What is the Difference Between Iron, Steel, and Cast Iron? (Properties, Applications, and Metallurgy)
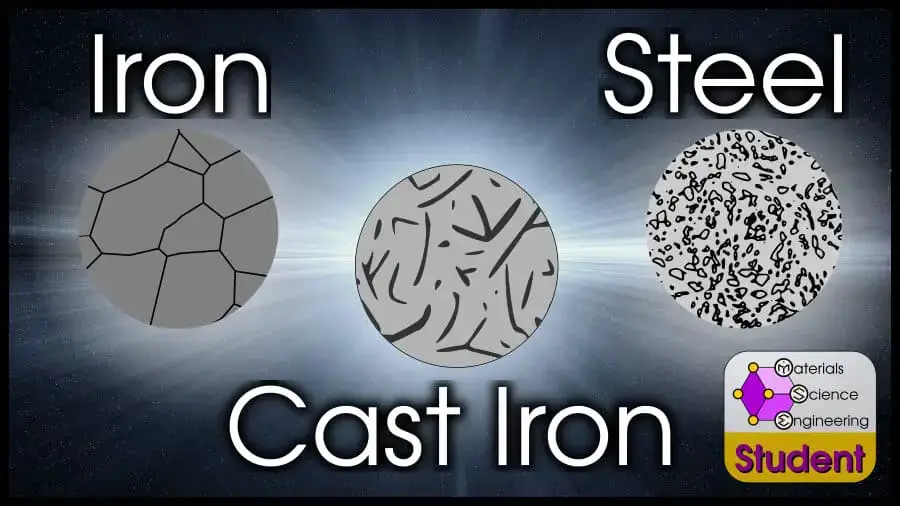
I have been interested in ferrous metallurgy for more than a decade, when I read a bunch of scientific papers about swords for my first open-topic project in middle school. I am tempted to wax poetic about iron alloys, but I will save that for another article. You just want to know the basic differences between iron, steel, and cast iron: so I’ll get to the point.
The difference between iron, steel, and cast iron is the amount of carbon present in the material. Pure iron does not have any carbon, steel is any iron alloy with up to 2 weight percent (wt%) carbon, and cast iron is any iron alloy with more than 2 wt% carbon. In practice, iron alloys will rarely have more than 4 wt% carbon.
Now that you know the definitions of iron, steel, and cast iron, let’s talk about why a tiny amount of carbon makes such a difference.
Outline
Ferrous Metallurgy: The Absolute Basics
Ferrous metallurgy is just the study of iron and iron alloys. Metallurgy tends to be divided between “ferrous” and “nonferrous” because steel is such an important metal.
Not only does steel have some of the best mechanical properties of any material, it’s also cheap and has complex chemistry. Engineers can dramatically change the properties of steel by adjusting compositions and processing techniques.
This article will explore how small changes in carbon content can produce such different results.
Pure iron, or ferrite (ferrite means it’s BCC crystal structure, which is true at room temperature) is a single phase with just iron atoms. Depending on the temperature, iron can dissolve very small amounts of carbon to be in an interstitial solid solution.
As non-trivial amounts of carbon are added to pure iron, steel results. Steel has a mixture of Fe (iron) and Fe3C (cementite). Pure cementite is very strong, but brittle. But if the cementite is surrounded by ductile ⍺-iron, the resulting mixture remains ductile but dramatically increases in strength.
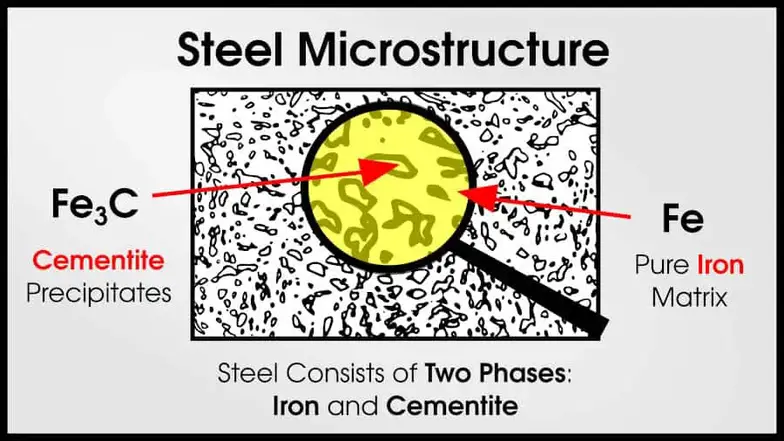
Steels with higher carbon content have a higher fraction of cementite. This makes them stronger, but less ductile. At some point, they entirely lose ductility.
Iron alloys with enough carbon that they lose ductility entirely are called cast iron. Usually, this means it has more than 8.67 at% (2 wt%) carbon. With this much carbon, cast alloys usually have all 3 phases: ferrite (Fe), cementite (Fe3C) and graphite (C).
The different balances of phases in iron, steel, and cast iron contribute to their very different properties.
Properties of Iron, Steel, and Cast Iron
There are a very wide range of properties that these three materials can have. In this article, I’m only talking about the effects of carbon–since that is what differentiates iron, steel, and cast iron–but real alloys may have a dozen other elements.
Even if we stick to basic compositions of iron and carbon, the materials can behave very differently depending on how they are processed. For example, quenching steel may cause martensite to form instead of ferrite. That’s not important to know right now, except to demonstrate that there is not a “universal steel” with certain properties.
Just to scare you, a few types of iron alloys are: TRIP steel, hypereutectoid steel, hypoeutectoid steel, tool steel, stainless steel, austenitic steel, gray cast iron, white cast iron, malleable cast iron, and ductile cast iron.
However, I can make broad generalizations about these materials’ properties.
For example, pure iron is much weaker than steel and cast iron. The cementite precipitates are much stronger than ferrite.
On the other hand, cast iron is much more brittle than steel or pure iron. In steel, having brittle precipitates is not so bad, because a crack would have to travel a large distance to connect these precipitates. In cast iron, the cementite phase is more continuous, so if a crack starts anywhere, it will quickly travel through the entire cementite phase.
Additionally, the graphite in cast iron means that the material is weak when pulled apart (but still strong when compressed!).
Pure iron tends to have the highest melting point, and cast iron has the lowest melting point. However, steel simply has better mechanical properties, so almost all high-temperature applications use steel instead of iron.
Cast iron is the cheapest of the iron alloys. However, since it is so brittle, it is difficult to machine. To make a cast iron part, you usually need to melt the material and pour it into a mold. This process is called “casting,” hence the term cast iron.
Pure iron, ironically, is often more expensive than steels or cast irons. Purifying elemental iron is not a trivial process, and so much more steel and cast iron is created that economies of scale make these materials cheaper.
Pure iron has the best conductivity, but iron has relatively low conductivity compared to other metals like copper or aluminum, so I can’t imagine a situation where you would use pure iron for electrical conductivity.
Without alloying elements, cast iron has the best corrosion resistance. However, there is a type of steel called “stainless steel’ that has chromium in it–this chromium helps prevent steel from rusting (I’ve never heard of stainless cast iron, because why waste “expensive” chromium on a material whose main advantage is price?).
Material | Pure Iron | Cast Iron | Steel |
Melting Point (oC) | 1538 | 1150-1300 | 1425 – 1540 |
Ductility | ductile | brittle | relatively brittle |
Electrical Conductivity | relatively low | low | low |
Cost | relatively expensive | cheap | relatively cheap |
Steel is stronger, harder, tougher, and more brittle than iron.
Applications of Iron, Steel, and Cast Iron
As you may have noticed from my description of their properties, steel has the most applications in engineering. It has superior qualities to most other materials, especially when considering the cost.
Some form of steel is used in almost every structural part, unless density is an issue. Most planes would be made of a lighter material than steel, but the landing gear is still solid steel. Steel is used for buildings, cars, bridges, sewers–you name it, it uses steel.
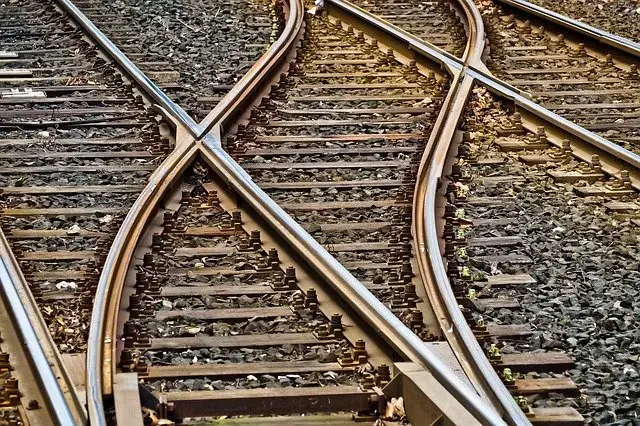
Cast iron is nice because it can be quite cheap. The graphite particles are great for absorbing energy from vibrations, so you may see cast iron frames on machines that vibrate or are sensitive to vibration.
Iron is almost exclusively used to make other things. Pure iron is not nearly as useful as its alloys. Iron has uses in chemistry (for example: as a catalyst in the Haber-Bosch process), but I can’t think of any structural applications for pure iron.
Even if you have heard of “wrought iron,” which is a historical name for something we have surpassed, wrought iron was actually a kind of mild steel. Historically, removing carbon from steel was more difficult than adding carbon back in. Pure iron has not really existed before modern metallurgy and chemistry.
With that said, here is a short quiz that you can check yourself. I’ll list an application, and you decide if this material should be made of steel or cast iron.
Engine block

Cooking pan

Brake discs

Knives or other tools

Reinforced concrete

Pressure vessels

Nails

Final Thoughts and Further Reading
Iron is one of the most important elements of modern society because of all the things you can make with iron. However, pure iron is not that useful on its own.
Adding carbon to iron produces steel, the most widely-used metal. Steel has an excellent combination of mechanical properties and is among the cheapest materials.
Adding even more carbon to iron produces cast iron. Cast iron has some benefit compared to steel–mostly because it has a lower melting point. For parts that need to be cast, cast iron is usually cheaper than steel. Cast iron has flecks of graphite which also helps to dampen vibrations.
No comments:
Post a Comment