Introduction
Friction stir welding (FSW) is a solid-state joining process developed at TWI Ltd in 1991. FSW works by using a non-consumable tool, which is rotated and plunged into the interface of two workpieces. The tool is then moved through the interface and the frictional heat causes the material to heat and soften. The rotating tool then mechanically mixes the softened material to produce a solid-state bond. The FSW process is illustrated in Figure 1.
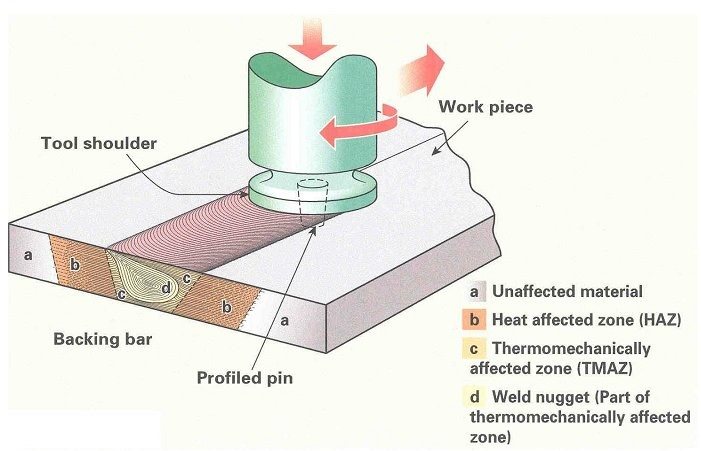
Applications
FSW is mainly used in industry to join aluminium alloys of all grades, in cast, rolled or extruded condition. Aluminium alloy butt joints with a thickness from 0.3mm to 75mm have been successfully joined in a single pass (dependent on workpiece material, machine power and structural stiffness). Other materials have also been successfully joined, namely magnesium, titanium, copper, and steel alloys. Plastics and metal matrix composites (MMC) have been explored. Dissimilar combinations between these materials have also proven possible.
Since its invention, FSW has become a proven technology in most manufacturing sectors. Some of its known applications include:
Shipbuilding and Marine
- panels for decks, sides, bulkheads and floors
- hulls and superstructures
- helicopter landing platforms
- masts and booms
Aerospace
- fuselage and wing structures
- fuel tanks for space vehicles
Railway industry
- rail stock vehicle floor, side and roof panels, namely for high-speed trains
- railway tankers
Automotive
- battery trays
- invertors
- engine chassis cradles
- wheel rims
- tailor welded blanks
- car body structures
- seat frames
Electronics
- enclosures for circuits
- cooling and thermal management plates
- Apple’s iMac computer body
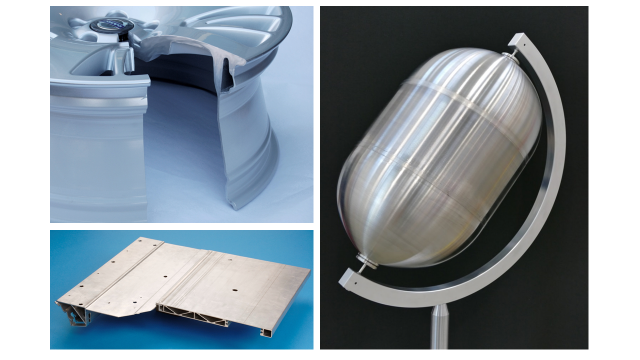
Microstructure and Mechanical Properties
Friction stir welds typically exhibit three main microstructural regions: a weld nugget, a thermo-mechanically affected zone (TMAZ) and a heat-affected zone (HAZ). Technically, the weld nugget and TMAZ are both “thermo-mechanically affected zones,” but are considered separately for exhibiting distinct microstructural features. The weld nugget experiences dynamic recrystallisation while the TMAZ does not. The extent and microstructural composition of these zones are dependent on the material and processing conditions (parameters and tool design, for example). Figure 1 provides an illustration of these zones.
With regards to the mechanical properties of friction stir welded aluminium alloys, it is now well established that they are generally superior to those obtained by arc welding processes.
There are two main standards that describe the guidelines for use:
AWS D17.3/D17.3M 2021 “Specification for Friction Stir Welding of Aluminum Alloys for Aerospace Applications”
And
ISO 25239:2020 Friction stir welding — Aluminium
process.
Advantages
Friction stir welding offers many advantages over fusion-based joining processes, especially when joining aluminium alloys:
- Remaining in the solid-state, avoiding many of the defects associated with melting and solidification during fusion welding, such as pores and solidification cracks.
- The peak temperatures are lower, allowing a reduction in distortion and shrinkage.
- Being able to join many ‘non-weldable’ aluminium alloys, namely from the 2xxx and 7xxx series.
- Producing superior mechanical properties.
- No filler metals, flux or shielding gas are required. No fumes, porosity or spatter are generated.
- Fully automated, making the process highly repeatable.
- Energy efficient.
- Does not require special edge preparation in most applications.
Friction Stir Welding (FSW) – Process & Applications
Friction stir welding (FSW) was first introduced in 1991. This is a solid-state process of joining two parts. In this process, the metal parts do not melt. Instead, welding friction between the metal parts and the FSW tool creates heat which allows the atoms of the two metal parts in order to fuse.
FSW, nowadays, is widely used for welding aluminum alloys and also other metal or metal alloy parts. FSW can be used to join parts made of the same metal as well as two different metal parts.
Process of FSW
The ‘tool’ of FSW is the most important part of the process. It is cylindrical and has a probe (a pin with a diameter smaller than the tool shoulder). The step-by-step process is:
- Firstly, two metal workpieces are kept in the friction stir welding machine side by side in order to make a butt joint.
- The tool then rotates and goes into the two clamped workpieces.
- The tool creates a hole in the middle of the joint and penetrates long enough so that the tool shoulder can touch the surface of the workpieces.
- After that, the tool dwells for a short time and then starts to move forward.
- The welding friction between the wear-resistant tool and the job parts creates heat. which makes the metal soft but doesn’t melt the metal.
- Dynamic recrystallization occurs on the workpiece material which causes severe solid-state deformation and attaches the two workpieces at a microstructural level.
This is how the whole friction stir welding process works.
Friction Stir Welding Tool Design
Designing the tool is very important because the welding speed and quality depend on the tool. Some important facts/criteria for the FSW tool are:
- The tool should be tough, strong, and have a melting point temperature high enough to withstand the welding temperature.
- The thermal conductivity of the tool should be very low so that no heat loss occurs.
- Tool Steel (AISI H13) is perfect for friction stir welding of alloys of aluminum whose thickness ranges from 0.5 to 50 mm.
- ‘Whorl’ design friction stir welding tools have variable pitch thread. It uses a tapered pin that has re-entrant features. This design improves the material’s downward flow.
- Triflute design (three tapering systems) improves the movement of material around the tool.
- Trivex tool design is simpler. During welding, this design helps to lower the forces that act on the tool.
- The concave shoulder profile design of the tool helps to reduce scrap and maintain downward pressure.
FSW Tool Speeds
There are two types of speed for the FSW tool such as rotational and translational speed. It is very important to choose these speed parameters carefully in order to make the welding cycle more efficient.
The workpiece material should be hot enough so that less force is required in order to make the bond. Faster rotation and slower translation of the tool will result in high heat production.
If the material is too cold or too hot, there will be defects in the final part. So, the heat should be at an optimum level. To reach that optimum level, the rotational and the translational speed should be optimized.
Applications of FSW
FSW welding is widely used in many industries for joining various metal components. The following industries use friction stir welding for its benefits:
Automotive Industry
Many components in the automobile industry such as motors, battery pack boxes, automobile engine frames, DC/DC converter, airbag inflator, etc. require FSW. Fully loaded airbag inflators can easily be welded due to the narrow heat-affected zone of FSW welding.
Network and Communication Industry
Various telecommunication device parts, 5G communication components, etc. requires friction stir welding for joining two parts. Many friction stir welding companies around the world make parts for this industry.
Aerospace Industry
In the aerospace industry, a low compression rotor is joined with a tube using the friction stir welding process. Cluster gear and many other components in this industry also require friction stir welding.
Marine Industry
Many large and small projects in the Marine industry use friction stir welding to speed up the construction. This saves a lot of time as well as increases the profit. Some examples where FSW is needed in this industry are flooring, deck, bridges, seawalls, panels, bulkheads, walkways, etc.
Agricultural industry
Many components in the agricultural industry such as water pumps, water pump gear, diesel engines, etc. need FSW. The friction stir welding companies can reduce the costs of agricultural components significantly for the agricultural industry.
Sunrise Metal – Friction Stir Welding Parts Manufacturer in China
Sunrise metal is one of the top friction stir welding suppliers and parts manufacturers in China. We provide friction stir welding services for many industries such as automotive, aerospace, marine, telecommunication, etc. Our goal is to achieve customer satisfaction by providing a one-stop solution for FSW welding parts.
Sunrise Metal’s friction stir welding services include:
Part Design and Development
We have experts in our team who have decade-long experience in this field. They always work to develop the parts for our clients and also design new parts from scratch if necessary. Our clients can rely on our team without worrying about the quality of the design or the parts.
FSW Parts Manufacturing
Our facilities own one of the advanced friction stir welding machines of this era, the TS-1260. This machine is capable of precisely joining the same and different types of metals. We use this to make FSW parts for our clients.
Die Casting
If our client requires, we can manufacture the metal FSW workpiece part by part using modern semi-solid die casting, high pressure die casting, vacuum casting, etc. processes. Then we can join the parts using the FSW process which makes the final component very strong and reliable.
Finishing Operations
Aside from the above services, we also provide surface finishing services for the finished parts. We do this to make the parts corrosion resistive, stronger, and long-lasting.
So, these are our friction stir welding services. As you can see, we provide different services so this saves a lot of costs. Our clients are happy to take our services because we always focus on the quality as well as on-time delivery. For this reason, Sunrise metal is one of China’s top friction stir welding suppliers.
What Are Some Common Features of FSW?
Following are the features of the FSW welding process:
- Friction stir welded parts show better mechanical properties. For example, friction stir welding aluminum alloy parts have better mechanical properties than arc welding aluminum parts.
- FSW parts mainly have three microstructural regions such as heat-affected zone (HAZ), thermomechanical affected zone (TMAZ), flow arm zone, and weld nugget or stir zone.
- The tool shoulder pulls some material from the upper surface of the weld part at the time of welding. This zone is known as the flow arm zone.
- Dynamic crystallization occurs in the weld nugget zone but does not occur in the thermomechanical affected zone.
- The HAZ zone of FSW parts is similar to other types of welded parts. This zone is affected by the friction heat but does not deform.
- The TMAZ zone appears on both sides of the weld nugget. Unlike weld nugget, its microstructure is recognizable.
What are the Advantages of the FSW Process?
There are many friction stir welding advantages, for example:
- The low-temperature results in less distortion and shrinkage of parts. So, the part dimensions are more accurate.
- FSW parts are highly defect-free. Defects such as solidification crack, porosity, or hot crack do not occur in these parts.
- FSW is environmentally friendly as it doesn’t produce any UV radiation, spatter, or fumes.
- For the friction stir welding of aluminum alloys, it is not mandatory to have any shielding gas, flux, or filler materials.
- The friction stir welding process is very energy efficient.
- It is easy to make this process automatic using the latest machine tool technology which reduces the labor cost.
- FSW parts do not require any expensive machining after welding.
- This process is suitable for joining many 2000 and 7000 series aluminum alloys that are not weldable by other welding processes.
So, these are the most significant friction stir welding advantages.
What Materials Can Be Welded Using the Friction Stir Welding Process?
The friction stir welding process is suitable for various materials. For example,
Aluminum
Before the invention of friction stir welding, some grades of aluminum were not weldable, for example, the 2000 series and the 7000 series aluminum. So, FSW was invented for these grades of aluminum and its alloys. Friction stir welding aluminum parts exhibits much better mechanical properties than other types of welding aluminum parts.
Copper and Its Alloys
Copper has high electrical and thermal conductivity. For this reason, it was very difficult to weld copper parts. But with the invention of FSW, it has become very easy to weld copper and its alloys.
Magnesium
It was very difficult to carry out the welding process of magnesium using fusion techniques. FSW helped to overcome this difficulty and now magnesium parts can easily be welded with FSW welding.
Steel and Ferrous Alloys
Friction stir welding of ferrous alloy and steel helps to reduce the rectification costs as well as distortion. FSW Steel parts have fewer defects which are economical for production.
Titanium
Other types of welding processes can be applied to titanium parts. But the problem occurs when there is a poor weld quality or workpiece distortion. FSW shows no such problem and is the best option for welding titanium parts.
Hafnium and Zirconium
Various industries such as power generation, oil refining, and petrochemical industries use these two metals. In these industries, FSW helps to join parts made of hafnium or zirconium easily and effectively.
Why Friction Stir Welding is Known as a Green Technology?
There are many reasons why friction stir welding is known as a green technology. The most significant reasons are:
- There is no requirement of shielding gas in order to weld low melting point temperature materials in FSW.
- FSW eliminates grinding wastes.
- The requirement for cleaning weld surfaces is very mild in FSW.
- FSW does not require degreasing so there is no need for any solvents.
- There is no occurrence of harmful emissions in the friction stir welding process.
To sum it up, FSW doesn’t provide any negative impact on the environment by emitting harmful gases or by any other means. For this reason, it is green technology.
What Are the Differences between Friction Stir Welding and Fusion Welding?
Fusion welding is the general term for different welding processes such as SMAW, GTAW, MIG welding, etc. The below table shows the differences between Friction Stir Welding and Fusion Welding:
Friction Stir Welding | Fusion Welding |
This is a solid-state welding process. | This is a liquid-state welding process. |
Here, the workpiece material doesn’t melt. | The workpiece material melts in this process. |
2000 and 7000 series aluminum alloys are weldable with this process. | 2000 and 7000 series aluminum alloys are not weldable with this process. |
The friction between the workpiece and the FSW tool produces heat for welding. | Electricity or other sources of power produces heat for welding. |
This is cheaper than fusion welding. | This is costlier than friction stir welding. |
The weld quality is better than fusion welding. | The weld quality is not so good as friction stir welding. |
This is more eco-friendly than fusion welding. | This is less echo-friendly than friction stir welding. |
What are the Differences between Friction Welding (FRW) and Friction Stir Welding (FSW)?
When it comes to friction stir welding vs friction welding, there are a few differences. The below table shows these differences:
Friction Stir Welding | Friction Welding |
Here an FSW tool is used which has a probe and a shoulder. | No tool is used in this process. |
The friction occurs between the tool and the workpieces. | The friction occurs between the two workpieces. |
Here the tool rotates and then moves along the joint axis to create the friction and heat to join the two parts. | Here the two workpieces (face to face) move up and down which creates friction and also heat between the surfaces. |
This process produces heat-affected zones (HAZ). | This process does not produce heat-affected zones (HAZ). |
Complex shapes are weldable with this process. | There are some limitations in welding complex parts with this process. |
In short, it can be said that the FSW process is more advanced than the FRW process.
No comments:
Post a Comment