Elasticity and Young’s Modulus (Theory, Examples, and Table of Values)
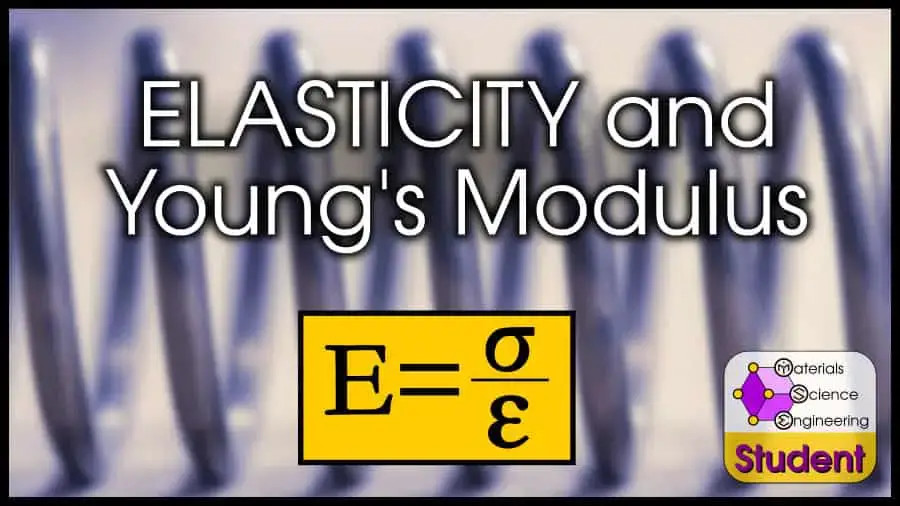
Young’s modulus–the most common type of elastic modulus, seems to be the most important material property for mechanical engineers. It’s pretty important for materials scientists, too, so in this article I’m going to explain what elasticity means, how to calculate Young’s modulus, and why stiffness is so important.
When a material is first exposed to force, it behaves elastically. Elastic behavior means that however the material moves while under load, it returns to its original position when the load is removed. This is true for every material, although sometimes the elastic regime might be really small.
Within the elastic region, a material has stiffness. Stiffness refers to how much force is required for elastic deformation. The inverse of stiffness is called “compliance” (stiffness and compliance have the same relationship as conductivity and resistivity). Different measures of stiffness are called elastic moduli, and the most common elastic modulus is Young’s modulus. (Yes, named after Thomas Young, the guy who developed the double slit experiment).
If you have ever heard of Hooke’s law, you might already know about elasticity.
Outline
- Hooke’s Law as You Learned in High School
- Hooke’s Law with Stress and Strain
- Identifying Young’s Modulus from the Stress-Strain Curve
- Calculating Young’s Modulus
- Elastic Behavior
- Values of Young’s Modulus for Common Materials
- Applications of Young’s Modulus
- Load Distribution
- Final Thoughts
- References and Further Reading
Hooke’s Law as You Learned in High School
Hooke’s law relates force on a spring to the spring’s displacement.
Equation for Hooke’s law:
You could say that applying a force causes elastic deformation in the material. “Deformation” means that the shape is changing, and “elastic” means that when the force is removed, the material returns to its original shape.
Springs are very elastic. You can push them or pull them and the spring displaces, but when the force is removed, the spring returns to its original shape. All materials behave like a spring for at least some small displacement. Hooke’s law applies when a material behaves elastically.
The point of Hooke’s law is that the elastic deformation is proportional to the force applied. The spring constant determines that proportionality, and if you double the force you get double the displacement.
The problem with Hooke’s law is that it only applies to springs. Every spring has a different size, shape, and materia, so it has a different spring constant. Since ,
, and
are extrinsic properties, this equation doesn’t generalize to other materials, or even other sizes..
When we want to measure the elastic behavior of a material–which is important, because every material behaves elastically for some portion–we need to rewrite Hooke’s law to depend on intrinsic properties.
Hooke’s Law with Stress and Strain
Intrinsic properties are properties that depend only on the material–not how much of the material there is. For example, the mass and volume of steel will be different for every single piece of steel, so they are extrinsic properties.
On the other hand, the ratio of mass and volume–or density–is constant. Whether you have a steel ball bearing or a piece of a skyscraper, the material density is the same, so it’s an intrinsic property.
The intrinsic analogues of force and displacement are stress and strain.
Stress is just the force divided by the cross-sectional area.
Strain is just the change in displacement divided by the original length.
Extrinsic Properties | Intrinsic Properties | ||
---|---|---|---|
Force | Displacement | Stress | Strain |
The new version of Hooke’s law is
Now we have , which is called Young’s Modulus or the modulus of elasticity. Young’s modulus provides the linear relationship between stress and strain. Young’s modulus is the same for any material–you could take a spoon or a girder; as long as they have the same young’s modulus and you knew their sizes, you could predict how much force would cause a certain amount of elastic deformation.
Since stress is a unit of pressure (usually expressed in MPa, or ) and strain is dimensionless, Young’s modulus is also a unit of pressure. It is typically expressed in GPa, or 1000 MPa.
You may also have heard of other elastic constants, such as the shear modulus, bulk modulus, , etc., but these all function in the same way. If you want to learn more about these other elastic constants, you can read a full explanation in the upcoming article.
Identifying Young’s Modulus from the Stress-Strain Curve
Young’s modulus specifically applies to tension, or pulling forces. The way we test this is with a tensile test, which basically just applies a strain and measures the stress.
If you want to know why strain is the independent variable (instead of stress) or you have any other questions about the stress-strain curve, I suggest you read this article.
I’ll also provide a quick recap in collapsable text here:
The straight-line portion of the graph–where stress and strain have a linear relationship , is called the elastic regime. Hooke’s law only applies in this elastic regime. The slope of this line–represented by
in Hooke’s law, is Young’s modulus.
Young’s modulus tells you exactly how much force will produce a certain displacement, as long as the material is still in the elastic region.
Calculating Young’s Modulus
Young’s modulus is just the slope of the linear portion of the stress-strain curve. Slope is
So just pick any two points on the linear portion, divide the difference in y-values by the difference in x-values, and you have your modulus of elasticity!
Remember, this modulus is called “Young’s modulus” when the stress-strain graph shows pure tension, but “modulus of elasticity” is a broad term that refers to stiffness in any direction.
Elastic Behavior
In the elastic regime, atomic bonds are being stretched. It turns out that atomic bonds behave similarly to springs, which is why there is a linear relationship between stress and strain here (and yes stretching atomic bonds means that volume is NOT conserved in the elastic regime).
Atomic bonds can stretch and perfectly return to their original shape, which is why this kind of deformation is called elastic deformation.
The opposite of “elastic deformation” is “plastic deformation,” which means that the material does not return to its original shape.
You can see this in the image below.
This stress-strain curve shows the force on the y-axis, and the deformation on the x-axis. The dotted line shows the relationship between force and deformation all the way until the material breaks, but imagine that we didn’t want to break the material.
The graph on the left shows that we add some force and then remove it. Since we stay in the elastic region, atomic bonds simply stretch and return to their original position.
The graph on the right extends the stress past the yield point, which is when the atoms have to move past each other to continue deformation. If you remove the stress, the bonds will relax and some deformation will reverse, but atoms that have moved past each other are now stuck.
Specifically, the yield point is where the stress-strain curve has a 0.2% offset from the Young’s modulus.
Engineers use this 0.2% offset to have an easily-identifiable point on the stress-strain curve. Technically what I’ve been describing so far is called the “proportionality limit” which is the exact point that stress and strain are no longer perfectly linear, but in practice this point is usually impossible to determine.
Values of Young’s Modulus for Common Materials
Before we talk about applications of stiffness, take a look at this table that shows values of Young’s modulus for common materials.
Material | Young’s Modulus (GPa) |
Aluminum | 69 |
Cobalt | 207 |
Concrete | 17 |
Copper | 117 |
Diamond | 1220 |
Glass | 50-90 |
Gold | 74 |
Iron | 210 |
Lead | 14 |
Magnesium | 45 |
Molybdenum | 329 |
Nickel | 170 |
Niobium | 103 |
Platinum | 147 |
Low-density Polyethylene (LDPE) | 0.1 – 0.45 |
Polyvinyl chloride (PVC) | 2.4 – 4.1 |
Rubber | 0.01-0.1 |
Silicon carbide (SiC) | 450 |
Silver | 72 |
Tin | 47 |
Tungsten | 400 |
Here are also two Ashby charts that show elastic modulus on one axis, and other properties on another axis.
Since stiffness is a good approximation of bond strength, it is closely related to melting point. Stiffness is not closely related to strength, since bond strength is only one factor in a material’s overall strength.
Applications of Young’s Modulus
When selecting materials, engineers need to control a variety of properties. Cost, operating temperature range, strength, corrosion resistance, and more. For many applications, the most important property is stiffness.
Analogy to Strength
Young’s modulus–or stiffness– is NOT strength. However, it does relate to strength. In most engineering applications, “strength” means yield strength–or the point where elasticity breaks down. Assuming similar yield stresses, higher Young’s modulus will result in higher yield strengths. (But yield stresses can vary quite dramatically).
When you design a part which is limited by strength, what you really mean is that the part must be able to survive a specific force without suffering damage.
If you made a pull up bar, it needs to have enough strength to withstand a person’s bodyweight. As far as engineering applications go, human bodyweight is not that demanding. Nylon is about ⅓ as strong as steel, so from a strength perspective either one would work.
However, the bar should also not move when a person gets on it. Nylon is about 1/100 as stiff as steel, which is why you don’t make pullup bars out of nylon. They would bend too much!
Young’s modulus describes how far something deforms elastically per given force, not how much force it can withstand.
So now you can see that one of the biggest applications of Young’s modulus is to calculate small elastic deformations.
Calculation of Deformation
Although people talk about how “strong” something is, in many cases they are actually interested in the stiffness.
You can use elastic modulus to calculate how far something will deform elastically. For example, imagine a door on a hinge.
The metal hinge needs to keep the door straight enough that it doesn’t bend and touch the floor. If you know the tolerance that the door has, an expected weight on the door (+ a huge safety factor), and the elastic modulus of your hinge material, you can calculate how thick the material needs to be!
Stiffness-Limited Design
Stiffness-limited design refers to applications where stiffness is the main property of interest. Examples of stiffness-limited design applications are support beams (or shafts, or struts), columns, panels, and pressure vessels. These can also be strength-limited–it depends on the other circumstances.
For example, the situation with the door hinge would be stiffness-limited because the wooden door will fail in strength before the hinge does. If you kept putting force on the door, it would either fail because the wood cracked and the screws ripped out, or it would fail because the hinge bent enough that the door touched the floor.
Elastic energy stored
Another reason to use very stiff materials is for elastic energy storage. Do you remember the equation for potential energy of a spring, ? Yup, you can just replace the
with an elastic modulus and
with strain.
Most engineering applications of elastic energy storage are based on springs, but now you know which materials will work best! You can also think about elastic energy storage if you were making a bow for archery.
Load Distribution
If you have multiple materials that support a load together, the materials with the highest elastic modulus will also bear the highest load.
This has implications that go far beyond architectural column design. For example, this phenomenon is one reason why steel is such a bad material for prosthetic implants.
When doctors first began replacing body parts with steel prosthetics, the stiff steel would support most of the patient’s weight. Since the surrounding bones were not be required to support much load anymore, they became very weak and the patient developed further problems.
Today, prosthetics are carefully engineered so that the prosthetic’s elastic modulus matches the elastic modulus of human bone.
Modulus of Resilience
Modulus of Resilience is like toughness, but just for the elastic regime. It tells you how much energy can be absorbed before the material has permanent deformation.
Modulus of Resilience:
where
Resilience is good for storing elastic energy. Springs should be made from a material with a high modulus of resilience.
Assuming this area is a right triangle (which introduces slight error), then
so highly resilient materials need a high yield strength and low elastic modulus.
Speed of Sound
You might not have expected this one! The speed of sound is related to a material’s stiffness and density. Acoustic Engineers would need this information when designing auditoriums.
I don’t have much more to say about this, but it’s just one example of where stiffness comes up that you might not expect!
Final Thoughts
Stiffness is one of the most important mechanical properties. Stiffness can be determined by calculating the slope of a stress-strain diagram, and it tells you how far a material will bend under a given force.
Ceramics usually have very high stiffness, and polymers have very low stiffness.
Very stiff materials are useful for a variety of applications where engineers don’t want materials to bend. Although strength is the first mechanical property most people think about, stiffness-limited design is just as common as strength-limited design.
No comments:
Post a Comment