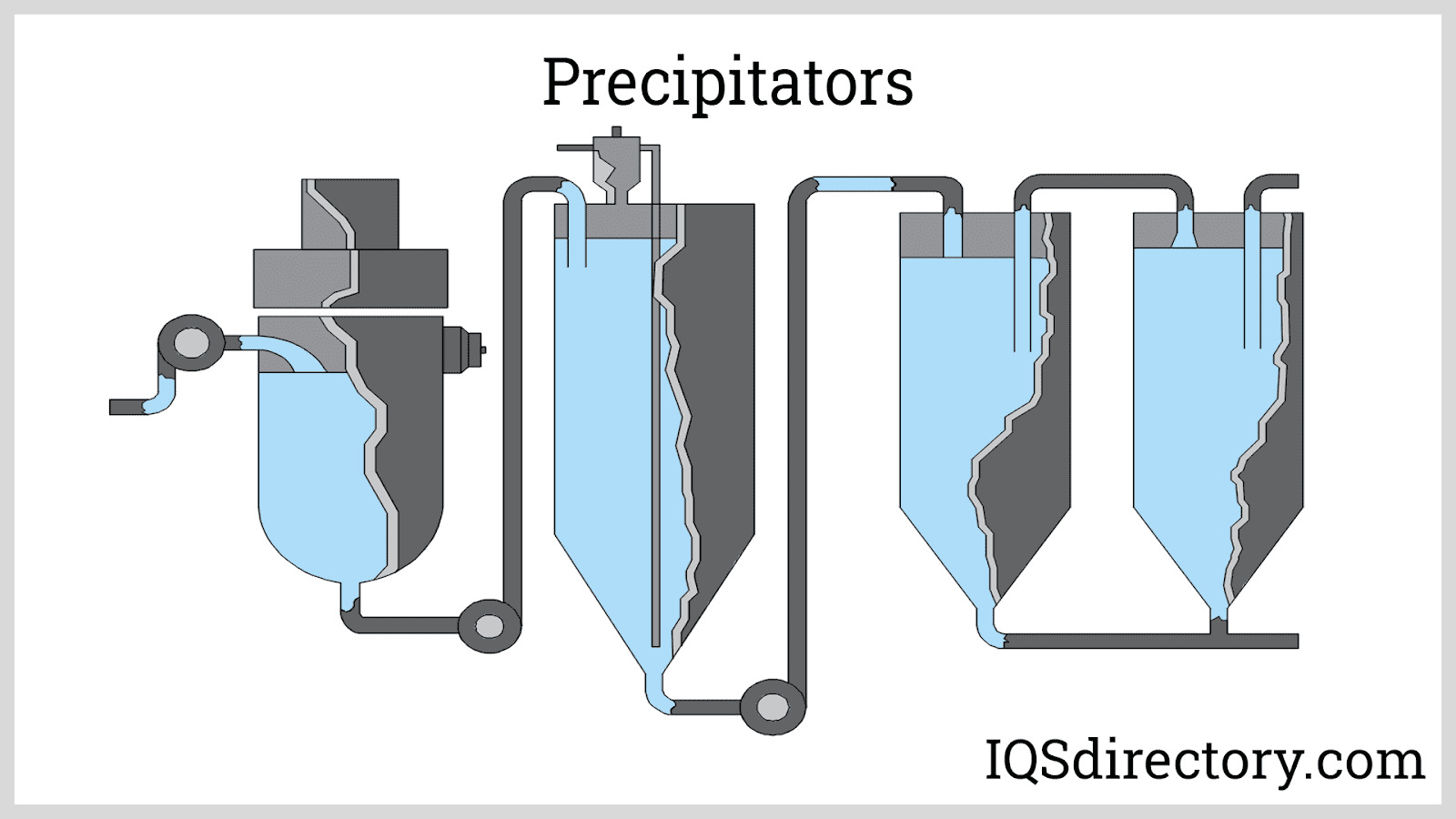
Calcination:
The final step in the extraction of alumina involves a heating process to remove water from the alumina hydrate. It is filtered and washed again to remove impurities and moisture. A conveyor, seen in the diagram, moves the hydrate to calcination, a gas fired kiln on an incline that rotates to ensure even heating.
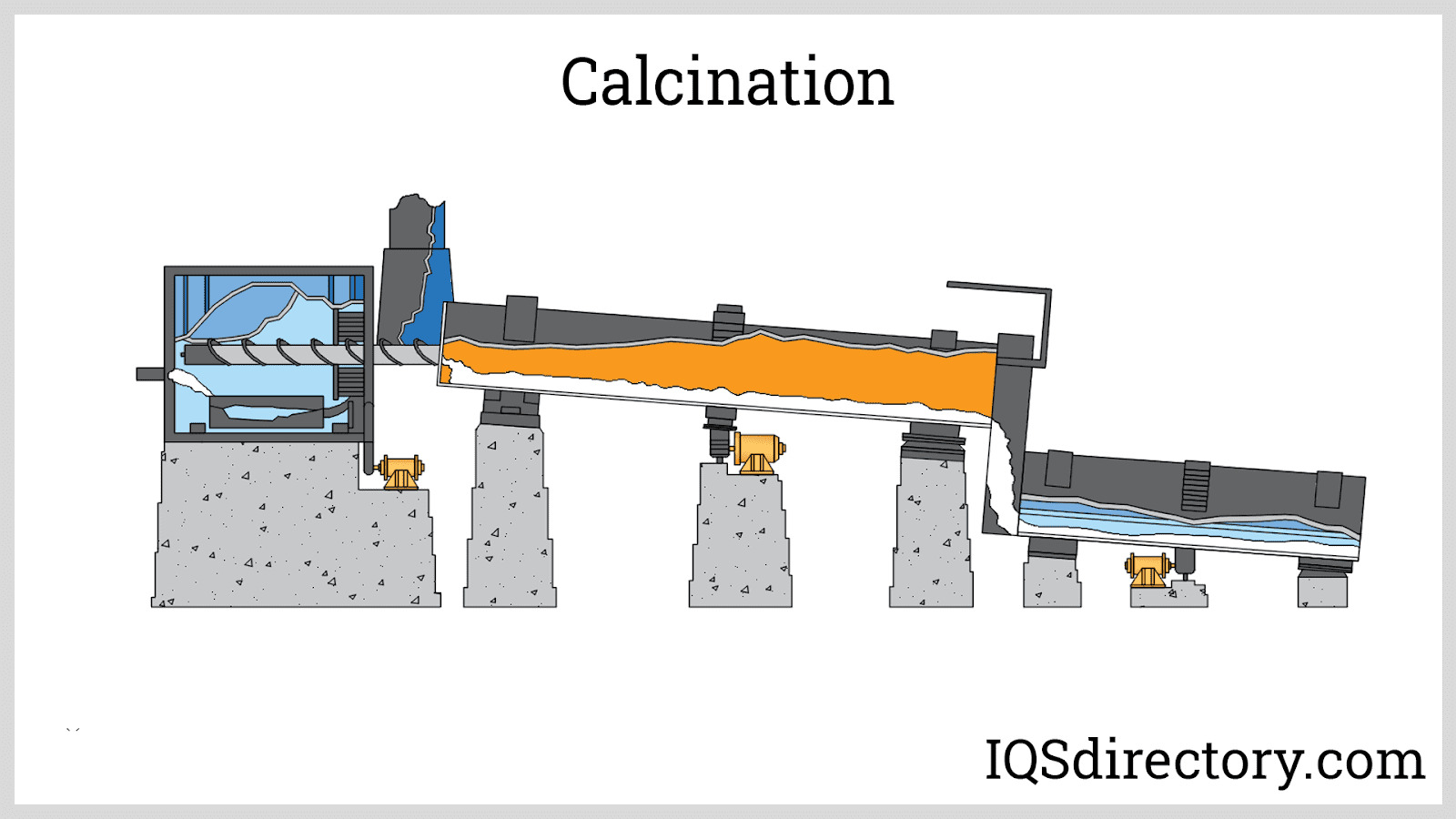
Newer methods of processing use a fluid bed calcining that suspends the alumina particles above a screen of hot air and calcined.
Final Alumina Powder:
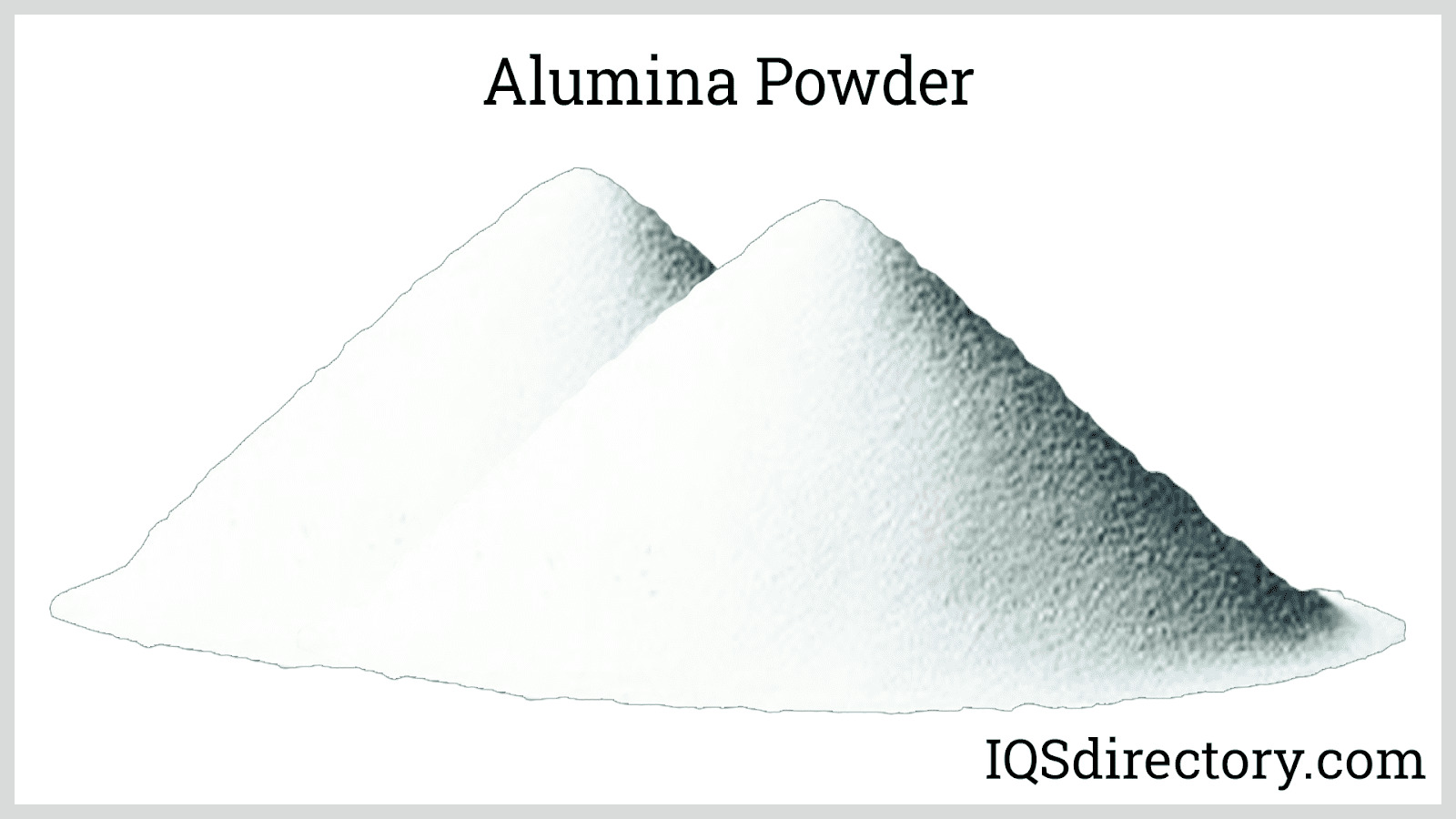
Producing Alumina Ceramics
The powder from refining is mixed with other materials before being put through the forming process. The blend of alumina and other substances determines the grade of the ceramics. Three of the mixing processes are spray dried powder, aqueous slip, and ceramic dough feedstock.
Spray Dried Powder:
Spray drying produces a granulated powder for uniaxial and isostatic pressing. The raw powder is milled in a solvent, such as water. A binder is added before the spraying process, which gives the material strength for pressing.
Aqueous Slip:
With aqueous slip processing, the raw materials are milled together using a ball mill in water with an organic dispersant that produces a concentrated slurry. The slip is placed under high pressure that produces green density parts.
Ceramic Dough Feedstock:
In the ceramic dough feedstock process, water, alumina, a binder, and plasticizer are mixed to produce a clay-like material. The feedstock has to be of high quality to produce the necessary green density for consolidation, which lowers shrinkage during the sintering stage.
Forming Process
Consolidation is the forming of the ceramic part for handling and forming. Four of the many methods for consolidation are extrusion, uniaxial and isostatic pressing, electrophoretic deposition, and slip casting.
Injection Molding:
In the injection molding process, fine powder is mixed with a binder to form the feedstock, which is heated to form a viscous slurry and injected molded to form the green part. The binder is removed to form the brown part, which is densified through sintering.
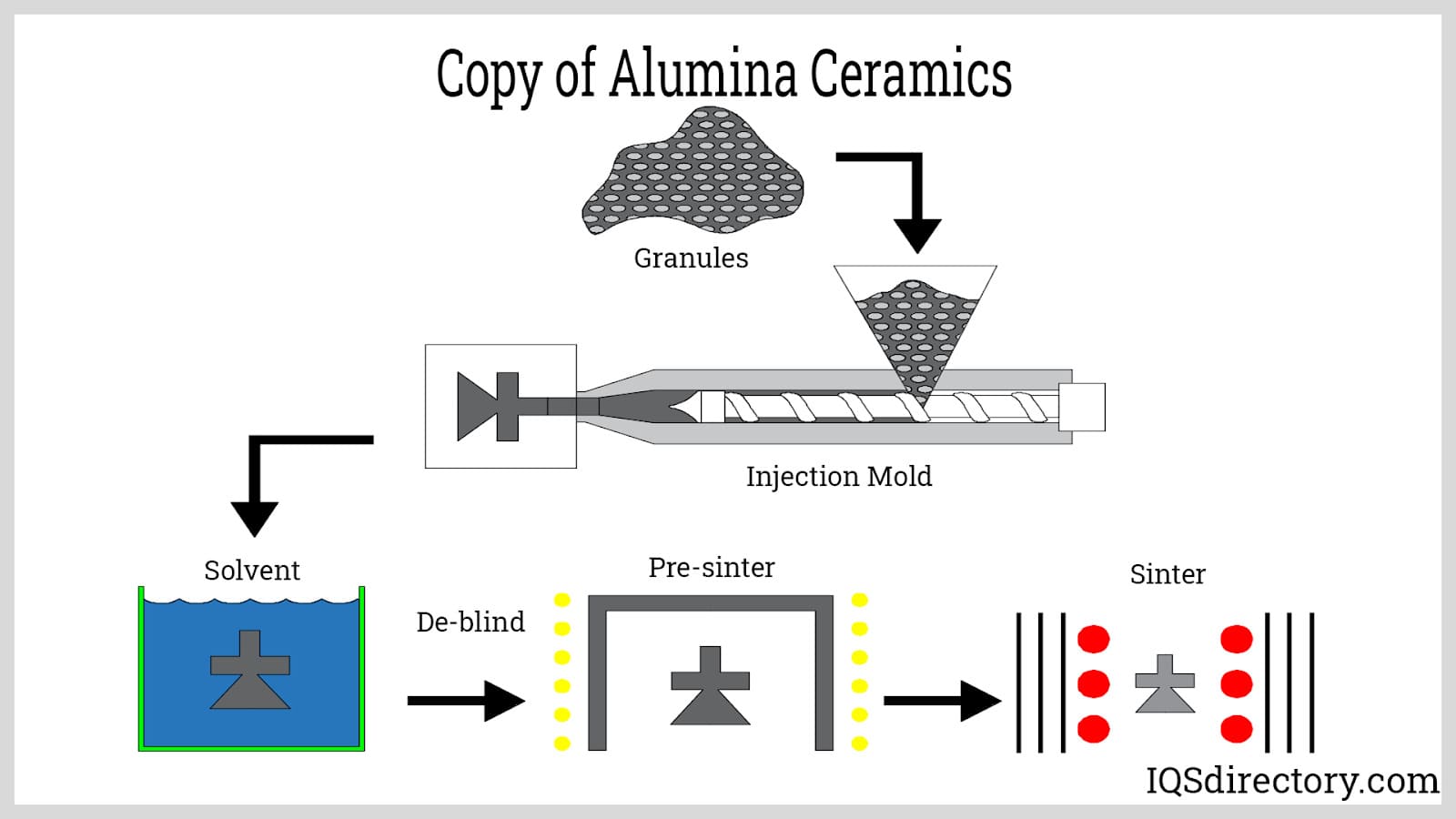
Extrusion:
Extrusion uses dough feedstock that is deformed under pressure. The binders in the mix help the form keep its shape as it dries.
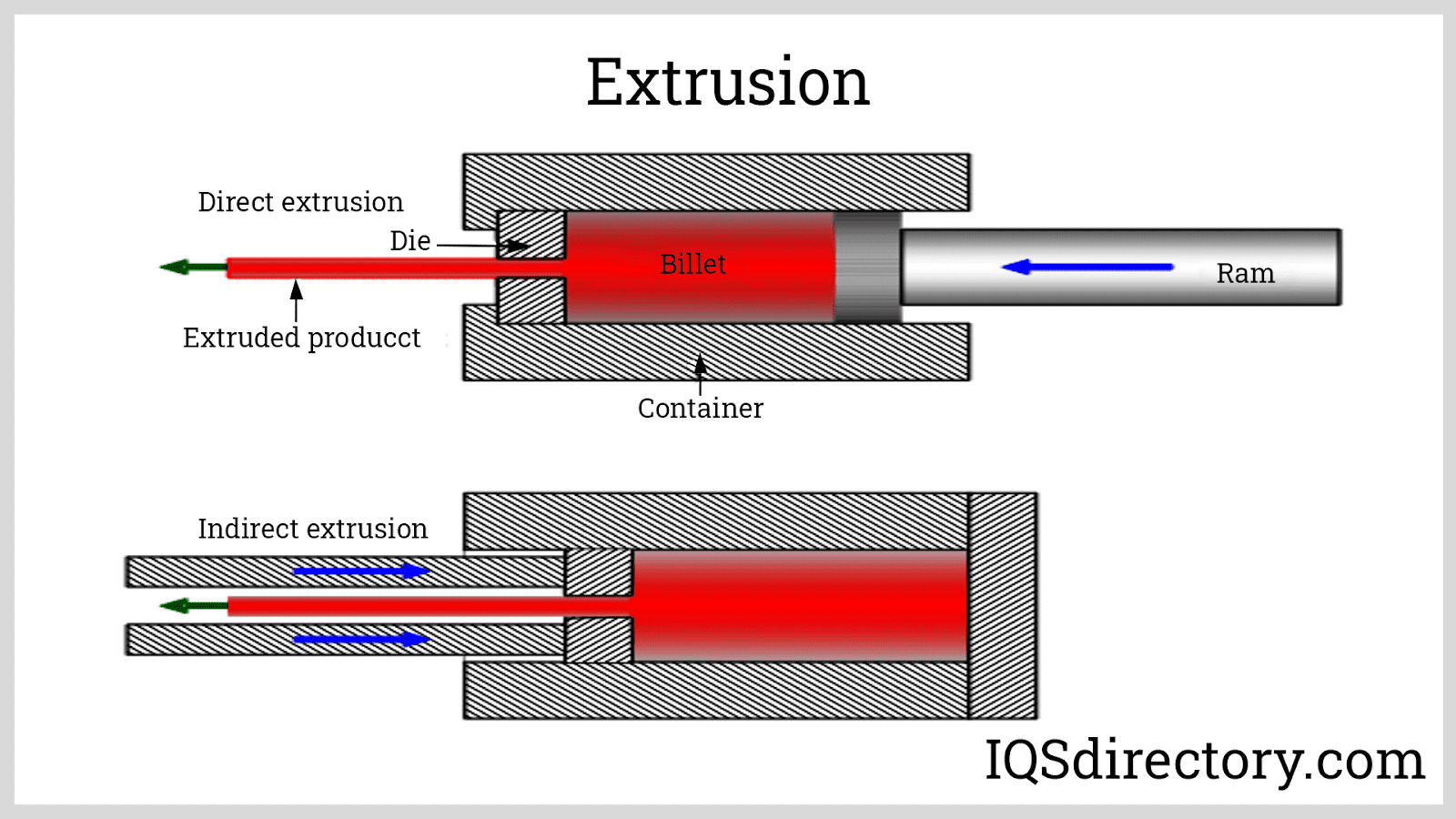
Isostatic pressing:
Isostatic can be wet or dry bag pressing. Sprayed powder is placed in a bag of rubber or polyurethane and placed under isostatic pressure. Wet bag pressing produces simple shapes, while dry bag pressing can produce very complex shapes.
Slip Casting:
Slip casting, or drain casting, uses a fluid aqueous slip that is poured into a mold made of plastic. Water is drained from the mixture leaving a consolidated powder mix on the sides of the mold. As the thickness of the cast increases, the remaining slip is drained. With pressure casting, pressure is applied to the slip creating thicker walled and more solid parts. A simplified version of slip casting can be seen in the diagram below.
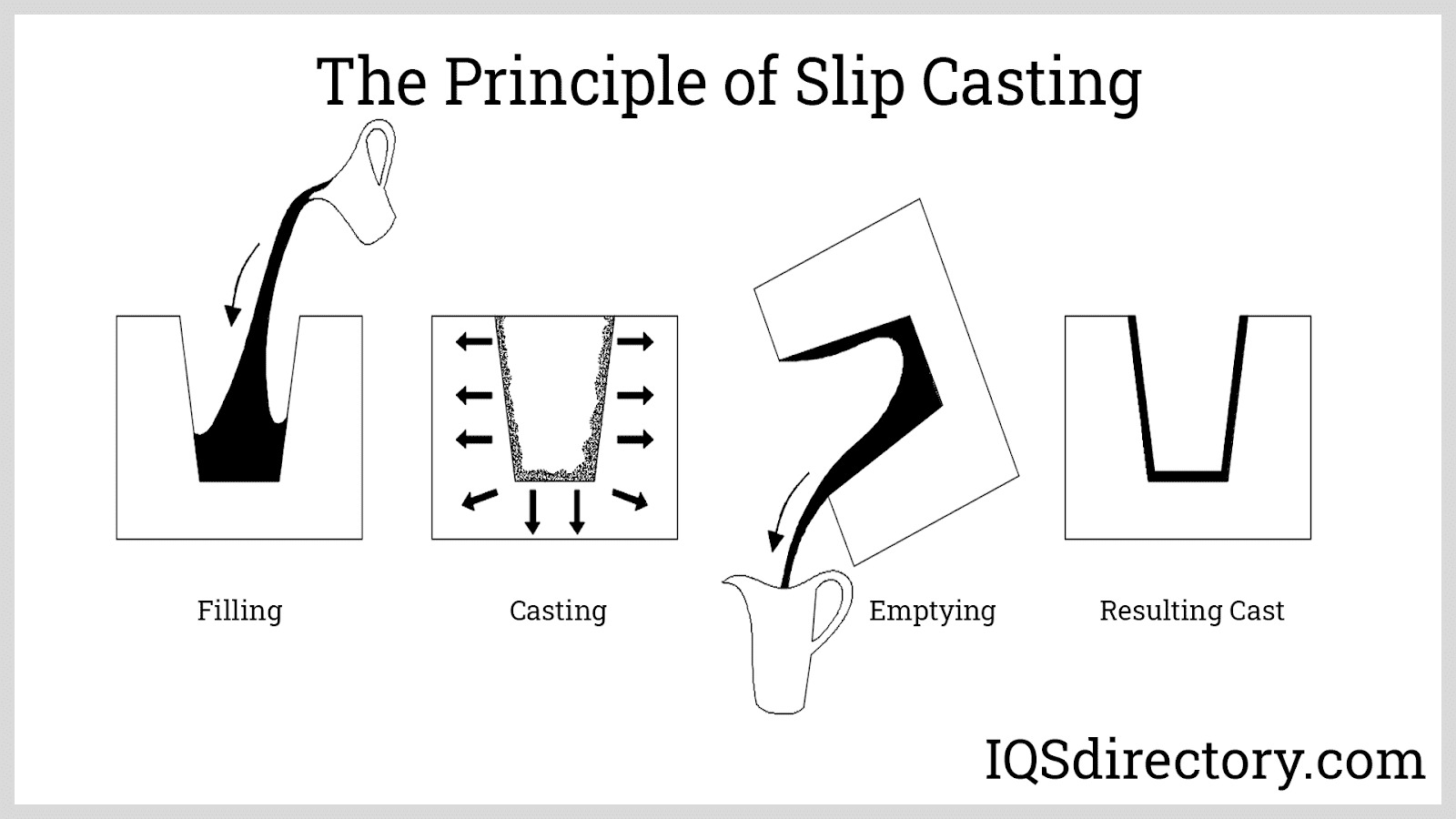
Uniaxial Pressing:
Uniaxial pressing is a compacting of alumina powder by applying pressure in a single axial direction using a piston, punch, or plunger. Presses for uniaxial pressing can be hydraulic or mechanical that have a top punch, bottom punch, and die.
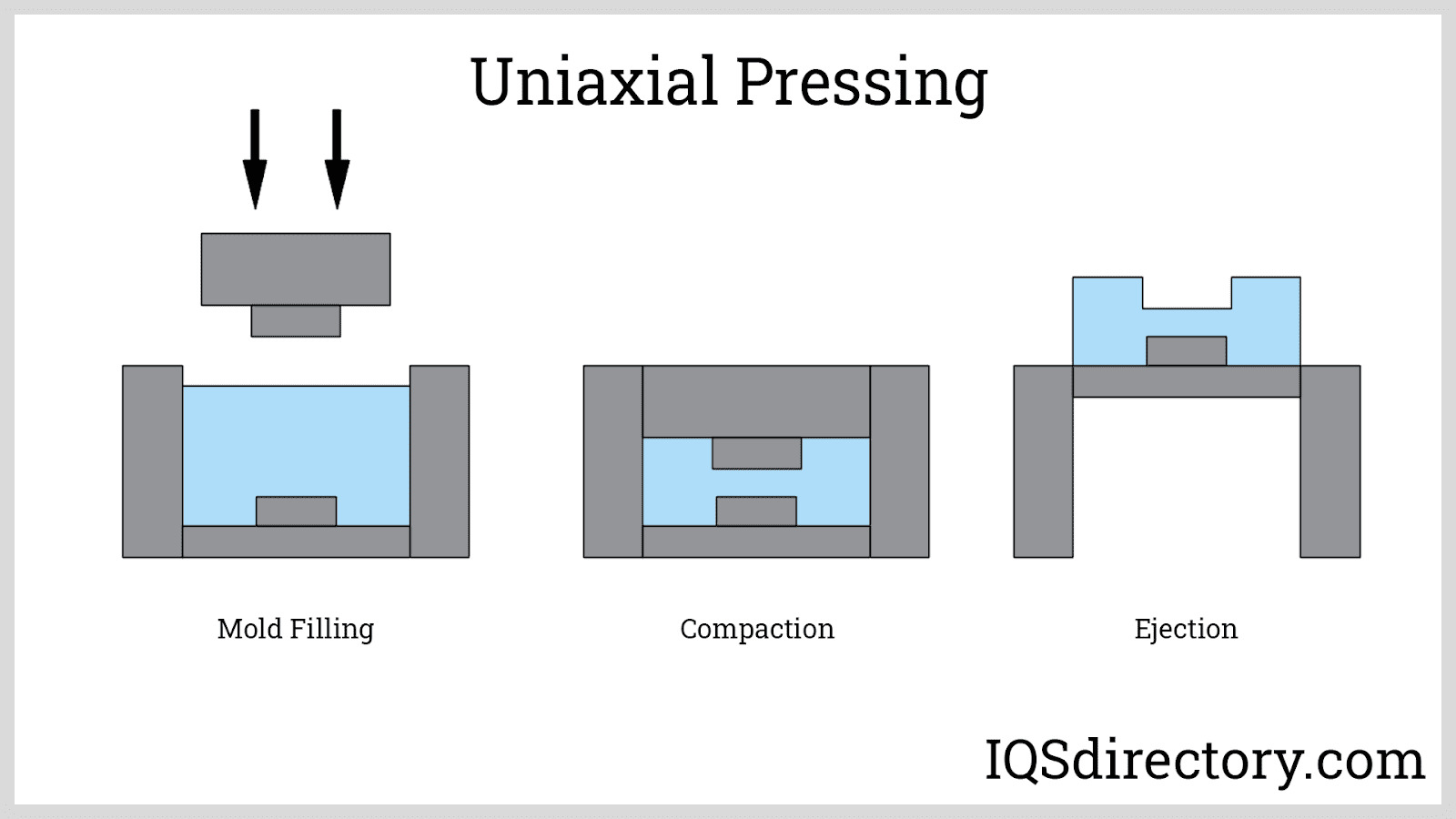
Electrophoretic deposition (EPD):
EPD used for several industrial coating and painting processes. For ceramic production, an electrostatic charge consolidates ceramic particles from suspension and deposits them on the surface of a mold. Once the necessary thickness is achieved, the mold is removed from the slip container or the slip is poured off.
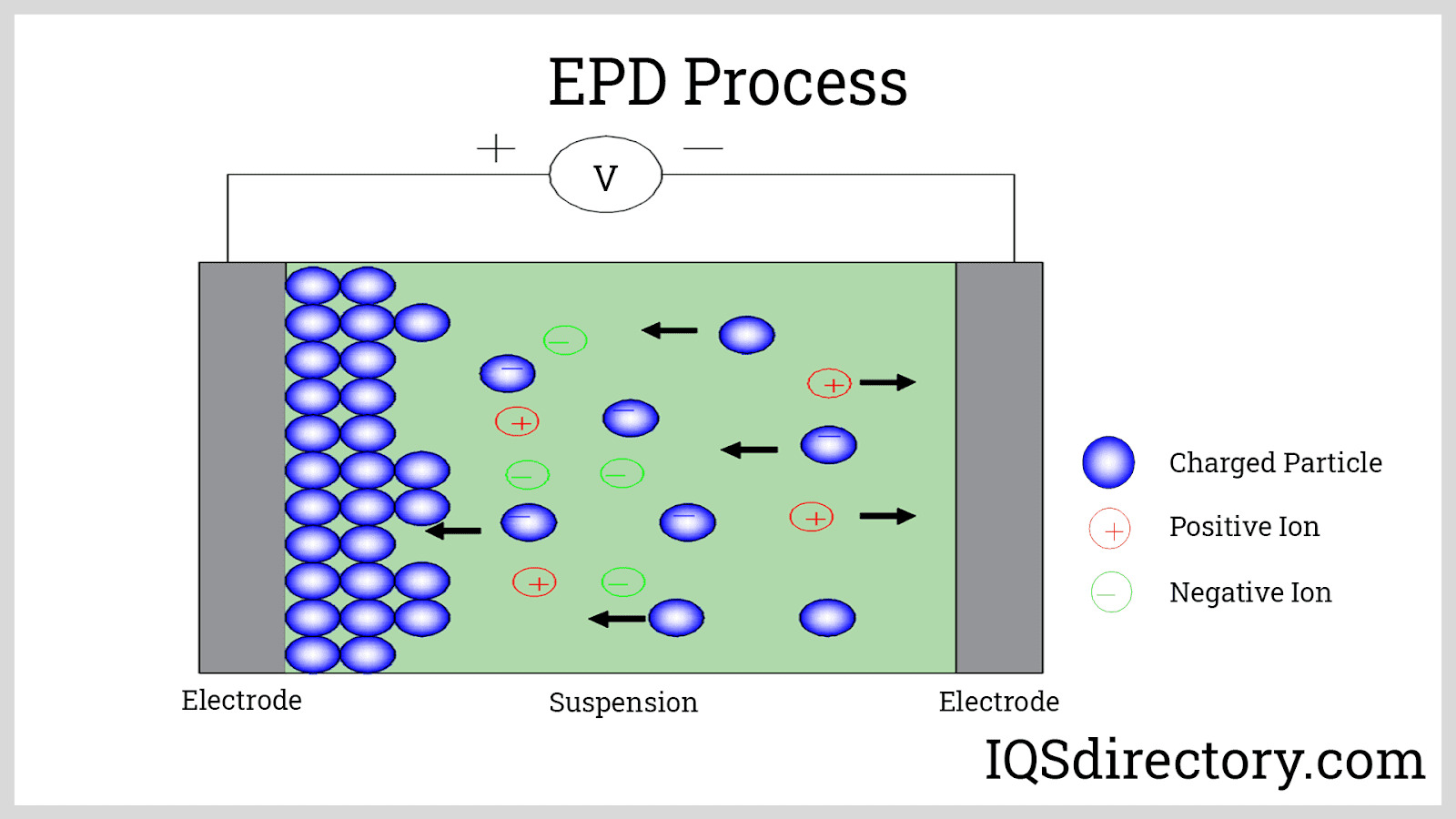
Finishing Processes
Sintering:
During sintering, the consolidated green ceramic part is fired to give it density. At the high temperatures of sintering, particle rearrangement, grain growth, and pore elimination take place. For alumina ceramics, this is known as solid state sintering. One of the outcomes of sintering is shrinkage from up to 20% to 25%. However, the uniformity of the shrinkage and the quality of the final part depends on the density of the green material.
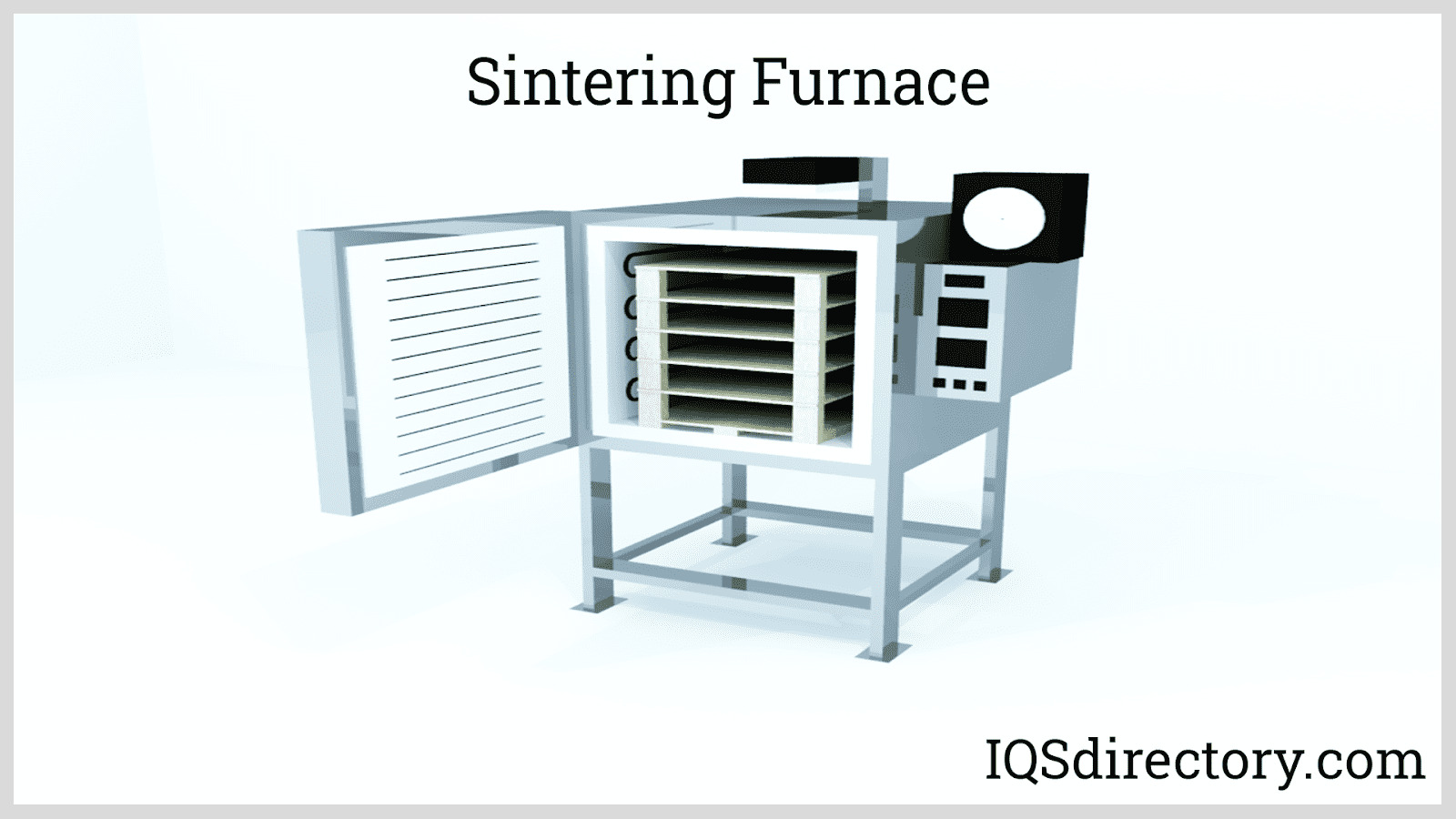
Green Machining:
Alumina can be machined in green or fully dense states. In the green form, it can be easily shaped into complex geometries. However, though it is easy to shape alumina in its green form, it will shrink by 20% during sintering, changing the dimensions of the piece. Therefore, green-machined alumina will not hold its tolerances during sintering. In order for alumina to maintain its tolerances, it needs to be machined after sintering with a diamond-coated wheel.
Diamond Grinding:
Diamond grinding is done after sintering to match tight tolerances, improve the surface finish, and remove any flaws. Diamond processes include grinding, cutting, honing, lapping, and polishing. The diamond tooling is necessary due to the hardness of alumina ceramics.
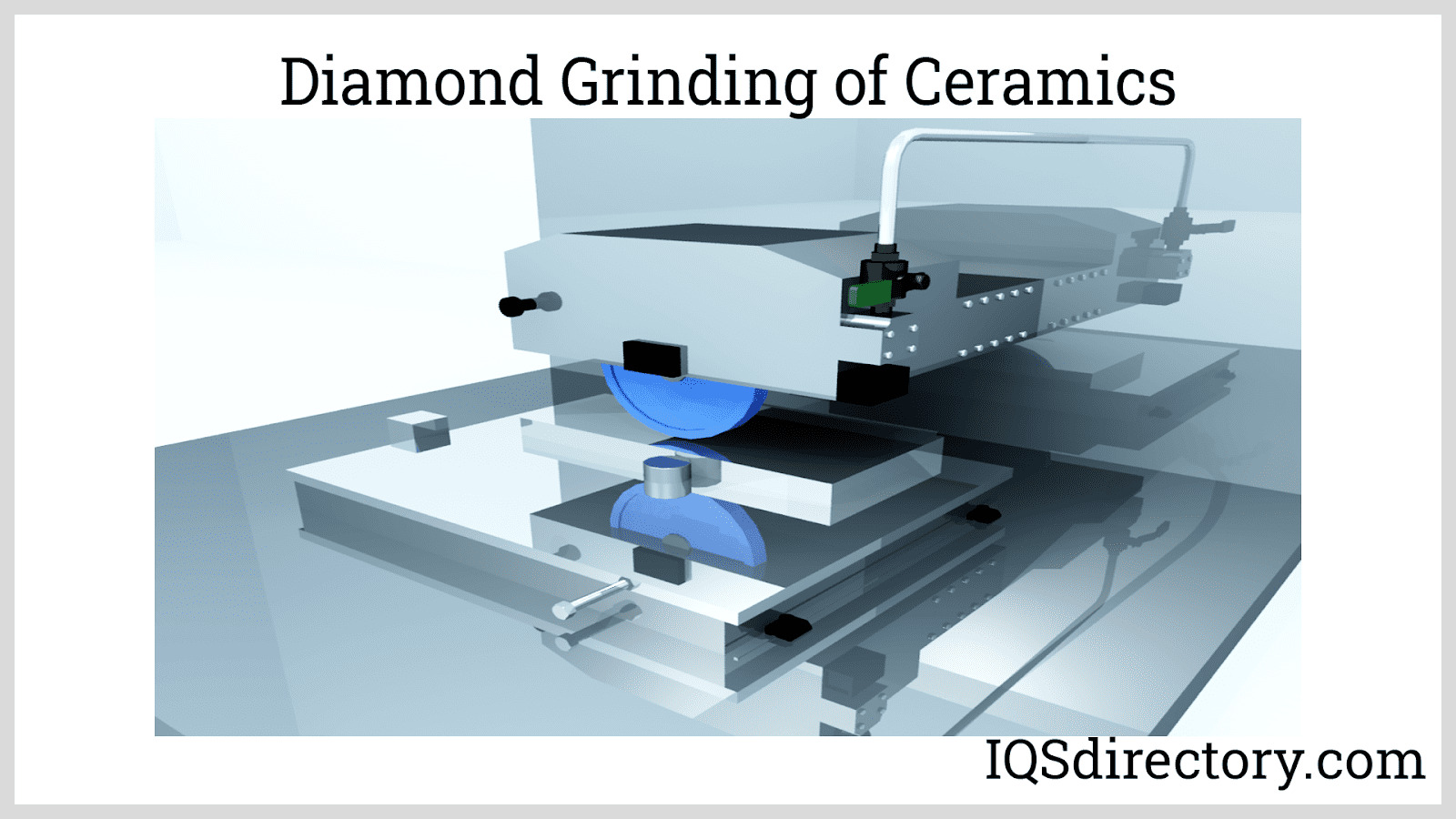
Chapter Four - Top Alumina Ceramics Machines
The goal of alumina ceramics is to provide pieces featuring high-temperature resistance, exceptional hardness, electrical resistance, and chemical inertness for various applications. Luckily, there are many manufacturers of machines that have essentially perfected their creation. Below, we feature five brands of machines used to produce alumina ceramics in the United States and Canada, along with specific models and their unique features:
CeraNova Corporation:
Model: High-Speed Ceramics Milling Machine
Features: The High-Speed Ceramics Milling Machine by CeraNova Corporation is designed specifically for the precision milling of alumina ceramics. It utilizes advanced cutting technology to achieve high material removal rates while maintaining excellent surface finish. The machine offers high-speed spindle options, multiple-axis control, and specialized tooling for efficient and accurate ceramic machining.
CoorsTek:
Model: CeraSurf™ Ceramic Grinding Media
Features: CoorsTek offers a range of ceramic grinding media, including alumina-based CeraSurf™. These grinding media are designed for various applications, such as ball milling and attritor milling. CeraSurf™ ceramic grinding media provide high wear resistance, chemical inertness, and uniform particle size distribution, resulting in improved grinding efficiency and product quality.
Sacmi USA Group:
Model: PH Series Presses
Features: The PH Series Presses by Sacmi USA Group are hydraulic presses specifically designed for the production of alumina ceramics. These presses offer precise control over pressure, speed, and stroke, allowing for the formation of complex shapes with high density. These machines feature a user-friendly interface, advanced automation options, and the ability to integrate with downstream processes.
Harper International:
Model: Pusher Furnaces
Features: Harper International manufactures advanced pusher furnaces used for sintering alumina ceramics. These furnaces provide high-temperature, controlled atmospheres necessary for the sintering process. They offer precise temperature control, uniform heating profiles, and adjustable residence times. Harper's pusher furnaces are designed for high throughput and can accommodate various ceramic shapes and sizes.
LECO Corporation:
Model: AMH43 Moisture Determination Analyzer
Features: The AMH43 Moisture Determination Analyzer by LECO Corporation is specifically designed for the analysis of moisture in alumina ceramics and other materials. It utilizes a precision balance, high-temperature drying, and advanced software algorithms to accurately determine moisture content. The analyzer offers rapid analysis, easy operation, and customizable test parameters.
Please note that the availability and specific models may vary over time, so it's always recommended to check with the respective manufacturers for the latest product offerings.
Chapter Five – Alumina Ceramic Products
Alumina is a major engineering material that has excellent mechanical and electrical properties, which makes it applicable for a wide range of uses. A few of its uses are listed below.
Alumina Ceramic Products
Insulation:
One of the main uses of alumina ceramics is as an insulation material due to its dielectric and thermal shock properties. High frequency applications use extremely pure and dense alumina that has been fired at 1600o C. Television and satellite transmitter tubes, microwave generators, and lasers depend on the strength and durability of alumina ceramics for insulation.
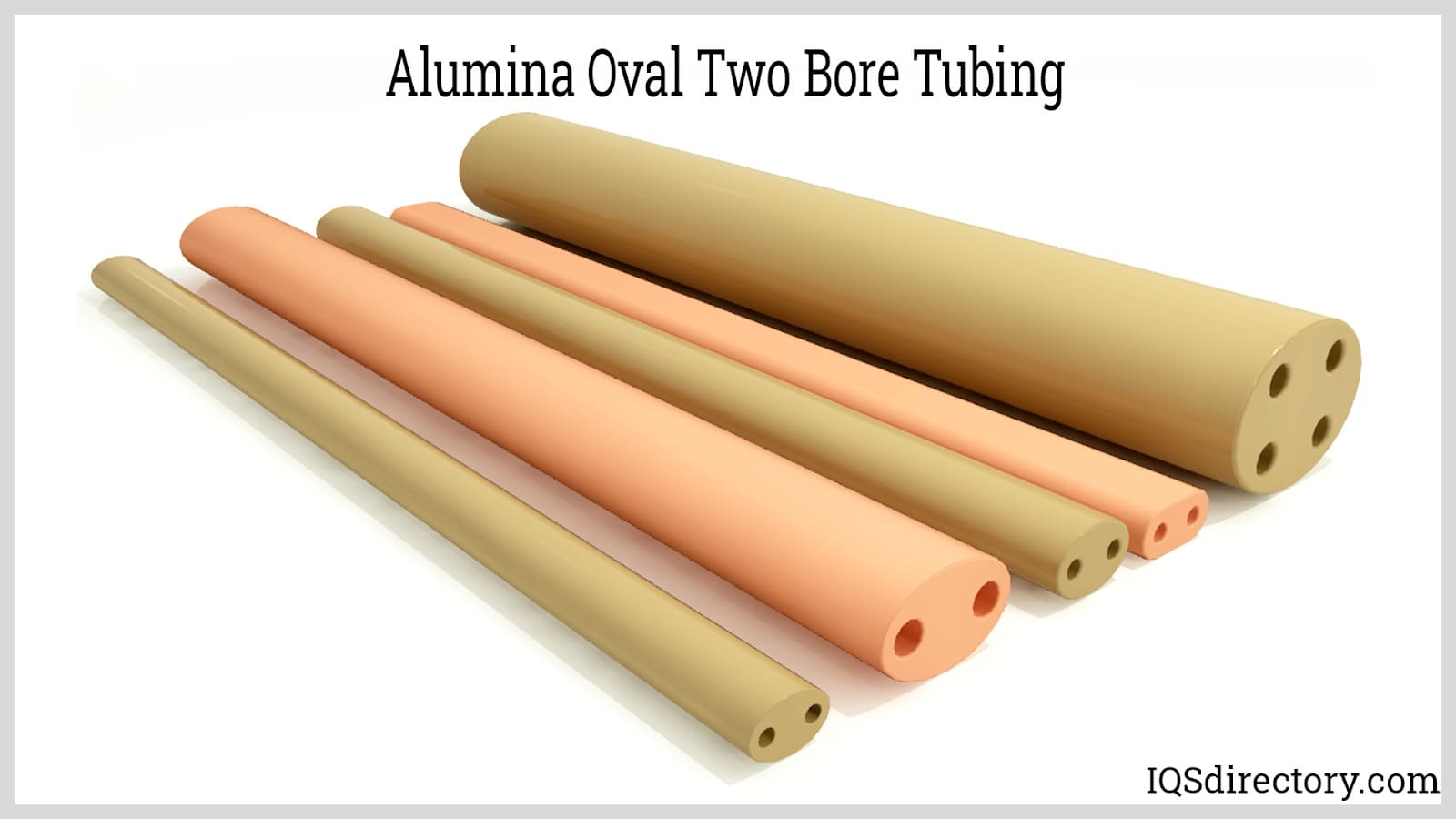
Labware:
Alumina ceramic labware is used for laboratory applications with high-temperature conditions that need to be contamination free. The chemical and corrosion resistance, high hardness, strength, durability, and wear resistance of alumina ceramics makes it a perfect solution for lab applications.
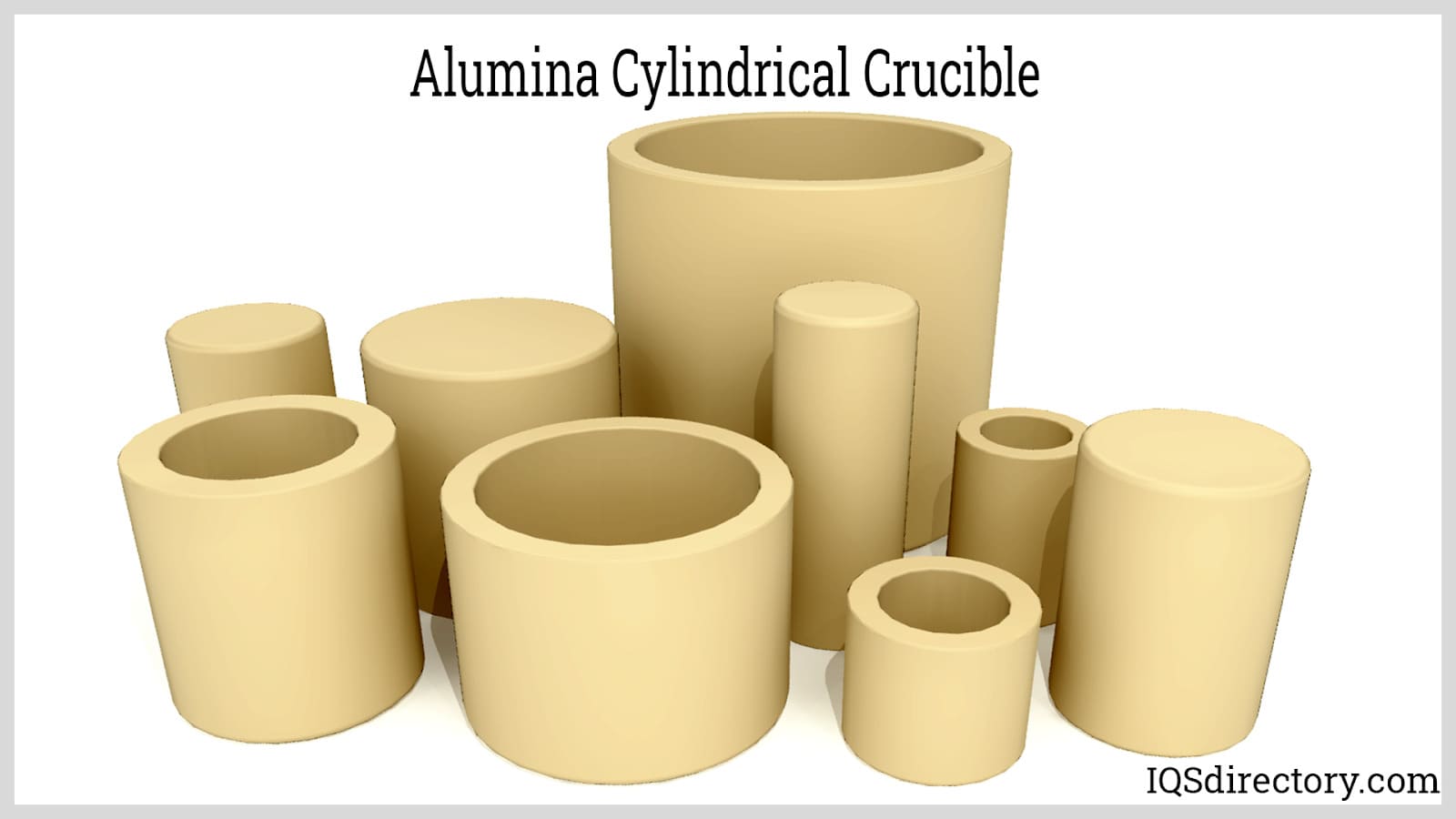
Electronics:
Alumina ceramics are used in the electronics industry for interconnectors, resistors, and capacitors. It is an economical and durable material for substrates for hybrid integrated circuits, surface mount devices, and sensors.
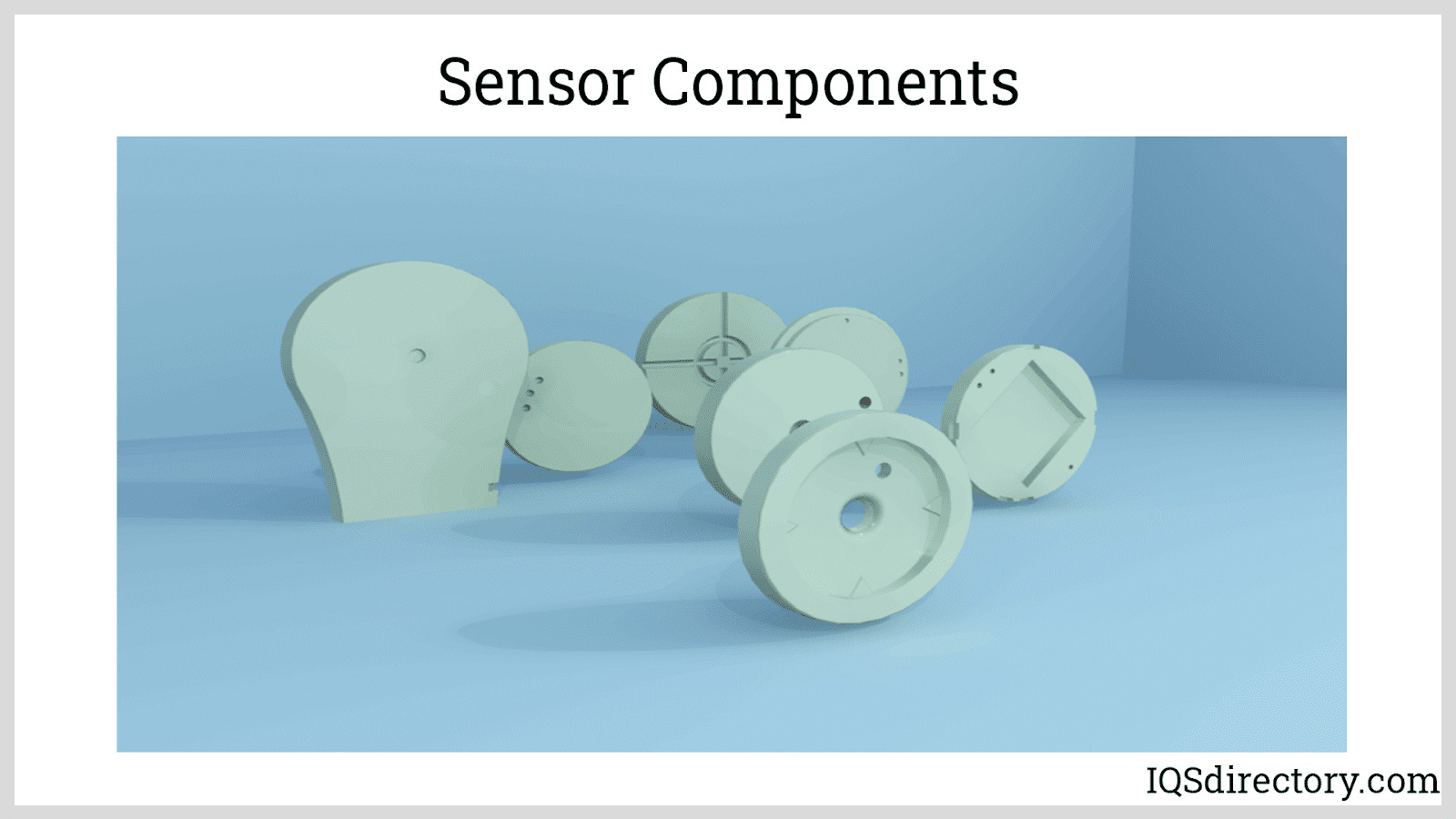
Cutting Tools:
Alumina ceramic cutting tools exhibit strength and thermal conductivity. Though alumina cutting tools were once very expensive, the material is now engineered with the use of composites to be cost-effective and are manufactured by sintering and die pressing. These composites are used as a substitute material for abrasive and cutting tools, extrusions, nozzles, friction parts in piston engines, and machinery when wear resistance is a concern. In addition, alumina ceramics are uniquely used in Olympic ice skaters’ blades.
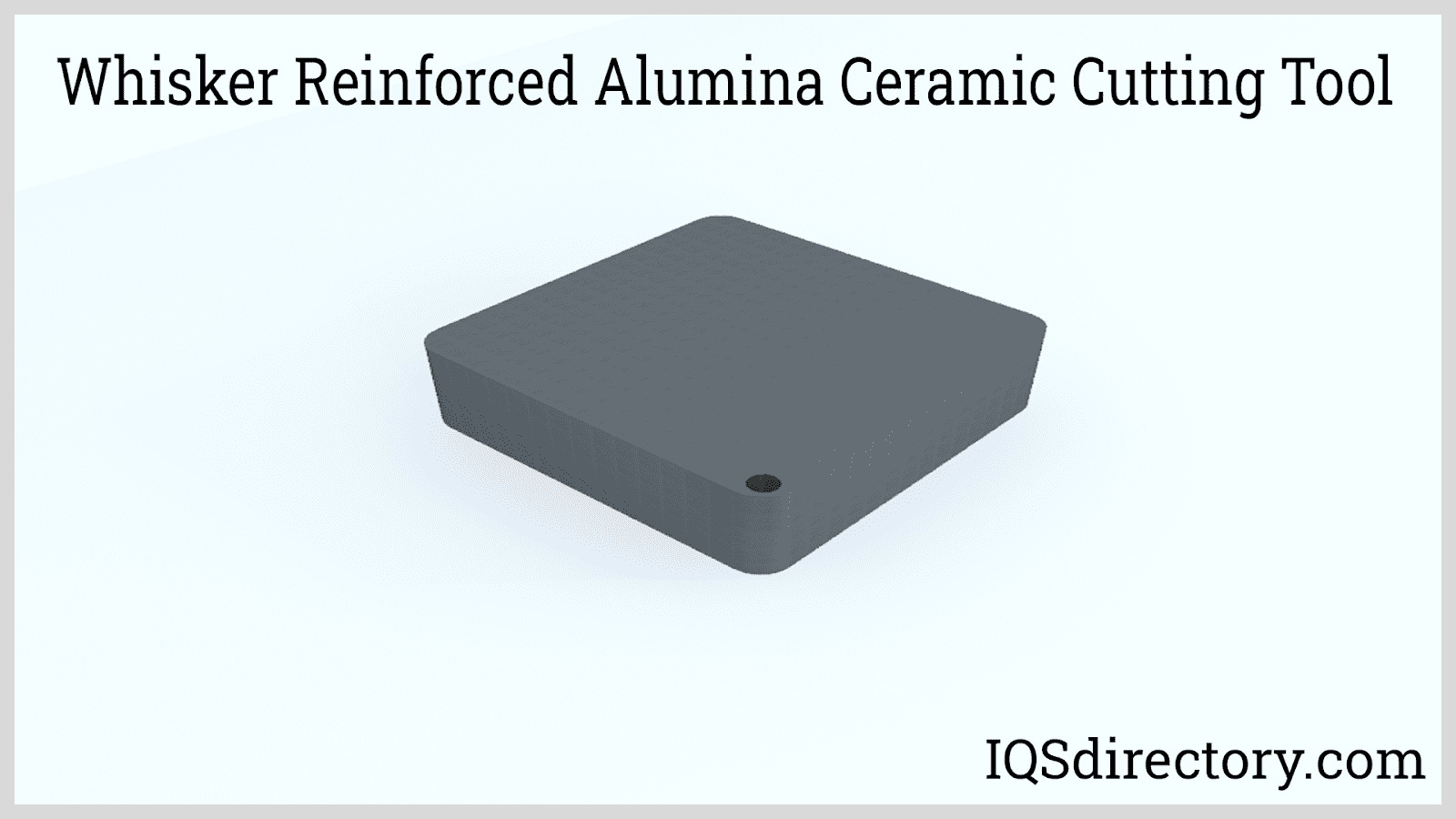
Military Use:
Alumina ceramic is used in ballistics due to its high shock resistance, making it ideal for body armor in tanks, helicopters, and bulletproof jackets. The use of alumina ceramics in armor is to withstand the initial impact of a projectile. It is the first line of defense and protection. Once the alumina ceramic has withstood the impact of a projectile, a second layer of material removes the kinetic energy of a projectile making it inert.
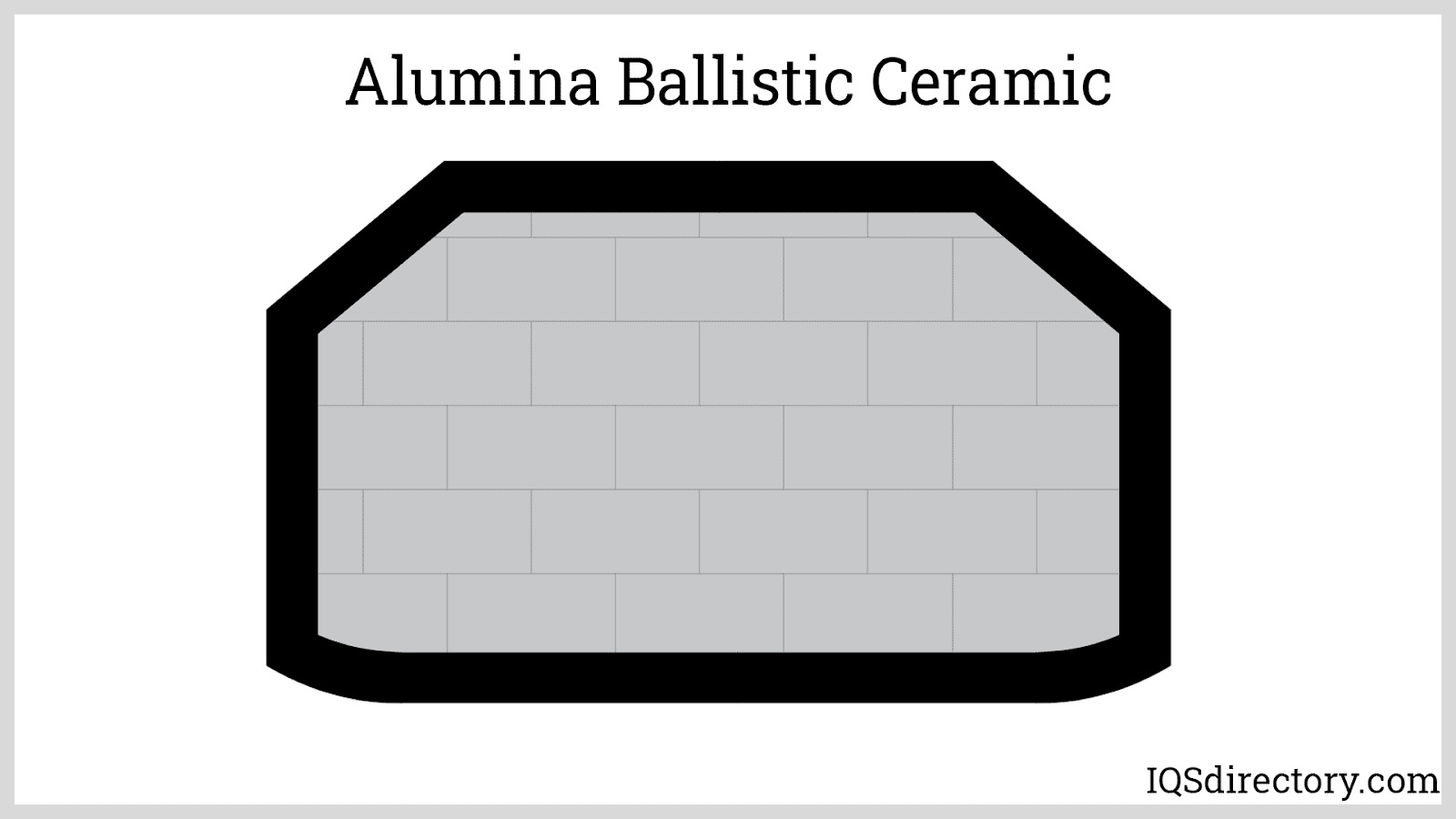
Biomedical Material:
Since alumina ceramics are inert, they are insoluble in chemical reagents, have wear resistance, and can have a highly polished finish, which makes them useful as biomaterial. Consequently, alumina ceramics are used for artificial joints, bone spacers, cochlear implants, and teeth implants. Tubes and scientific products are also made from alumina ceramics. The positive properties of alumina ceramics makes it an ideal material for use in replacing body parts.
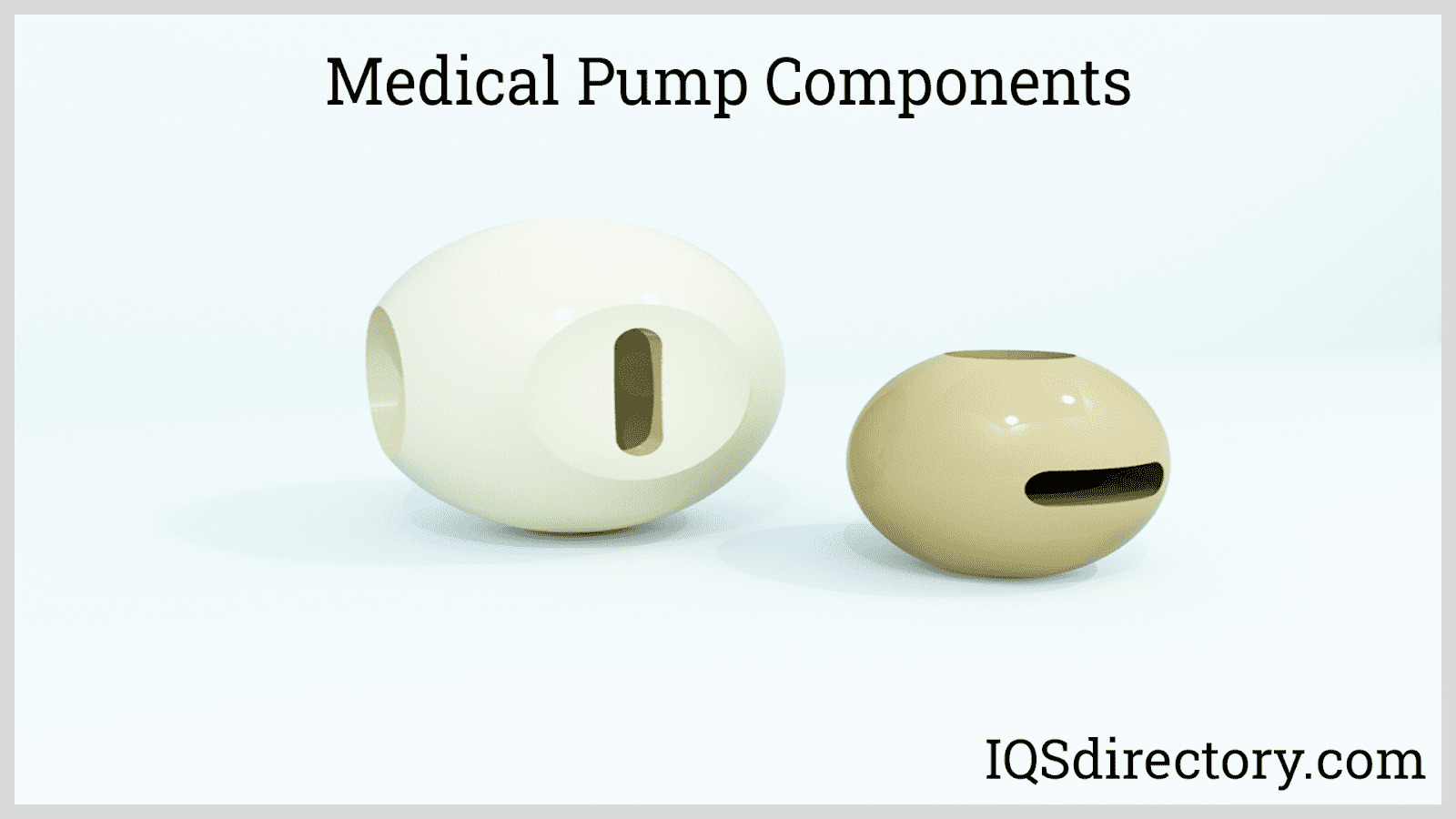
Ceramic Sheets:
There are many ways to use alumina ceramic sheets due to their ability to withstand extreme temperatures. 99% alumina content sheets are suitable for use in vacuum applications. In addition, their machinability allows them to be shaped and placed in harsh environments, including ones with high humidity, since the sheets are unaffected by water.
Since alumina ceramic sheets can withstand temperatures up to 2600 °F (1426 °C), the sheets are often used to make gaskets for furnaces and boilers and can be easily shaped using any form of cutting tool. The consistency and strength of alumina ceramic sheets varies depending on the percentage of alumina content. Thicknesses range from 0.01 in (0.0254 cm) up to 0.5 in (1.27 cm) and are available in various lengths and widths. These lengths and widths are limited by the size of the ovens available to finish them.
Chapter Six – Types and Grades of Alumina Ceramic Material
The grades and types of alumina ceramics is determined by the percentage of alumina the material contains, which can vary from 70% to 99.9%. The percentage of alumina fluctuates according to the amount of other elements that are added to the mixture.
Types of Alumina Ceramics Material
92% Alumina:
features electrical properties, mechanical strength, wear resistance, chemical and corrosion resistance, thermal stability, and is dense non-porous. It is used for electrical packaging, bushings, grinding media, wear resistant components, and industrial applications. The tube lining below is made from 92% alumina ceramics.
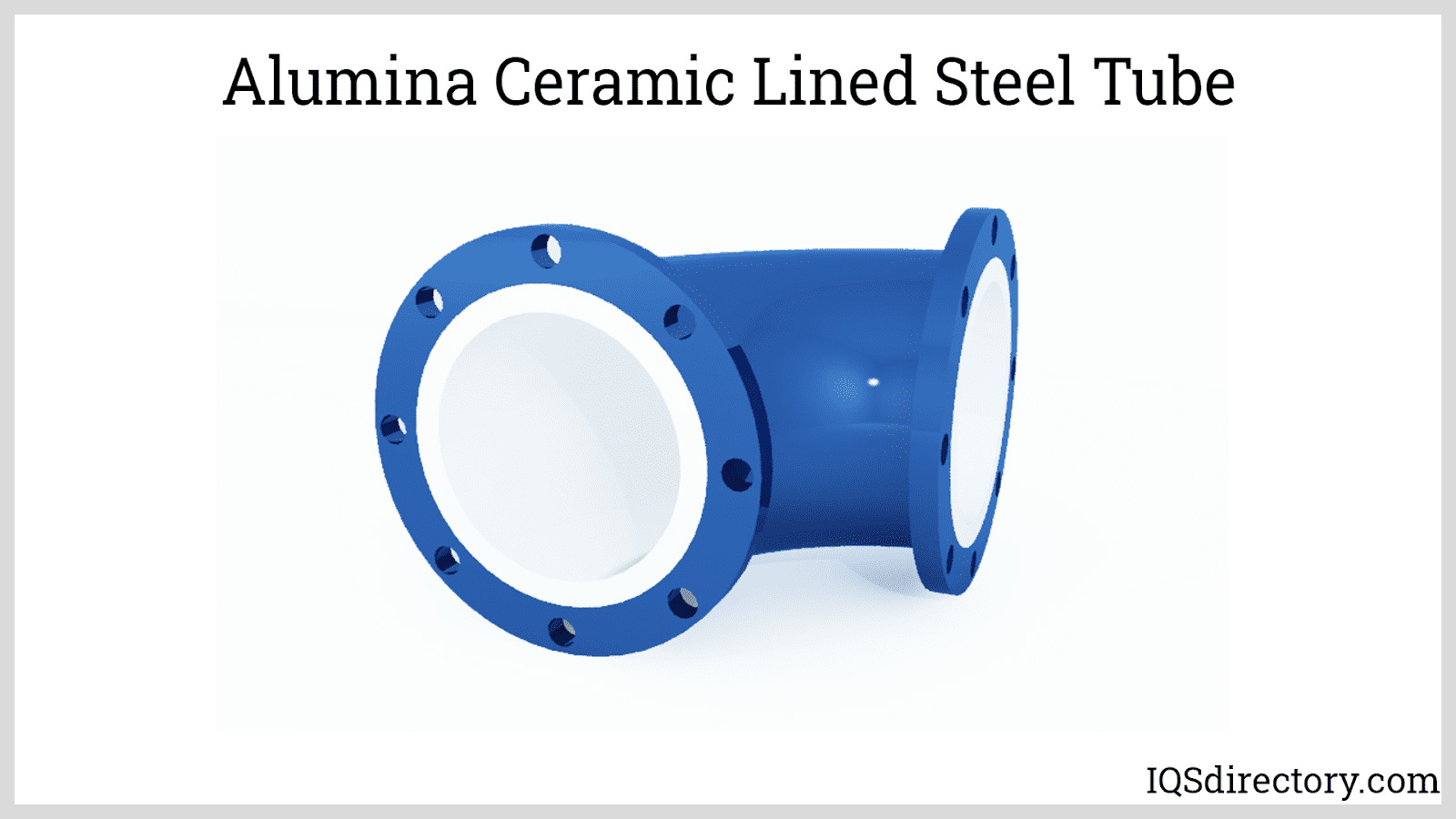
94% Alumina:
has low thermal expansion, high volume resistivity, abrasion and chemical resistance, dielectric constant, and accepts manganese metal coating for high temperature brazing. It can be used as a pressure sensor, bearing coatings, electron tube, and laser components.
95% Alumina:
has similar properties to 94% alumina with added qualities of compressive and flexural strength and excellent hermeticity. It is good for ceramic to metal feed throughs, X-ray component feed throughs, high voltage bushings, and medical implants. This percentage of alumina can be molded into body armor for military applications.
96% Alumina:
is used for medical applications. It has a combination of mechanical, electrical, thermal, and chemical properties. The combination of these properties makes them suitable for wear nozzles, wear guides, blood valves, electrical connector housings, and other industrial applications.
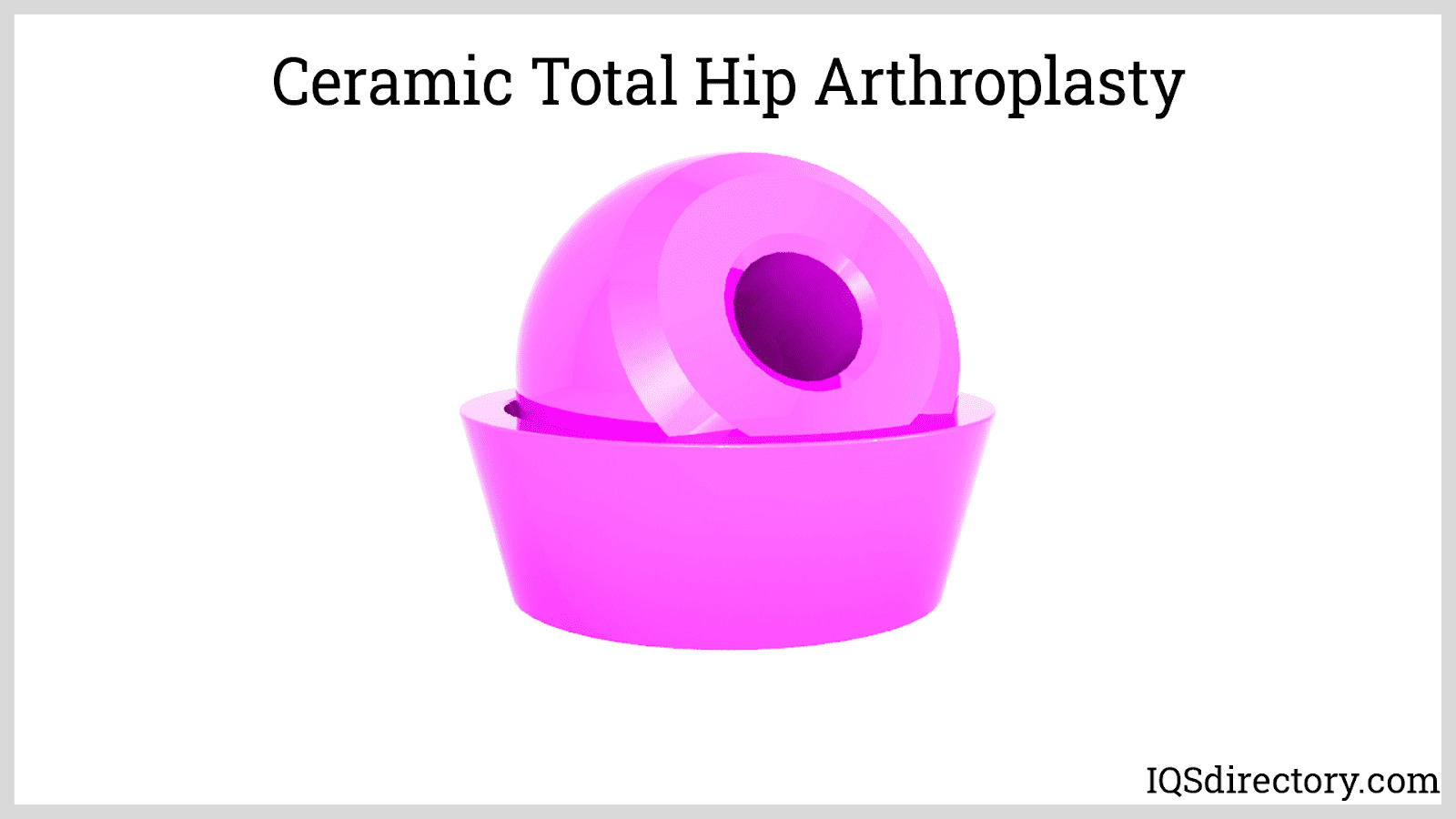
97% Alumina:
can be metal coated for high temperature brazing assemblies and serve as an electrical insulator. It can be used for high vacuum systems, laser equipment, X-ray tubes, electron microscopes, microwave windows, and insulation for medical equipment.
97.5% Alumina:
is a high quality, fine grain alumina used for electrical and mechanical components that need a thick metal coating and where abrasive and chemical resistance is required. It can be used with metal coated components like conductor and resistor networks, and dielectric layers. This percentage of alumina can be used in the defense industry, medicine, and scientific research to name a few.
97.6 Alumina:
is an essential part of components that require operational stability and reliability. It is electrically and dimensionally stable in a wide range of temperatures. It is used for laser components, electro optical devices, flow measurement, sensors, and X ray equipment.
98.6% Alumina:
is a light weight alumina for use as armor for military vehicles and structures. It can stop small arms fire and medium caliber cannon.
99% Alumina:
is extremely hard and is used as a component on rotary and reciprocating pumps that handle chemicals. Shafts, bearings, thrust washers, plungers, and counter face seals on pumps that handle chemicals use 99% alumina material.
99.5% Alumina:
is a very pure form of alumina that is used for semiconductors, semiconductor chambers and fixtures. It has low particle generation and is vacuum tight.
99.7% Alumina:
has a 98% reflectance efficiency at 1064 nanometers (nm) and a 96% reflectance at wavelengths of 500 to 2000 nm making it perfect for laser reflectors. It can be used for pumping chambers for flash lamps and continuous wave lasers.
99.8% Alumina:
is very high purity and has been developed for semiconductors. It has excellent chemical and plasma resistance with dielectric properties for high voltage applications. It can be used for semiconductor applications that include PVD, CVD, and CMP oxide etching, ion implants, and photolithography to name a few. This percentage of alumina has wide use in the semiconductor industry.
99.9% Alumina:
is the ultra-pure alumina, which can be applied in severe applications, such as plasma etching components and nuclear grade insulator components. The properties of 99.9% alumina can be seen in the chart below from CoorsTek.
Properties of 99.9% Alumina
Property | Units | Value |
Flexural Strength, MOR (20 °C) | MPa | 350 - 600 |
Fracture Toughness, KIc | MPa m1/2 | 4.0 - 5.0 |
Thermal Conductivity (20 °C) | W/m K | 28 - 35 |
Coefficient of Thermal Expansion | 1 x 10-6/°C | 8.0 - 8.5 |
Maximum Use Temperature | °C | 1750 - 1800 |
Dielectric Strength (6.35mm) | ac-kV/mm | 8.7 |
Dielectric Loss (tan δ) | 1MHz, 25 °C | 10-4 to 10-3 |
Volume Resistivity (25°C) | Ω-cm | 1014 to > 1015 |
Zirconia Toughened Alumina (ZTA)
Zirconia toughened alumina is produced by combining aluminum oxide with 10% to 20% zirconium oxide. The resulting material has exceptional strength, toughness, hardness, and outstanding wear resistance. It provides a design solution that is less expensive than using zirconia alone, which can cost anywhere from $75 to $400 per carat. The cost of zirconia varies in accordance with its purity and quality.
The transformation process in combining alumina oxide and zirconia oxide is designed to increase the fracture toughness of ZTA. When zirconia is stressed, its particles change their crystal structure, causing a volume expansion that compresses the cracks in the alumina matrix. This process gives alumina exceptional structural strength to meet the needs of a variety of highly stressful applications.
Conclusion
- Alumina ceramic, or aluminum oxide (Al2O3), is an industrial ceramic that has high hardness, is long wearing, and can only be formed by diamond grinding.
- Alumina ceramics are made from a white granular material or a very fine silky dense powder refined from bauxite.
- Alumina is a major engineering material that has excellent mechanical and electrical properties, which makes it applicable for a wide range of uses.
- The powder material for alumina ceramics comes from the processing of bauxite, which is an aluminum rich clay like material located a few meters below the earth’s crust.
No comments:
Post a Comment